Styrofoam has long been a popular material in construction, widely recognized for its potential as an insulator. But how effective is it truly? This blog post will delve into the properties of Styrofoam to determine if it lives up to its reputation as a good insulator.
We’ll explore its thermal resistance, durability, and common applications, helping you understand its benefits and limitations for various insulation needs.
What is Styrofoam Insulation?
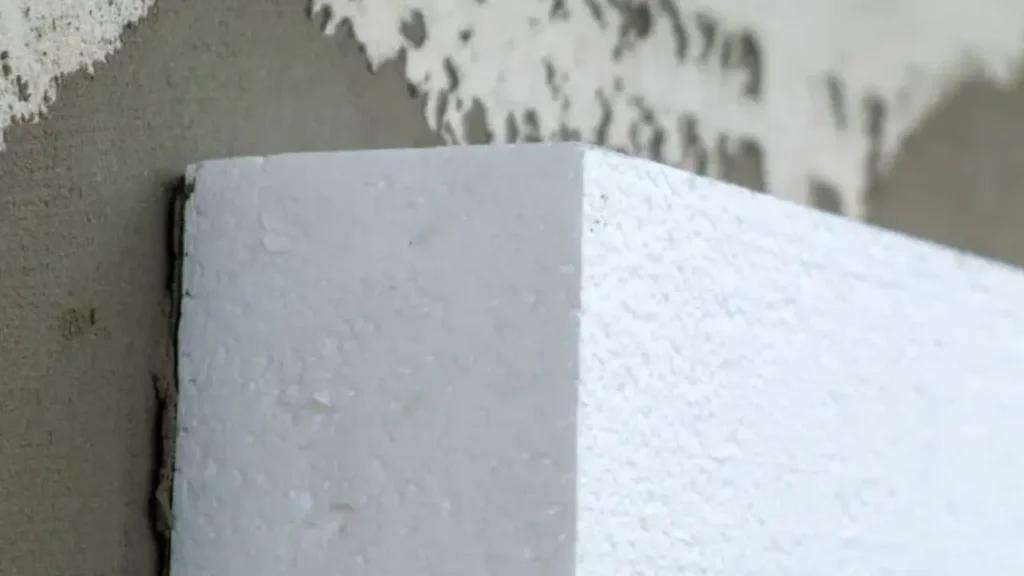
Styrofoam insulation, often recognized by its distinctive blue or white color, is a common building material made from extruded polystyrene (XPS) foam or expanded polystyrene (EPS) foam.
It is widely used in construction due to its excellent thermal resistance properties, which help to reduce heat transfer and improve a building’s energy efficiency. Its closed-cell structure makes it resistant to moisture and provides a rigid, durable barrier, making it suitable for various applications, including walls, roofs, and foundations.
Is Styrofoam a Good Insulator?
Yes, Styrofoam is generally considered a good insulator due to its excellent thermal properties. Its effectiveness stems from its cellular structure, which traps air and creates a barrier against heat flow.
Here’s why it’s a good insulator:
- Lightweight and Easy to Install: Its light weight and rigidity make it easy to handle and install, contributing to its widespread use in construction.
- Low Thermal Conductivity: Styrofoam has a very low thermal conductivity, meaning it doesn’t easily transfer heat.
- Closed-Cell Structure: The trapped air within its closed-cell foam structure significantly reduces heat convection.
- Moisture Resistance: Its resistance to moisture helps maintain its insulating properties over time, as water can reduce insulation effectiveness.
What is Better Insulation Fiberglass or Styrofoam?
When comparing Fiberglass and Styrofoam as insulation materials, both offer effective thermal resistance but have distinct characteristics that make them suitable for different applications.
Here’s a breakdown:
- Styrofoam (XPS or EPS): As a rigid foam board, Styrofoam offers a higher R-value per inch compared to fiberglass, making it more thermally efficient in thinner applications. It’s also resistant to moisture and air infiltration, providing a strong thermal and vapor barrier. However, it’s less flexible for intricate spaces and generally more expensive per square foot than fiberglass.
- Fiberglass: Typically made from fine glass fibers, fiberglass is excellent for insulating irregularly shaped spaces due to its flexibility. It’s cost-effective and provides good sound dampening, but its R-value (a measure of thermal resistance) can decrease if it gets wet, and installation often requires protective gear.
What Makes Styrofoam a Good Insulator?
Styrofoam’s effectiveness as an insulator primarily stems from its unique cellular structure. It is composed of numerous tiny, trapped air pockets within its expanded or extruded polystyrene foam matrix.
Air is an inherently poor conductor of heat, and by trapping it, Styrofoam significantly reduces the transfer of thermal energy through conduction and convection. This closed-cell composition also makes it highly resistant to moisture absorption, ensuring that its insulating properties are maintained even in damp conditions, unlike some other materials whose performance can degrade with water exposure.
What is the R Value of Styrofoam Insulation?
The R-value of Styrofoam insulation varies depending on the type of polystyrene foam. Expanded Polystyrene (EPS) typically offers an R-value ranging from R-3.6 to R-4.2 per inch of thickness.
Extruded Polystyrene (XPS), which is the denser, usually blue or pink foam board often referred to as Styrofoam, generally provides a higher R-value of approximately R-5.0 per inch. This R-value indicates its resistance to heat flow; a higher number signifies better insulating performance.
How to Cut Styrofoam Insulation?
Cutting Styrofoam insulation properly ensures clean edges and efficient installation for your projects. This guide outlines the key steps to achieve precise cuts, minimizing waste and maximizing the effectiveness of your insulation.
Step 1: Gather Your Tools
Before starting, collect the necessary tools for cutting Styrofoam. This typically includes a utility knife, a long straightedge or T-square, a measuring tape, and a marker. Ensure your utility knife has a sharp blade, as a dull blade can tear the foam rather than cut it cleanly, leading to rough edges and an unprofessional finish.
Step 2: Measure and Mark
Accurate measurements are crucial for a successful cut. Use your measuring tape and marker to precisely mark the desired dimensions on the Styrofoam board. Double-check your measurements to prevent errors. For straight cuts, use a straightedge or T-square to draw a clear, continuous line across the board, providing a guide for your knife.
Step 3: Secure the Styrofoam
To ensure a safe and precise cut, stabilize the Styrofoam board. Place it on a flat, sturdy surface, ensuring it won’t shift during cutting. You can use clamps or simply hold it firmly in place with one hand, applying even pressure. This prevents the board from moving, allowing for a cleaner and more controlled cutting action.
Step 4: Make the Cut
Align your utility knife with the marked line, using the straightedge as a guide. Apply steady, even pressure and make multiple passes with the knife rather than trying to cut through in a single stroke. This technique helps achieve a smooth, clean edge and reduces the likelihood of cracking or tearing the foam, especially on thicker boards.
Step 5: Clean Up and Finish
Once the cut is complete, carefully remove any excess foam or debris from your workspace. Inspect the cut edge for any imperfections. For a smoother finish, you can gently sand the edges if necessary. Properly dispose of Styrofoam scraps and store your tools, ensuring they are ready for your next insulation project.
How to Install Styrofoam Insulation?
Installing Styrofoam insulation can significantly improve your building’s energy efficiency. This guide outlines the essential steps for proper installation, ensuring maximum thermal performance and a secure, long-lasting insulating barrier.
Step 1: Prepare the Surface
Before installing Styrofoam insulation, ensure the surface is clean, dry, and free of any debris, dust, or moisture. Any irregularities on the surface should be smoothed out to allow for flush installation of the foam boards. A clean and even surface is crucial for proper adhesion and optimal performance of the insulation, preventing air gaps and thermal bridging.
Step 2: Measure and Cut
Accurately measure the areas where the Styrofoam boards will be installed. Transfer these measurements to the Styrofoam sheets and use a utility knife or hot wire cutter to cut the boards precisely to size. Precise cutting minimizes gaps, which are potential areas for heat loss, and ensures a snug fit, enhancing the overall insulating effectiveness of the system.
Step 3: Apply Adhesive or Fasteners
Depending on the application, secure the Styrofoam boards using an appropriate adhesive or mechanical fasteners. For walls, a construction adhesive designed for foam insulation is often used, applied in beads or dollops. For foundations or exterior applications, specialized fasteners might be required to ensure the boards are firmly attached and can withstand environmental conditions.
Step 4: Install the Boards
Carefully press the cut Styrofoam boards into place, ensuring they fit tightly against each other and the prepared surface. Minimize any gaps between boards by pushing them together firmly. For multiple layers, stagger the seams between layers to further reduce air infiltration and improve thermal performance. Proper alignment is key for a continuous insulation layer.
Step 5: Seal Gaps and Seams
Once all the Styrofoam boards are in place, seal any remaining gaps, cracks, or seams with appropriate foam sealant or tape. This step is critical for preventing air leakage, which can significantly compromise the insulation’s effectiveness. Sealing ensures a continuous thermal envelope, maximizing energy savings and preventing moisture intrusion into the insulated area.
Styrofoam Insulation Cost
Styrofoam insulation costs can vary based on several factors, including the type of foam (EPS or XPS), thickness, R-value, and the quantity purchased. Generally, these rigid foam boards are a cost-effective insulation option, but prices can fluctuate regionally and depending on whether you’re buying retail or wholesale.
Here are some general cost considerations:
- Bulk Purchases: Buying in larger quantities, especially wholesale, can significantly reduce the per-unit cost.
- Expanded Polystyrene (EPS): This type is typically more affordable, with costs ranging from approximately $0.30 to $0.50 per square foot for standard thicknesses.
- Extruded Polystyrene (XPS): XPS, often recognized by its blue or pink color, usually has a higher R-value per inch and is therefore slightly more expensive, ranging from about $0.40 to $0.70 per square foot.
- Thickness and R-value: Thicker boards with higher R-values will naturally cost more per sheet.
Can You Paint Styrofoam Insulation?
Yes, you can paint Styrofoam insulation, but it’s crucial to use the right type of paint to avoid damaging the foam.
Oil-based paints and spray paints containing harsh solvents can dissolve or melt Styrofoam. Therefore, it is highly recommended to use water-based paints, such as acrylic latex paints, which are safe for foam surfaces. Always apply paint in thin, even coats, and consider using a primer specifically designed for foam to ensure better adhesion and a more uniform finish.
Styrofoam vs Fiberglass Insulation
Choosing between Styrofoam and fiberglass insulation involves understanding their distinct properties and benefits. Both materials offer effective thermal resistance, but their applications, performance characteristics, and installation methods differ significantly, making each suitable for specific insulation needs and project requirements.
R-Value (Thermal Performance)
Styrofoam, particularly extruded polystyrene (XPS), generally offers a higher R-value per inch compared to fiberglass batting. This means that a thinner layer of Styrofoam can provide similar or even superior thermal resistance to a thicker layer of fiberglass. Fiberglass’s R-value can also be compromised if it becomes wet or compressed, whereas Styrofoam maintains its insulating properties more consistently.
Moisture Resistance
Styrofoam boasts excellent moisture resistance due to its closed-cell structure, which prevents water absorption. This makes it ideal for applications where moisture exposure is a concern, such as foundations, below-grade walls, and basements. Fiberglass, being an open-cell material, can absorb water, which significantly reduces its insulating effectiveness and can lead to mold growth if not properly managed.
Installation and Flexibility
Fiberglass insulation, especially in batt or roll form, is highly flexible and can easily be fitted into irregular cavities, around pipes, and through tight spaces. This makes it a popular choice for existing wall cavities and attics. Styrofoam, available in rigid boards, is less flexible but provides a continuous, uniform barrier that is easier to install on flat, open surfaces like exterior walls and roofs.
Durability and Compression
Styrofoam is a rigid and durable material that maintains its shape and R-value over time, even under light compression. It’s less prone to sagging or settling, ensuring consistent performance. Fiberglass, particularly unfaced batts, can settle or become compressed over time, which can reduce its R-value and leave uninsulated areas, affecting the overall thermal envelope of the structure.
Cost
Generally, fiberglass insulation is more cost-effective per square foot than Styrofoam, making it an attractive option for large-scale projects where budget is a primary concern. While Styrofoam might have a higher upfront cost, its superior R-value per inch, moisture resistance, and long-term durability can offer better overall value and energy savings in specific applications, leading to lower energy bills over time.
Conclusion
In conclusion, Styrofoam proves to be a highly effective insulator, offering significant thermal resistance, durability, and versatility for various construction and insulation needs. Its lightweight nature and ease of installation further solidify its position as a valuable material in enhancing energy efficiency.
Considering its numerous benefits, Styrofoam remains a compelling choice for those seeking reliable and cost-effective insulation solutions. It contributes to creating more energy-efficient and comfortable environments, whether for residential or commercial projects.
For all your insulation requirements, you can get wholesale Styrofoam directly from us. Contact us today to learn more about our products and how we can support your next project.