In today’s construction and industrial sectors, material selection is critical for performance, efficiency and sustainability. XPS Styrofoam is a material that has received much attention due to its unique properties that make it stand out in many applications. But what exactly is XPS Styrofoam?
What is Xps Styrofoam?
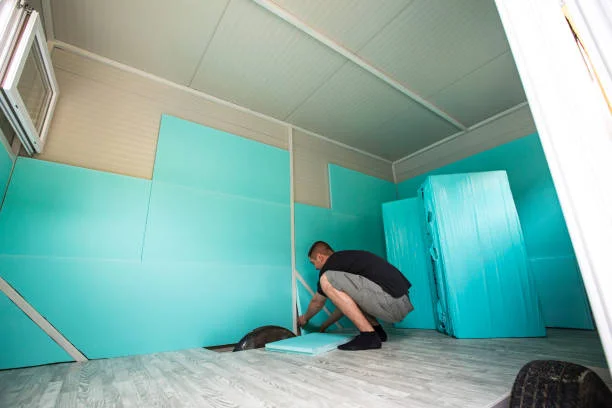
XPS polystyrene foam, full name Extruded Polystyrene Styrofoam, is a rigid foam plastic made from polystyrene resin through an extrusion process. Its main component is polystyrene, and a foaming agent such as carbon dioxide or hydrofluorocarbons is added during the manufacturing process to form a uniform closed-cell structure.
What is the Difference Between Xps Styrofoam and Eps Styrofoam?
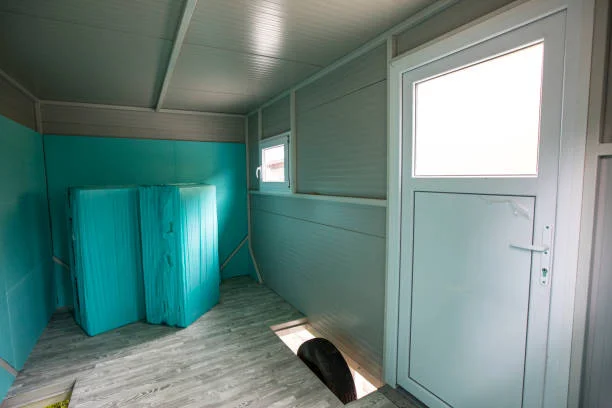
The main differences between XPS Styrofoam and EPS Styrofoam are as follows:
- Production method: XPS is made by adding polystyrene resin components and adding a small amount of additives; EPS is formed by the foam of polystyrene resin.
- Features: Compared with EPS, XPS has low thermal conductivity, high heat resistance, low linearity, and low expansion coefficient.
- Thermal insulation performance: At the same thickness, XPS has better thermal insulation performance than EPS. However, if the same thermal insulation effect is to be achieved, the thickness of XPS sheet can be thinner, but its price is relatively higher.
- Water absorption: EPS is more likely to absorb water than XPS.
- Strength: XPS has higher strength and EPS has lower strength. XPS may be more suitable in coastal areas or buildings that require higher roof strength, but XPS sheets are more brittle, and when the pasting area is large, the exterior wall finishing layer is more likely to crack.
- Flexibility: EPS has better flexibility than XPS.
- Weather resistance: XPS is not as weather resistant as EPS, but EPS’s ductility can overcome certain defects.
- Breathability: EPS has better breathability than XPS.
- Environmental protection: EPS is not environmentally friendly during the production process, and it will emit a lot of waste and gas.
- Maturity: EPS insulation system is more mature at home and abroad, and there are more corresponding technical documents; while XPS insulation system needs further improvement and practice.
Performance Advantages of XPS Polystyrene Foam
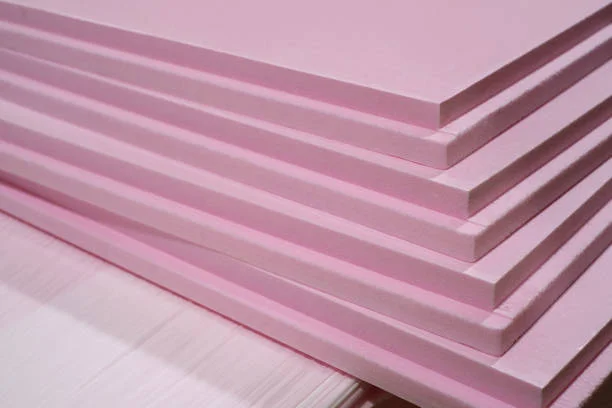
Excellent Thermal Insulation Performance
XPS polystyrene foam has extremely low thermal conductivity, a property that gives it excellent insulation capabilities. Thermal conductivity is a key measure of a material’s effectiveness at preventing the transfer of heat, and XPS foam’s value is significantly lower than that of many traditional insulation materials. Its unique molecular structure and closed-cell cell morphology effectively limit the occurrence of heat convection and heat conduction.
This advantage is particularly significant in building insulation applications. The energy consumption of a building depends largely on its insulation performance, and using XPS for insulation can significantly reduce the exchange of heat between indoors and outdoors. In winter, it can effectively block the intrusion of cold air and keep the room warm, thereby reducing the energy consumption of heating equipment; in summer, it can prevent external heat from entering the room and reduce the burden on the air conditioning system. This not only creates a comfortable indoor environment for residents, but also brings considerable energy savings in long-term use, helping to reduce the building’s operating costs, while also having positive implications for reducing energy consumption and greenhouse gas emissions.
High Strength and Pressure Resistance
XPS polystyrene foam exhibits superior compressive strength compared to other common foam materials. This is mainly due to its uniform and dense closed-pore structure, as well as the unique molecular chain arrangement formed during the production process. This high strength allows XPS to withstand large loads without deformation, performing well in a variety of practical application scenarios.
In terms of ground insulation, it can withstand the daily activities of people and furniture and the placement of heavy objects without significant compression and dents. For roof load-bearing, XPS can serve as an effective insulation layer while providing additional support to the roof structure, enhancing the overall stability of the roof and resisting the pressure caused by natural factors such as wind, rain and snow.
Excellent Moisture-proof Performance
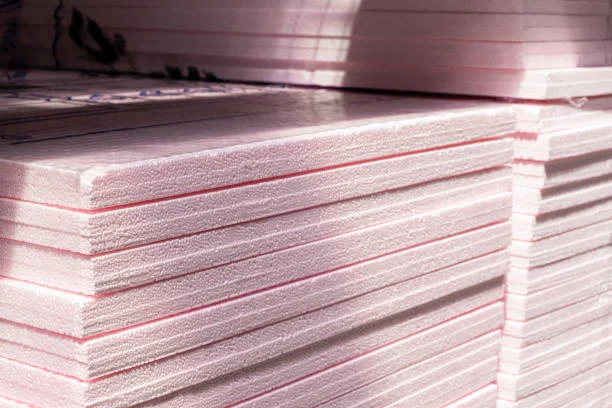
The closed-cell structure of XPS polystyrene foam is key to its excellent moisture resistance. The closed-cell structure makes it difficult for moisture to penetrate into the foam, effectively preventing moisture absorption. This feature is a great advantage in applications with higher humidity or in contact with water.
In buildings, good moisture resistance is essential to maintain insulation. If the insulation material absorbs moisture, its thermal conductivity will increase, resulting in a decrease in insulation performance. XPS foam effectively avoids this problem, maintaining good insulation and structural stability over the long term, even in damp basements or near water sources.
Chemical Stability
XPS polystyrene foam exhibits good resistance to most chemicals. This is due to the chemical structure of polystyrene itself and the stabilizers and antioxidants added during the production process. It is not susceptible to erosion and degradation by common chemicals such as acids, alkalis, salts and organic solvents.
This chemical stability enables XPS to maintain stable performance under a variety of complex environmental conditions. Whether exposed to industrial waste gases, acid rain, or chemical leaks, it maintains its physical and chemical properties. This makes XPS widely used in industries that require high chemical stability of materials, such as chemical industry and electronics.
XPS Manufacturing Process
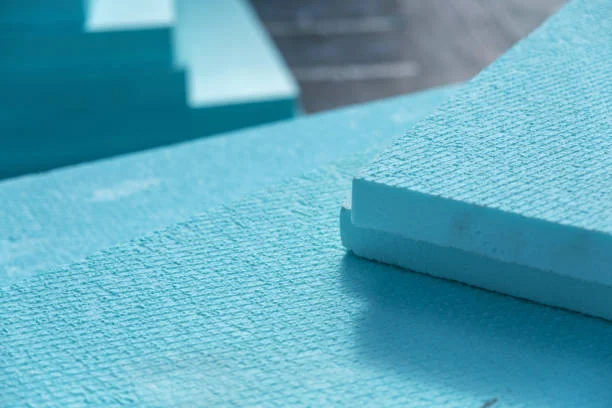
The manufacturing process of XPS includes the following key steps:
Raw Material Preparation
polystyrene resin particles are mixed with additives such as foaming agents, flame retardants, antioxidants, etc. in precise proportions. Ensuring the quality and proportion of the raw materials is accurate is the basis for the subsequent production of high-quality XPS sheets.
Extrusion Molding
The mixed raw materials are fed into the extruder. The inside of the extruder is in a high temperature and high pressure environment, and the raw materials are extruded under strong mechanical pressure and thermal force to form a continuous plate or tube shape.
Foaming and Curing
During the extrusion process, the foaming agent is decomposed by heat to produce gas, causing the material to expand to form a uniform closed-cell foam structure. Subsequently, it is quickly cooled by a cooling device to solidify and shape the foam to maintain a stable shape and size.
Cutting and Trimming
The cured XPS sheet is cut according to the predetermined length and width. At the same time, the edges and surfaces of the sheet are trimmed to ensure dimensional accuracy and appearance quality.
Quality Inspection
The XPS sheets produced are tested for various performance indicators, such as density, compressive strength, thermal conductivity, water absorption, etc., to ensure that the products meet relevant standards and customer requirements.
Packaging and Storage
Qualified XPS sheets are packaged to protect the products from damage during transportation and storage, and are properly stored in a dry and ventilated warehouse waiting for shipment and use.
The fine control and coordinated operation of these key steps ensure the performance and quality of XPS products.
Application Areas of XPS Styrofoam
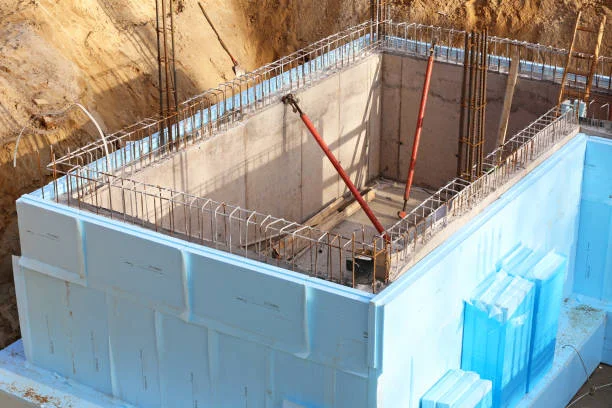
- Building insulation
Widely used in exterior wall insulation, roof insulation, basement insulation, etc., to help buildings achieve energy-saving goals. - Cold chain logistics
Used for insulation of refrigerated trucks, cold storage and other facilities to ensure the temperature stability of goods during transportation and storage. - Packaging materials
Provide buffering and protection for electronic products, medical devices, etc., and have certain insulation functions. - Floor insulation
In floor heating systems, XPS can effectively reduce heat loss downward and improve energy efficiency.
Conclusion
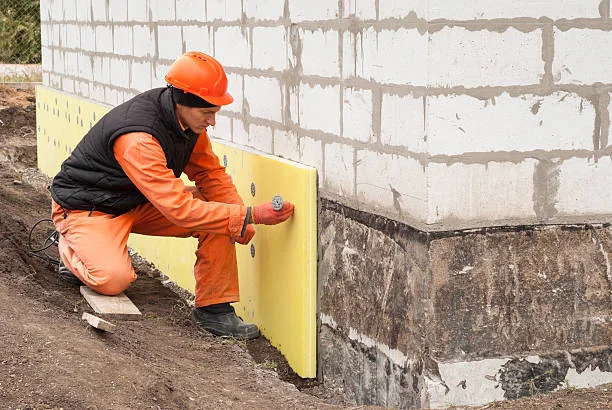
XPS Styrofoam, as a high-performance insulation and building material, plays an important role in many fields. Understanding its definition, performance, manufacturing process, application and sustainability will help us select and use this material more scientifically, and also encourage us to continue to explore innovations to achieve more efficient and environmentally friendly building and industrial solutions.
Visit our website to learn more about Styrofoam.