Expandable Polystyrene (EPS), also widely known by the brand name Styrofoam, is a lightweight and versatile plastic material with a vast array of applications. From protective packaging to building insulation and even decorative elements, EPS finds itself woven into the fabric of our daily lives. But how does this seemingly simple material come to be?
This blog post dives into the intricacies of EPS block molding, the process that lays the foundation for countless EPS products.
EPS Building Block
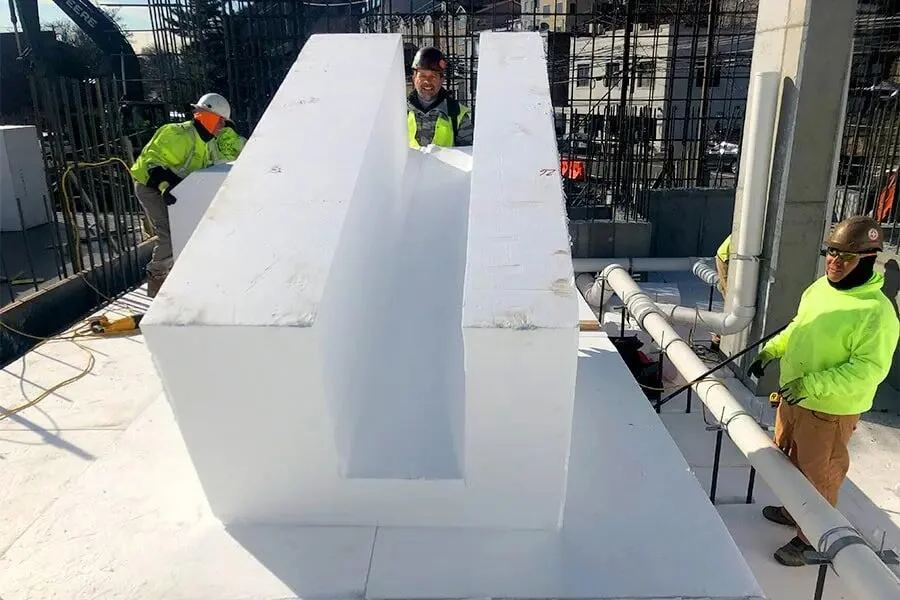
EPS starts its journey as tiny, solid beads of polystyrene resin. These beads are infused with a blowing agent, typically a hydrocarbon gas like pentane. The blowing agent plays a crucial role – when exposed to heat, it expands, causing the solid beads to puff up into the familiar white foam we associate with EPS.
EPS Block Molding Process
While the previous section provided a general overview, let’s delve deeper into the technical aspects of the EPS block molding process, focusing on the key factors influencing quality and efficiency:
Pre-Expansion:
- Pre-Expander Design: The design of the pre-expander significantly impacts the uniformity of bead expansion. Factors like steam distribution channels, mixing chambers, and bead residence time all play a role.
- Steam Pressure and Temperature Control:Â Precise control of steam pressure and temperature within the pre-expander ensures consistent bead expansion and minimizes the risk of over-expansion or bead fusion.
Mold Design and Materials:
- Mold Material: Molds are typically constructed from steel or aluminum due to their durability and ability to withstand high temperatures. In some cases, special coatings might be applied to the mold surface to enhance heat transfer or prevent sticking.
- Venting Channels: Proper venting channels within the mold allow for the escape of trapped air during the molding process, promoting uniform density and minimizing internal voids in the EPS block.
- Cooling System Design: The efficiency of the cooling system significantly impacts cycle times. Water-based systems with efficient circulation patterns offer faster cooling compared to simple air circulation methods.
Process Parameters and Control:
- Steam Flow Control: Precise regulation of steam flow during the molding stage is crucial for achieving the desired final density of the EPS block. Higher steam pressure leads to lower density and vice versa.
- Cooling Rate Control: The cooling rate significantly impacts the final properties of the EPS block. A rapid cooling rate can lead to internal stresses and potential cracking, while an excessively slow cooling rate extends cycle times. Modern machines incorporate sophisticated control systems to optimize the cooling process for specific material formulations and desired block properties.
- Vacuum Technology (if applicable): When vacuum technology is utilized, the timing and level of vacuum applied during the molding stage need to be carefully controlled. Early application of vacuum can prematurely collapse the beads, while delayed vacuum might not effectively remove trapped air.
Quality Control Measures:
- Bead Inspection:Â Regular inspection of the pre-expanded beads ensures consistent size and quality before entering the molding process.
- Dimensional Checks:Â The final EPS blocks undergo dimensional checks to ensure they meet the required specifications.
- Density Testing:Â Density testing methods like gravimetric analysis or core density meters help verify that the EPS block meets the desired density range.
Additional Considerations:
- Material Handling:Â Proper handling and storage of pre-expanded beads are essential to prevent damage or contamination that could affect the final product quality.
- Maintenance: Regular maintenance of the EPS block molding machine, including cleaning the mold cavity and checking for leaks, is crucial to ensure optimal performance and consistent product quality.
By understanding these technical details, manufacturers can optimize their EPS block molding process, achieving consistent quality, improved efficiency, and minimal waste generation.
The Importance of Vacuum Technology (Optional):
While the basic EPS block molding process relies on steam pressure for expansion and cooling, some advanced machines incorporate vacuum technology. Here’s how it adds value:
- Enhanced Density Control: A vacuum applied during the molding stage helps remove air trapped within the beads, leading to a more uniform and consistent density throughout the EPS block.
- Improved Quality and Appearance: By minimizing air pockets, vacuum technology can contribute to a smoother surface finish on the final EPS block.
- Faster Cycle Times: In some cases, vacuum technology can help optimize the cooling process, potentially leading to slightly faster production cycles.
Applications of EPS Blocks:
The large EPS blocks produced through this process serve as the raw material for a wide range of applications. Here are some prominent examples:
- Packaging: EPS blocks are cut into various shapes and sizes to create protective packaging for delicate items, electronics, and appliances.
- Construction: EPS blocks are used to manufacture insulation boards for walls, roofs, and foundations, contributing to energy-efficient buildings.
- Industrial Applications: EPS blocks are used to create lightweight and shock-absorbing components for various industrial applications.
- Craft and Design: EPS blocks can be shaped and sculpted to create decorative elements, architectural models, and artistic installations.
Choosing the Right EPS Block Molding Machine:
For manufacturers venturing into EPS production, selecting the right block molding machine is crucial. Here are some key factors to consider:
- Production Volume:Â The machine’s capacity and production rate should align with your desired output.
- Desired Block Size:Â Ensure the mold cavity dimensions can accommodate the size and shape of EPS blocks you require.
- Level of Automation: Consider the level of automation desired, balancing labor costs with your production needs.
- Budget: EPS block molding machines come in various price ranges. Choose a machine that fits your budget while offering the necessary features for your application.
Safety Considerations in EPS Block Molding:
- Heat Exposure: The EPS block molding process involves high temperatures. Always wear appropriate personal protective equipment (PPE) like heat-resistant gloves and clothing.
- Steam Safety: Be aware of the potential hazards of pressurized steam. Follow proper safety protocols and maintain the machine in accordance with the manufacturer‘s instructions.
- Dust Control: The pre-expansion process generates EPS dust. Ensure proper ventilation and dust collection systems are in place to maintain a healthy work environment.
Conclusion: The Building Blocks of Innovation
The EPS block molding process forms the foundation for a vast array of EPS products that touch our lives in countless ways. From the protective packaging of everyday goods to the energy-efficient insulation of our homes, EPS blocks play a significant role in various industries.
As technology advances, EPS block molding continues to evolve, offering increased efficiency, improved quality control, and a focus on sustainability. Understanding this process allows for a deeper appreciation of the versatile and ever-evolving world of EPS.