EPS (Expanded Polystyrene) machines play a pivotal role in modern manufacturing, offering versatile solutions across diverse industries.
Understanding how EPS machines function is crucial for appreciating their impact on production efficiency and product quality.
What Is EPS Machine?
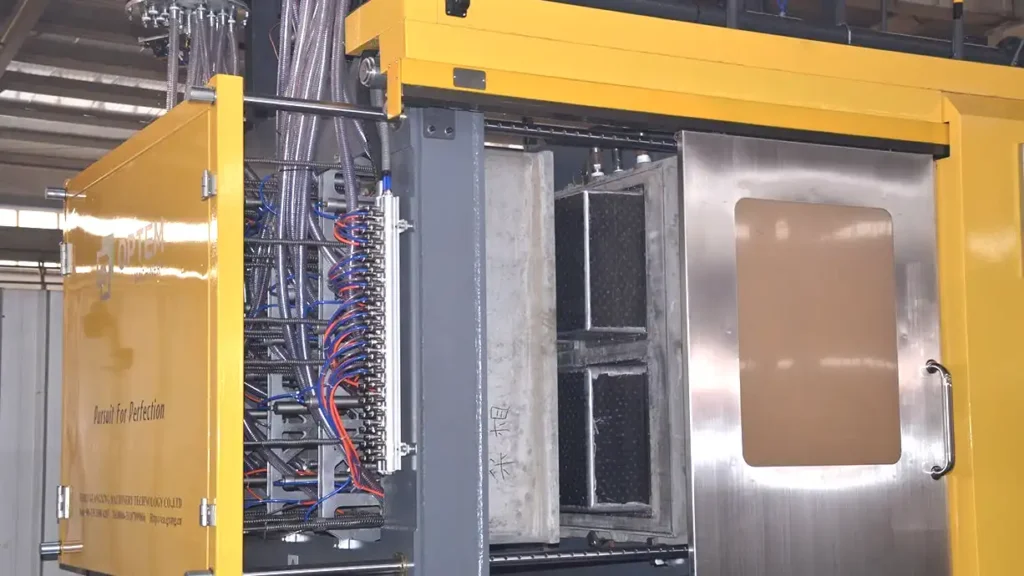
An EPS (Expanded Polystyrene) machine is a specialized piece of equipment used in manufacturing processes to produce expanded polystyrene foam products. These EPS machines utilize advanced technology to transform raw polystyrene beads into lightweight and versatile foam materials.
Importance of EPS Machine
EPS machines play a crucial role in various industries, including packaging, construction, and automotive manufacturing. They enable the creation of a wide range of EPS products, such as packaging materials, insulation panels, and automotive components.
The operation of an EPS machine involves several key steps:
- Pre-expansion: The process begins with pre-expanding polystyrene beads using steam. This step ensures uniform expansion and density control, laying the foundation for high-quality foam products.
- Molding: Pre-expanded beads are then transferred to molds, where they undergo heat and pressure treatment to achieve the desired shape and density. Precision in molding is essential for meeting product specifications and quality standards.
- Cooling and Demolding: After molding, the formed EPS products are cooled to stabilize their structure. Once cooled, the products are demolded and inspected for quality assurance before further processing or packaging.
EPS machines are equipped with advanced control systems to monitor and regulate various parameters such as temperature, pressure, and timing. This ensures consistent product quality and production efficiency.
EPS Machine Working Process
The working process of an EPS (Expanded Polystyrene) machine involves several intricate steps that transform raw polystyrene beads into expanded foam products. Here’s a detailed explanation of how an EPS machine operates:
Step 1: Pre-expansion
The process begins with the pre-expansion of polystyrene beads. These beads are loaded into a chamber within the EPS machine, where they are exposed to steam. The steam causes the beads to expand, increasing their volume and forming tiny closed cells within the material. This pre-expansion step ensures uniform expansion and density control, laying the groundwork for high-quality foam products.
Step 2: Molding
Once the beads are pre-expanded, they are transferred to molds where they undergo molding. The molds are typically made of metal and are designed to give the desired shape and size to the foam products. The pre-expanded beads are injected into the molds, and heat and pressure are applied to further expand and fuse the beads together. This process ensures that the foam products take on the precise shape and density required for their intended application.
Step 3: Cooling and Demolding
After molding, the foam products are cooled to stabilize their structure. Cooling may involve circulating air or water around the molds to accelerate the cooling process. Once cooled, the foam products are demolded from the molds. This is typically done mechanically, using hydraulic or pneumatic systems to eject the products from the molds. The demolding process must be carefully controlled to prevent damage to the foam products.
Step 4: Inspection and Finishing:
After demolding, the foam products undergo inspection to ensure they meet quality standards. Any defects or imperfections are identified and addressed before the products are further processed or packaged. Depending on the application, additional finishing steps such as trimming, cutting, or surface treatment may be carried out to achieve the desired final appearance and properties.
Step 5: Packaging or Further Processing:
Once the foam products have been inspected and finished, they are ready for packaging or further processing. In some cases, the products may undergo additional treatments or assembly processes before being packaged for shipment to customers or assembly lines.
The working process of an EPS machine involves precise control of temperature, pressure, and timing to ensure the production of high-quality foam products. From pre-expansion to molding, cooling, and finishing, each step plays a crucial role in shaping the final characteristics of the foam products, making EPS machines essential tools in modern manufacturing processes.
Applications of EPS Machine
EPS (Expanded Polystyrene) machines are versatile tools used across various industries for producing foam products with unique properties. Here are some common applications of EPS machines:
- Packaging: EPS foam is widely used in packaging due to its lightweight nature and excellent cushioning properties. It is commonly employed for protecting fragile items during shipping and transportation. EPS packaging provides shock absorption and thermal insulation, making it ideal for electronic goods, appliances, glassware, and perishable items.
- Construction: EPS foam is extensively utilized in the construction industry for thermal insulation and building materials. EPS panels are lightweight, easy to handle, and offer superior insulation properties, making them ideal for insulating walls, roofs, and foundations. Additionally, EPS can be molded into various shapes and sizes, providing versatility in construction applications.
- Automotive: In the automotive sector, EPS foam finds applications in interior components, such as seat cushions, headliners, and door panels. Its lightweight nature helps reduce vehicle weight, contributing to fuel efficiency and improved performance. Additionally, EPS foam provides sound insulation and vibration damping properties, enhancing passenger comfort.
- Marine: EPS foam is used in marine applications for buoyancy and flotation devices. Its closed-cell structure makes it resistant to water absorption, ensuring buoyancy and stability in marine environments. EPS buoyancy aids in the construction of docks, pontoons, and marine buoys, as well as in the fabrication of flotation devices for boats and watercraft.
- Arts and Crafts: EPS foam is a popular material in arts and crafts due to its lightweight, easy-to-carve nature. Artists and hobbyists use EPS foam blocks and sheets to create sculptures, props, and decorations for theatrical productions, exhibitions, and events. EPS foam can be easily shaped, carved, and painted to achieve desired artistic effects.
- Horticulture: EPS foam is utilized in horticulture for its insulating properties and water retention capabilities. EPS foam can be used as a protective cover for plants during cold weather, providing insulation against frost and maintaining soil temperature. Additionally, EPS foam can be incorporated into hydroponic and aquaponic systems to support plant growth and nutrient absorption.
- Medical: In the medical field, EPS foam is used in orthopedic devices, prosthetics, and medical packaging. Its lightweight and shock-absorbing properties make it suitable for applications such as splints, braces, and cushioning materials. EPS foam packaging is also used to protect delicate medical equipment and supplies during shipping and storage.
These are just a few examples of the diverse applications of EPS machines in various industries. The versatility, cost-effectiveness, and performance characteristics of EPS foam make it a preferred choice for a wide range of applications, from protective packaging to structural insulation and beyond.
Advantages of EPS Machine
EPS (Expanded Polystyrene) machines offer numerous benefits in manufacturing processes, making them valuable assets in various industries.
Here are some advantages of EPS machines:
- Lightweight: EPS foam products are exceptionally lightweight, making them easy to handle and transport. This lightweight nature reduces shipping costs and simplifies logistics, especially for large and bulky items.
- Insulation Properties: EPS foam exhibits excellent thermal insulation properties, helping to regulate temperature and conserve energy in buildings, vehicles, and appliances. Its insulation capabilities contribute to energy efficiency and cost savings over the long term.
- Versatility: EPS machines can produce foam products in a wide range of shapes, sizes, and densities to suit diverse applications. From packaging materials to construction components, EPS foam offers versatility in design and functionality.
- Cost-effectiveness: The manufacturing process of EPS foam products is cost-effective compared to alternative materials. EPS machines optimize material usage and production efficiency, resulting in lower production costs and competitive pricing for end products.
- Durability: Despite its lightweight nature, EPS foam is durable and resilient, capable of withstanding impact and compression forces. This durability ensures that EPS foam products maintain their integrity and performance under various conditions.
- Customization: EPS machines allow for customization of foam products to meet specific customer requirements and design preferences. Manufacturers can adjust parameters such as density, shape, and surface finish to achieve desired product characteristics.
- Recyclability: EPS foam is recyclable and can be processed into new foam products or other materials through recycling programs. This recyclability reduces waste and promotes environmental sustainability, aligning with circular economy principles.
- Sound Absorption: EPS foam has sound-absorbing properties, making it suitable for acoustic insulation applications. It helps reduce noise transmission and improve acoustic comfort in buildings, vehicles, and industrial environments.
- Chemical Resistance: EPS foam is resistant to chemicals and moisture, ensuring long-term durability and stability in various environmental conditions. This resistance makes EPS foam suitable for outdoor and harsh environment applications.
- Design Freedom: EPS machines enable intricate designs and complex shapes to be produced with precision and consistency. This design freedom allows for creative and innovative solutions in product development and manufacturing.
These advantages highlight the value of EPS machines in modern manufacturing processes, offering efficiency, versatility, and performance across diverse industries.
Conclusion
EPS machines play a vital role in modern manufacturing, offering versatile solutions across various industries. From packaging to construction and automotive applications, EPS foam continues to revolutionize product design and performance. Embracing sustainable practices and technological innovations will drive the future growth of EPS technology, ensuring a greener and more efficient manufacturing ecosystem.
FAQs
What is EPS foam made of?
EPS foam is made of expanded polystyrene, a lightweight and rigid plastic material derived from petroleum.
Are EPS products recyclable?
Yes, EPS products are recyclable. Recycling programs and initiatives aim to reduce EPS waste and promote environmental sustainability.
How does EPS insulation work?
EPS insulation works by trapping air within its cellular structure, creating a barrier that prevents heat transfer. This thermal insulation property helps maintain desired temperatures in buildings and vehicles.
Can EPS foam be used in food packaging?
Yes, EPS foam is commonly used in food packaging due to its lightweight, insulating, and shock-absorbing properties. It helps protect perishable goods during transportation and storage.
What are the alternatives to EPS foam?
Alternatives to EPS foam include biodegradable packaging materials, such as paper-based products, mushroom packaging, and bioplastics. These materials offer sustainable solutions for packaging and insulation needs.
How long does EPS foam take to decompose?
EPS foam is non-biodegradable and can take hundreds of years to decompose in landfills. However, recycling initiatives and innovative technologies aim to reduce EPS waste and minimize its environmental impact.