Styrofoam is a ubiquitous material, found in everything from coffee cups to packaging. But have you ever stopped to wonder what exactly it’s made of? This blog post delves into the composition of this versatile material, exploring its chemical makeup and manufacturing process.
We’ll break down the science behind Styrofoam, explaining how polystyrene beads are transformed into the lightweight, insulating product we know. Join us as we uncover the secrets of Styrofoam and shed light on its properties and applications.
What Is Styrofoam
Styrofoam is a type of plastic foam that’s formally known as expanded polystyrene (EPS). It’s made from tiny beads of polystyrene, a type of plastic, that are expanded and molded together. This process creates a lightweight material that’s mostly air, which is why it’s so good at insulation.
While the word “Styrofoam” is often used to refer to any type of foam cup or packaging, it’s actually a trademarked name for a specific type of extruded polystyrene (XPS) foam made by DuPont. This type of foam is denser and more moisture-resistant than EPS, and is typically used for construction purposes like insulation.
Styrofoam Chemical Formula
Styrofoam is actually a brand name for a type of extruded polystyrene foam (XPS), but the chemical formula for the base material, polystyrene, is (C8H8)n.
Here’s what that means:
- C8H8: This represents the repeating unit of the polystyrene molecule. It shows that the molecule is made up of 8 carbon atoms (C) and 8 hydrogen atoms (H).
- n: This indicates that the C8H8 unit is repeated many times, forming a long chain or polymer. The “n” can be a very large number, resulting in a large molecule.
Essentially, polystyrene is a long chain of repeating styrene units. This structure gives it its unique properties, such as its lightweight nature, insulation capabilities, and moldability.
When Was Styrofoam Invented
Styrofoam, as we know it, was invented in 1941 by Ray McIntire, a chemical engineer working at Dow Chemical. He was actually trying to create a flexible insulator to replace rubber, which was in short supply during World War II.
In his experiments, McIntire combined styrene with isobutylene, and accidentally discovered that the isobutylene formed tiny bubbles within the styrene, creating a foam that was 30 times lighter and more flexible than solid polystyrene. This accidental discovery led to the creation of Styrofoam, a material that has since become ubiquitous in packaging, insulation, and many other applications.
What is Styrofoam Made of
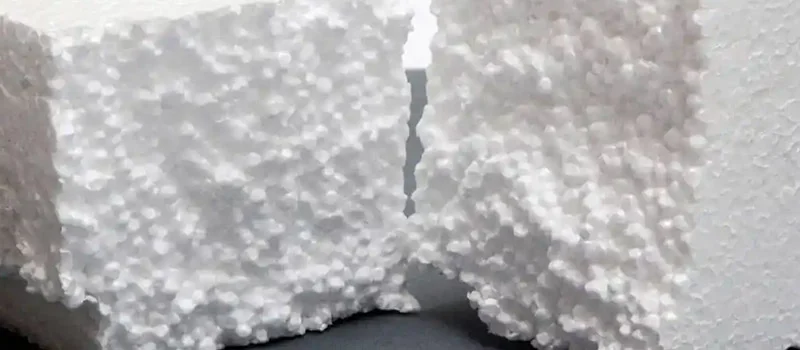
Here’s the chemical equation for the reaction:
C8H10 (ethylbenzene) -> C8H8 (styrene) + H2 (hydrogen gas)
Styrofoam, or expanded polystyrene (EPS), is primarily made from the elements carbon and hydrogen. These elements are present in the form of polystyrene, which is a polymer derived from petroleum.
Other elements may also be present in EPS depending on any additives used in the manufacturing process, such as flame retardants or stabilizers. However, the main components of EPS are carbon and hydrogen.
Styrofoam Composition
Styrofoam, or expanded polystyrene (EPS), is primarily composed of polystyrene, a type of plastic derived from petroleum. This base material is formed into tiny beads, which are then expanded using a blowing agent, like pentane. The expansion process creates a lightweight material that is mostly air (around 98%), giving Styrofoam its characteristic properties of being lightweight and insulating.
What Does Styrofoam Look Like
Styrofoam, in its most common form, appears as a lightweight, white, and slightly rigid foam. It’s often composed of small, tightly packed beads that are fused together, giving it a slightly textured, almost pebbled surface. Depending on how it’s manufactured, it can also have a smoother, more uniform appearance. The material is generally quite brittle and can break or crumble easily, especially when compressed or impacted.
Beyond the classic white, Styrofoam can sometimes be colored, though this is less common for standard packaging or insulation applications. You might encounter colored Styrofoam in craft projects or specialized packaging where color-coding or aesthetics are desired. The color is usually added during the manufacturing process.
It’s important to note that “Styrofoam” is often used generically to refer to any type of expanded polystyrene foam. However, the actual trademarked Styrofoam, made by Dow Chemical, is a specific type of extruded polystyrene (XPS) foam. This XPS foam is denser, has a smoother surface, and is often blue in color. It’s typically used for construction and insulation purposes, and has a higher resistance to moisture than the more common expanded polystyrene (EPS) foam.
How Styrofoam is produced
Preparation of Raw Materials:
The primary raw material for Styrofoam production is polystyrene resin, which is derived from petroleum. Other additives such as blowing agents, flame retardants, and stabilizers may also be included depending on the desired properties of the final product.
Pre-Expanding:
The polystyrene resin beads are first pre-expanded using steam. This process involves heating the beads in a steam-filled chamber, causing them to expand and partially fuse together. Pre-expansion increases the volume of the beads and makes them easier to mold in the next step. For environmental protection, The gas commonly added to EPS (expanded polystyrene) during the pre-foaming process is typically pentane.
Pentane is a hydrocarbon gas that serves as a blowing agent, meaning it generates the gas bubbles necessary for expanding the polystyrene beads. During the expansion process, the pentane gas expands rapidly due to the heat, creating the characteristic cellular structure of EPS foam. Once the foam has solidified, the pentane gas is trapped within the foam cells, contributing to its lightweight and insulating properties.
Molding:
The pre-expanded beads are then molded into the desired shape using molds or forms. This can be done using either steam molding or pressure molding techniques. Steam molding involves placing the beads into a mold and exposing them to steam, which causes further expansion and fusion, while pressure molding uses heat and pressure to achieve the same effect.
Final Expansion:
After molding, the formed EPS products undergo a final expansion process to achieve the desired density and shape. This is typically done in a steam chest or oven, where the molded products are exposed to heat and steam, causing them to expand further and fully fuse together.
Cooling and Cutting:
Once the final expansion is complete, the EPS products are allowed to cool and solidify. They are then cut to the required size and shape using hot wires or other cutting tools.
Finishing and Packaging:
After cutting, the EPS products may undergo additional finishing processes such as trimming or shaping to achieve the desired dimensions and appearance. Finally, the finished products are packaged and prepared for distribution and use in various applications such as packaging, insulation, and construction.
Throughout the production process, quality control measures are implemented to ensure that the EPS foam products meet the required specifications and standards for their intended use.
What Natural Resources Are Used to Make Styrofoam
Styrofoam, at its core, is a petroleum-based product. This means that the primary natural resource used in its production is crude oil.
The process begins with extracting crude oil from the earth. This oil is then refined and transformed into various petrochemicals, one of which is styrene. Styrene is a key building block in the creation of polystyrene, the base material for Styrofoam.
While petroleum is the main ingredient, other resources are also involved in the manufacturing process. These include natural gas, which is used to produce ethylene, another component of styrene. Additionally, small amounts of other materials like pentane, a hydrocarbon gas, are used as blowing agents to expand the polystyrene beads.
What Are the Standards for Producing Styrofoam
Standard | Description |
---|---|
ASTM Standards | Developed by the American Society for Testing and Materials (ASTM) covering material properties, performance testing methods, and manufacturing processes. |
ISO Standards | Published by the International Organization for Standardization (ISO) addressing quality management, environmental impact, and product specifications. |
Food Contact Regulations | Regulations set by government agencies such as the U.S. Food and Drug Administration (FDA) and the European Food Safety Authority (EFSA) to ensure the safety of Styrofoam products intended for food contact. |
Building Codes | Local building codes and regulations specify requirements for insulation materials, fire resistance, and structural performance in construction and building applications. |
Environmental Regulations | Regulations related to environmental impact, including restrictions on certain additives, requirements for recycling or disposal, and guidelines for reducing environmental footprint. |
Industry Guidelines | Guidelines and best practices published by industry associations and organizations for the use of Styrofoam in specific applications, such as packaging, insulation, or manufacturing. |
Why Choose Styrofoam
Styrofoam, or expanded polystyrene (EPS), continues to be used in various applications despite its environmental drawbacks due to a combination of key advantages:
Superior Insulation Properties
Styrofoam boasts exceptional insulation capabilities, making it an ideal choice for construction, packaging, and various other applications. Its closed-cell structure effectively traps air, providing excellent thermal resistance and energy efficiency.
Styrofoam insulation helps maintain consistent temperatures, whether you’re aiming to keep your home cozy during winter or cool during scorching summers.
Lightweight and Durable
One of the standout features of Styrofoam is its lightweight nature coupled with remarkable durability. Despite being lightweight, it exhibits impressive strength and resilience, making it suitable for packaging fragile items or constructing sturdy structures.
Whether you’re shipping delicate electronic gadgets or constructing architectural models, Styrofoam’s lightweight yet robust characteristics ensure your products remain well-protected throughout handling and transit.
Versatility Across Industries
From construction to crafting, Styrofoam finds applications across a wide spectrum of industries. Its versatility enables it to be molded into various shapes and sizes, catering to specific project requirements.
In construction, Styrofoam serves as an effective insulation material, reducing heat transfer and enhancing energy efficiency in buildings. Additionally, it finds use in crafting props, sculptures, and even flotation devices, showcasing its adaptability across different domains.
Cost-Effectiveness
In comparison to alternative materials, Styrofoam stands out for its cost-effectiveness. Its affordability makes it an attractive option for businesses and individuals alike, allowing them to achieve their objectives without breaking the bank.
Whether you’re a small business owner looking to optimize packaging costs or a homeowner seeking budget-friendly insulation solutions, Styrofoam offers a compelling value proposition without compromising on quality or performance.
Environmental Sustainability
Contrary to popular misconceptions, Styrofoam can be recycled and repurposed, contributing to environmental sustainability efforts. Many recycling facilities accept Styrofoam for processing, where it can be transformed into new products or utilized as a raw material in various industries.
Styrofoam Commonly Used Additives
In addition to styrene and blowing agents, Styrofoam incorporates various additives to tailor its properties for specific applications. These additives may include flame retardants, colorants, and stabilizers. Flame retardants play a crucial role in enhancing the fire resistance of Styrofoam, making it suitable for applications where safety is paramount. Colorants impart aesthetic appeal, while stabilizers ensure the material’s durability and longevity.
Additive | Function | Specific Product Applications |
Blowing Agents | Blowing agents are added to EPS during the manufacturing process to create the characteristic cellular structure of the foam. Common blowing agents include pentane and carbon dioxide. | 1. Packaging materials for fragile items 2. Insulation for buildings and refrigeration systems 3. Cushioning in furniture and automotive industries |
Flame Retardants | Flame retardants are incorporated into EPS to improve its fire resistance and reduce its flammability. Examples of flame retardants used in EPS include brominated compounds and phosphorus-based additives. | 1. Building insulation and construction materials 2. Electrical and electronic equipment 3. Automotive parts and components |
Stabilizers | Stabilizers are added to EPS to improve its thermal stability and resistance to degradation from heat and ultraviolet (UV) radiation. These additives help prolong the lifespan of EPS products. Common stabilizers include antioxidants and UV absorbers. | 1. Roofing materials and membranes 2. Geotechnical applications such as retaining walls 3. Marine flotation devices and buoyancy aids |
Colorants | Colorants are added to EPS to provide pigmentation and enhance the appearance of the foam. These additives allow EPS products to be manufactured in various colors according to customer preferences or industry standards. | 1. Decorative and ornamental products 2. Packaging for retail products 3. Craft and hobby materials |
Expanders | Expanders are used to control the expansion process of EPS during manufacturing, ensuring uniform cell structure and density. These additives help optimize the physical properties of EPS foam. | 1. Molded packaging inserts for delicate items 2. Structural insulated panels (SIPs) for construction 3. Lightweight fill material in road and landscape projects |
What Are the Applications of Styrofoam?
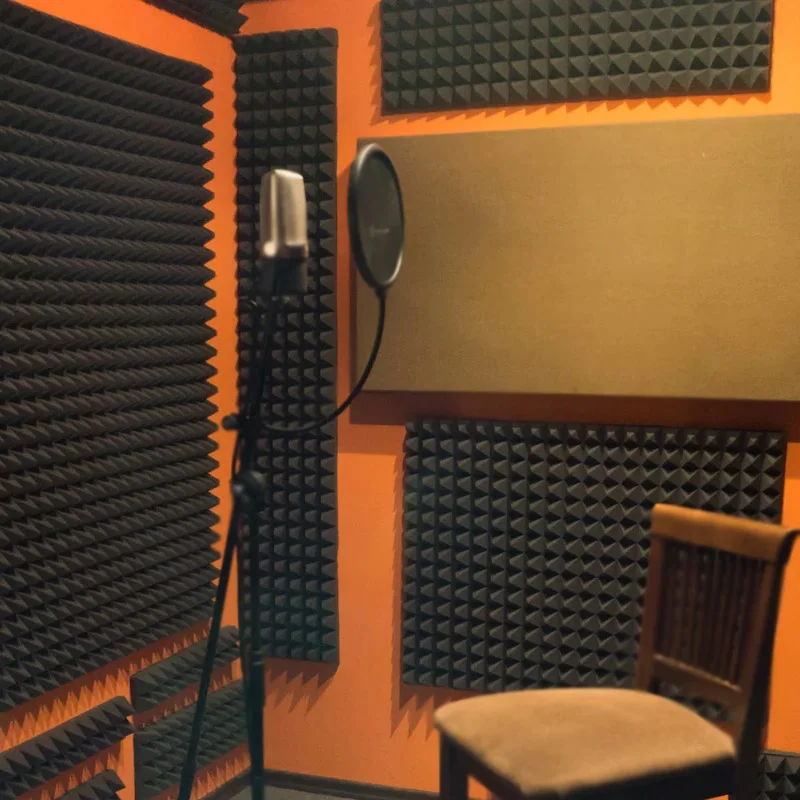
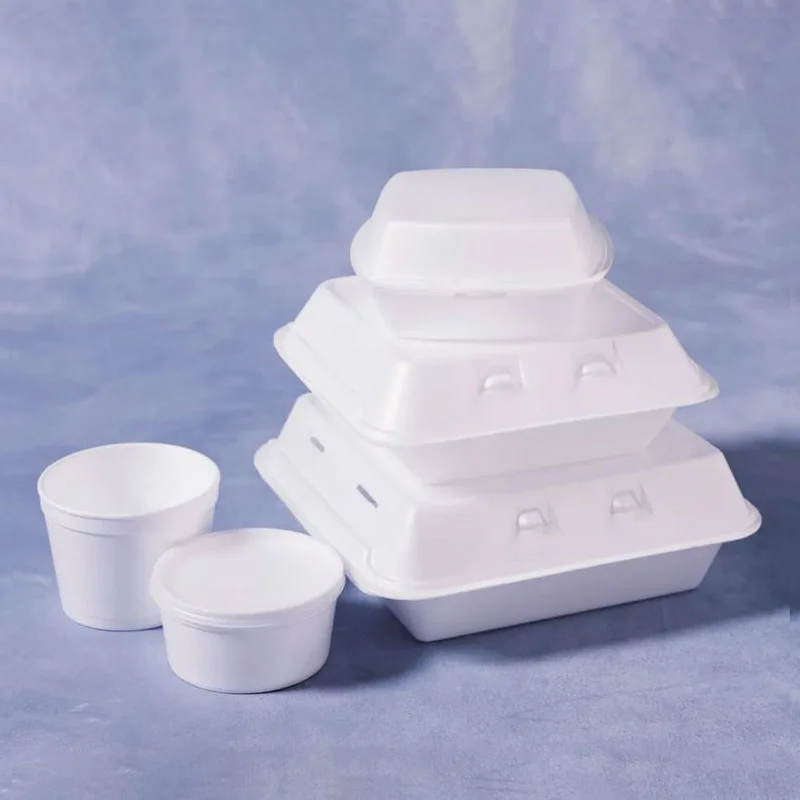
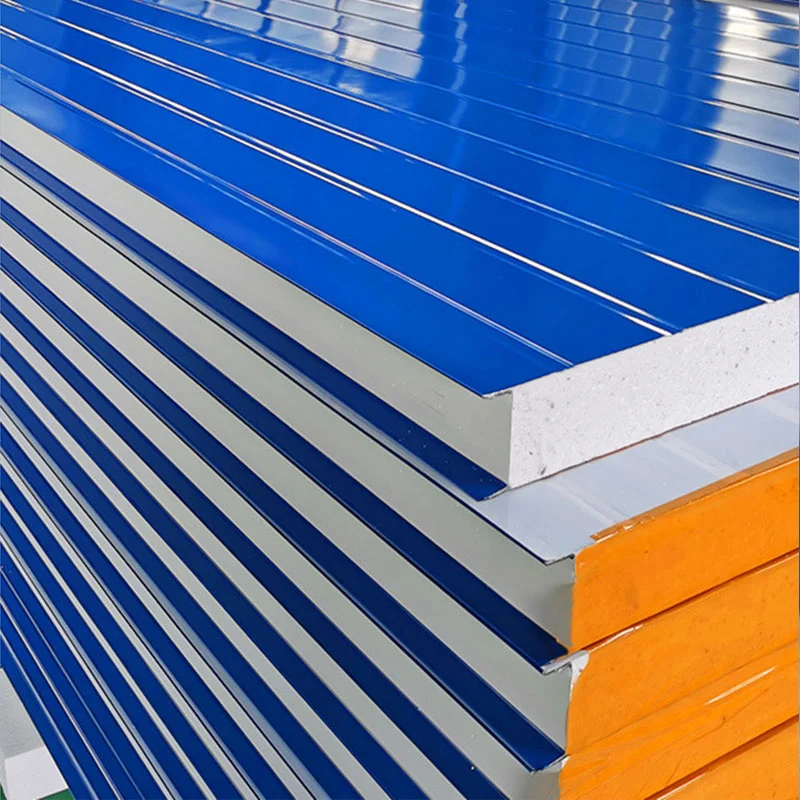
Styrofoam, or expanded polystyrene (EPS), finds widespread use across various industries due to its unique properties. Here’s a breakdown of some of its key applications:
1. Building and Construction:
- Insulation: Styrofoam is a highly effective thermal insulator.
- Wall Insulation: Used in exterior insulation and finish systems (EIFS), cavity wall insulation, and insulated concrete forms (ICFs) to improve energy efficiency in buildings.
- Roof Insulation: Provides excellent thermal resistance for roofs, reducing heat loss and gain.
- Floor Insulation: Used in underfloor heating systems to improve efficiency and reduce heat loss.
- Foundation Insulation: Helps prevent frost heave and improve the stability of foundations.
- Structural Applications: Used in lightweight concrete applications and as a void filler in construction.
2. Packaging:
- Protective Packaging:
- Protects fragile items like electronics, glassware, and appliances during shipping and handling.
- Acts as shock absorbers and cushions, minimizing damage.
- Food Packaging:
- Keeps food and beverages hot or cold during transport.
- Used in disposable food containers, coolers, and ice chests.
3. Marine Applications:
- Buoyancy Aids: Used in life jackets, flotation devices, and marine buoys.
- Pontoon Construction: Used in the construction of docks, piers, and floating platforms.
4. Other Applications:
- Arts and Crafts: Used as a versatile material for sculpting, modeling, and creating various crafts.
- Toys and Games: Used in the production of toys, games, and sports equipment.
- Medical Applications: Used in some medical devices and packaging for medical equipment.
Table Summarizing Styrofoam Applications:
Application Area | Specific Uses |
---|---|
Building & Construction | Insulation (walls, roofs, floors), Foundation insulation, Structural applications |
Packaging | Protective packaging, Food packaging |
Marine | Buoyancy aids, Pontoon construction |
Others | Arts & Crafts, Toys & Games, Medical Applications |
Conclusion
In conclusion, Styrofoam, made primarily of carbon and hydrogen elements derived from polystyrene, undergoes a production process involving styrene monomer synthesis, polymerization, expansion with blowing agents, molding, and finishing. Additives like flame retardants and stabilizers enhance its properties for diverse applications. Quality control ensures compliance with standards from ASTM, ISO, and regulatory bodies.
Despite its versatility, Styrofoam’s non-biodegradability poses environmental challenges, prompting efforts for recycling and eco-friendly manufacturing.
FAQ
What is Styrofoam made of?
Styrofoam is made primarily from expanded polystyrene (EPS), which is a lightweight, rigid plastic foam composed of small beads of polystyrene that have been expanded and fused together.
Are there any other materials used in Styrofoam production?
While expanded polystyrene (EPS) is the main component, Styrofoam may also contain additives such as blowing agents, flame retardants, stabilizers, and colorants, depending on the specific application and manufacturing process.
Is Styrofoam environmentally friendly?
Styrofoam is not biodegradable and can persist in the environment for a long time if not properly disposed of. However, efforts are being made to recycle Styrofoam and reduce its environmental impact.
What are the properties of Styrofoam?
Styrofoam exhibits properties such as lightweight, thermal insulation, shock absorption, buoyancy, and moisture resistance. These properties make it suitable for a wide range of applications in packaging, construction, and other industries.
Can Styrofoam be recycled?
Yes, Styrofoam can be recycled, but the process can vary depending on local recycling facilities and regulations. Some facilities accept clean, dry Styrofoam for recycling, while others may not. It’s important to check with local authorities or recycling centers for guidance on proper disposal and recycling of Styrofoam products.
Is Polystyrene Styrofoam?
While both are related, Styrofoam is not exactly the same as polystyrene. Polystyrene is the base plastic material, while Styrofoam is a specific type of expanded polystyrene foam. Think of it this way: polystyrene is like the flour, and Styrofoam is like a specific type of bread made from that flour.
Styrofoam is created by expanding polystyrene beads, which makes it lightweight and gives it its insulating properties. So, while Styrofoam is made of polystyrene, it’s a distinct form of the material with unique characteristics.