What Is Expanded Polystyrene?
EPS is a lightweight, rigid, and insulating plastic foam material, abbreviated as Expandable (E) Polystyrene (PS).
It possesses excellent and durable thermal insulation, unique cushioning and shock resistance, anti-aging properties, and waterproof characteristics. EPS is widely used in food and electronics packaging, as well as in the construction insulation industry.f the styrene monomer to form the polymer structure of EPS.
What Is Expanded Polystyrene in Construction
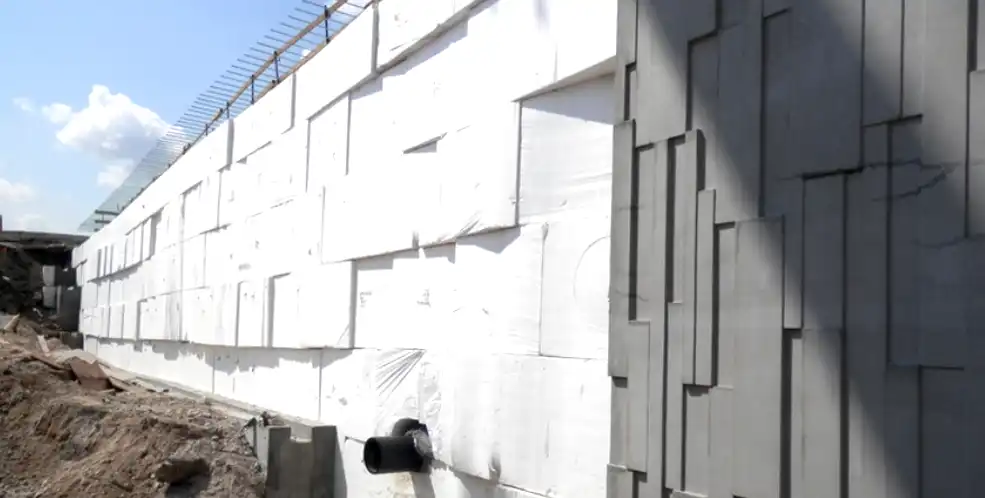
Expanded Polystyrene (EPS) in construction refers to the use of EPS foam as a building material for various applications.
EPS is a lightweight, rigid, cellular plastic material that is popularly used in construction due to its insulation properties, versatility, and cost-effectiveness.
In construction, EPS foam is commonly used in the following forms:
- Insulation: EPS foam boards are widely used as insulation materials in walls, roofs, and floors. The cellular structure of EPS traps air, providing excellent thermal insulation properties that help to regulate indoor temperatures and reduce energy consumption for heating and cooling.
- Lightweight Fill: EPS beads or blocks are used as lightweight fill material in construction applications such as road embankments, foundation backfill, and landscaping. Its lightweight nature reduces structural loads and minimizes settlement issues.
- Concrete Formwork: EPS foam panels are used as temporary formwork for pouring concrete in construction projects. These panels are lightweight, easy to handle, and provide thermal insulation to the concrete during curing.
- Structural Components: EPS can be molded into various shapes and forms to create structural components such as insulated concrete forms (ICFs), which are used for building walls and foundations. ICFs combine the structural strength of concrete with the insulation properties of EPS foam, resulting in energy-efficient and durable building systems.
So, expanded polystyrene plays a significant role in modern construction by offering insulation, lightweight fill, formwork, and structural solutions that contribute to energy efficiency, cost savings, and sustainable building practices.
History of EPS
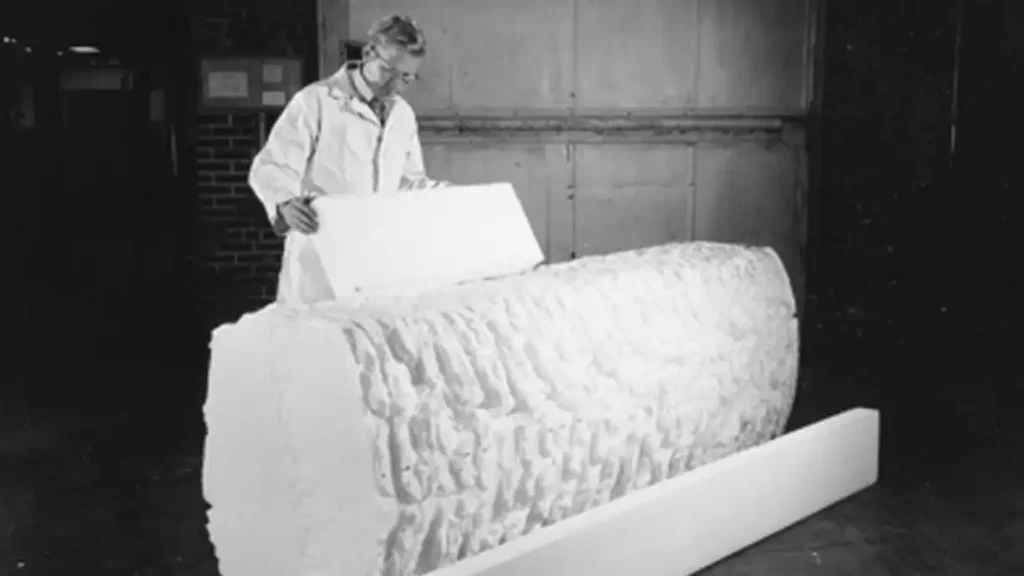
Here are some milestones of EPS history you can get to know in the following.
In 1925, Germany began producing styrene, initially as a rubber intermediate, laying the foundation for the production of polystyrene.
In 1930, suspension PS (polystyrene) was introduced.
In 1943, the US company DOW Chemical became the first to industrialize PS foam plastic production.
In 1949, Japan successfully developed extruded polystyrene foam plastic (XPS) and utilized it for product packaging.
In 1952, EPS (expanded polystyrene) products made their debut at a plastics trade fair in Germany.
EPS Chemical Structure
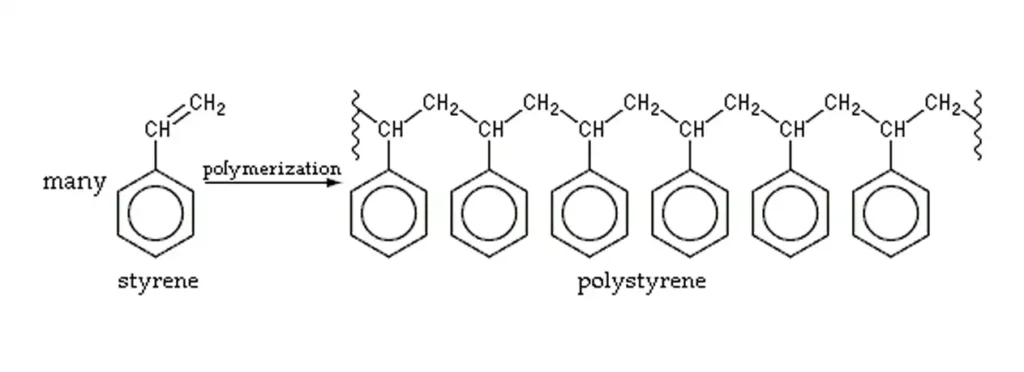
The Expanded Polystyrene Chemical Formula can be represented based on the monomer unit of styrene, which is polymerized to form the polymer. The basic chemical formula for styrene is C8H8, and when polymerized to create polystyrene, the chemical formula can be expressed as (C8H8)n, where ‘n’ represents the number of repeating units in the polymer chain.
So, the generalized chemical formula for expanded polystyrene (EPS) can be represented as (C8H8)n, where ‘n’ is a variable indicating the polymerization.
Expanded Polystyrene Material Properties
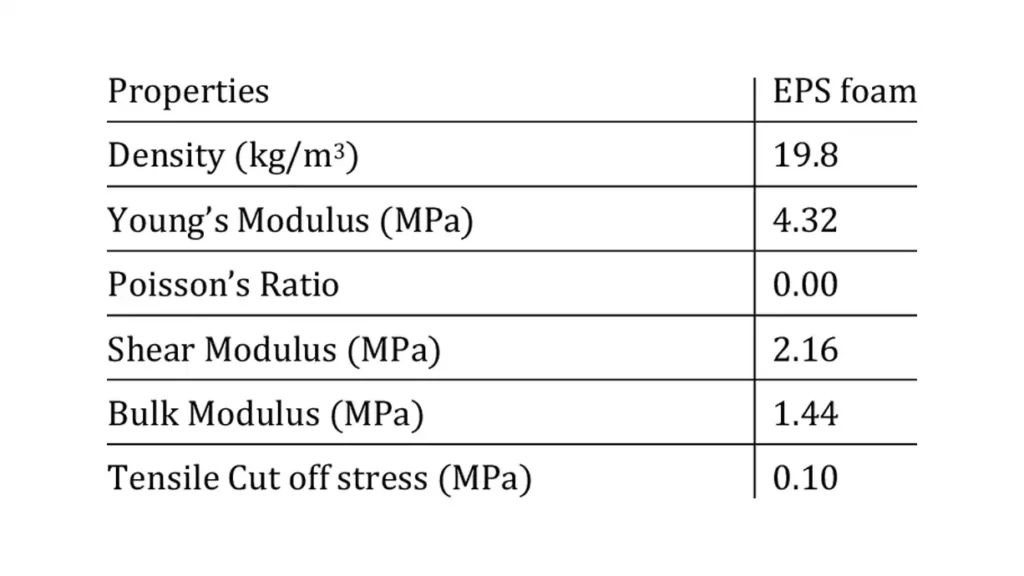
Expanded Polystyrene (EPS) is a versatile and lightweight foam material with several key properties:
Insulation: EPS is known for its excellent thermal insulation properties. It has a low thermal conductivity, making it effective in resisting heat flow and maintaining temperature stability.
Lightweight: EPS is a lightweight material, making it easy to handle and transport. This property is advantageous in various applications, including packaging and construction.
Rigidity: Despite its lightweight nature, EPS exhibits a degree of rigidity, providing structural support in applications like insulation boards and packaging materials.
Buoyancy: EPS is buoyant and water-resistant, making it suitable for applications where buoyancy is important, such as in flotation devices and marine construction.
Chemical Resistance: EPS is resistant to most chemicals, ensuring its stability and performance in various environments.
Cushioning: EPS is commonly used as a cushioning material due to its ability to absorb and disperse impact energy, making it ideal for packaging fragile items.
Moldability: EPS can be molded into various shapes and sizes, offering flexibility in design and customization for specific applications.
Cost-Effective: EPS is a cost-effective material, making it a popular choice for packaging, construction, and insulation solutions.
Recyclability: EPS can be recycled, contributing to sustainability efforts. However, proper recycling facilities and processes are necessary for effective recycling.
Fire Retardant: While EPS is flammable, flame retardants can be added during manufacturing to enhance its fire resistance, making it suitable for certain applications where fire safety is a concern.
You need to know about expanded polystyrene foam properties when you choose the right EPS for specific applications.
Expanded Polystyrene Moulding Process
This is how is expanded polystyrene made.
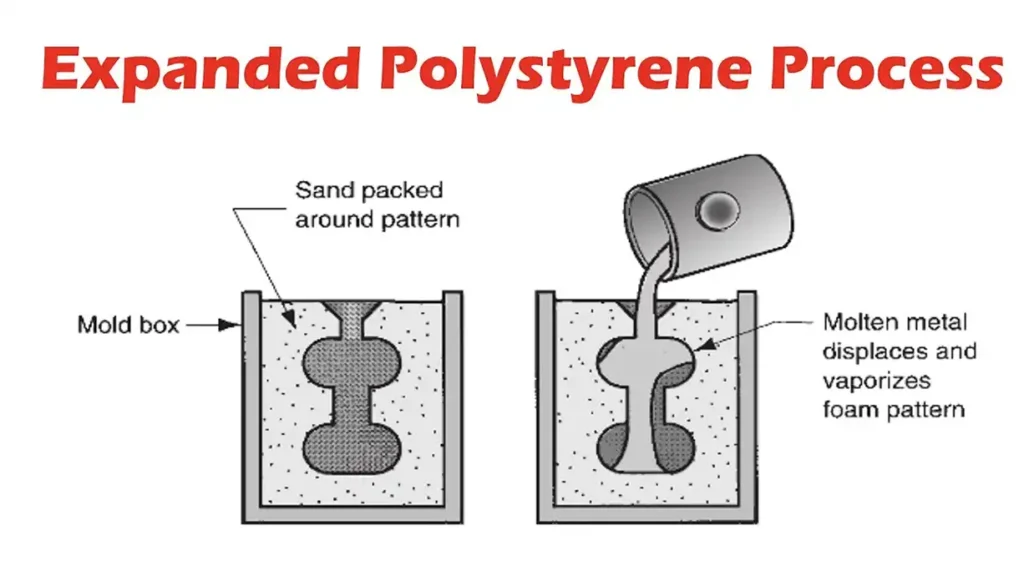
The production process for products made from Expanded Polystyrene (EPS) consists of three main stages:
Step 1: Pre-Expansion:
Expanded polystyrene beads are introduced into a performer.
Steam, along with a small amount of pentane (typically around 5% by weight), serves as a blowing agent, causing the beads to expand approximately 40 times their original size.
The expanded beads are then transferred to a storage hopper for further processing.
Step 2: Maturing /Aging:
The material cools, causing pentane to liquefy and create a partial vacuum within the beads.
The expanded polystyrene beads are stored for 12-24 hours to facilitate maturing and allow air to permeate the beads.
Step 3: Final Forming:
The beads undergo reheating using steam, and a pre-measured quantity of expanded beads is introduced into a mold.
Steam is circulated within the mold, further expanding the polystyrene beads by an additional 10%.
The steaming process halts, and a vacuum is applied to remove residual condensed water and heat. Additional water channels assist in cooling the mold.
Expanded Polystyrene Applications
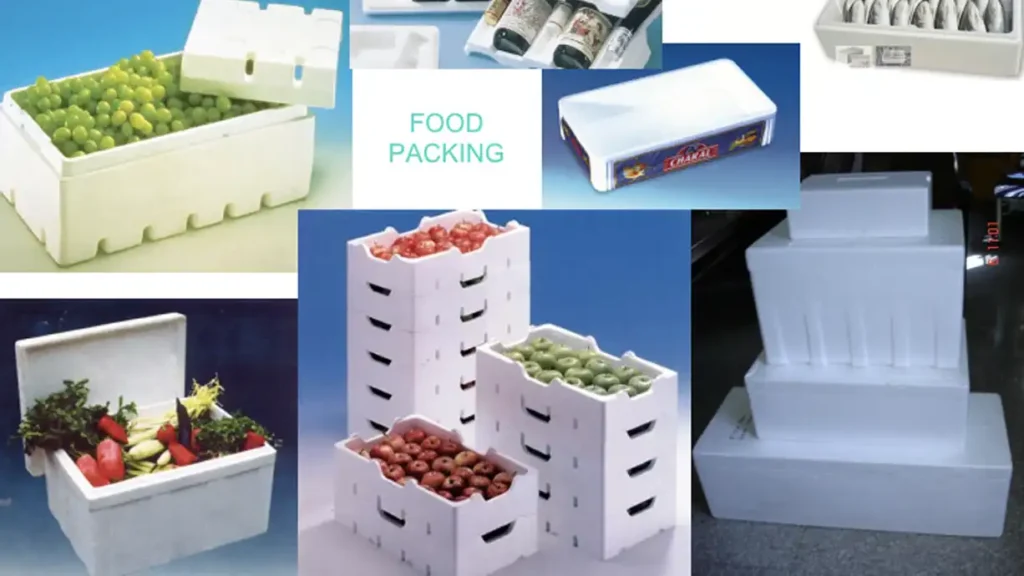
Due to EPS insulation, heat resistance, shock absorption, flexibility, and durability, Expanded polystyrene has a very wide application, and mainly includes packaging and building materials,
Packaging:
Food packaging, includes vegetable boxes, fruit boxes, fish boxes, etc.
Electric appliance packaging, includes TV packaging, refrigerator packaging, air conditional packaging, computer, etc. The EPS raw material is moulded into different shapes as the sandwich layer to protect the appliance inside.
Building:
And EPS material can be designed to be used in building materials, to achieve various applications.
For example, EPS raw material can be produced as external wall panels, ICF, brick inserts, 3D sandwich panels, colored steel sandwich panels, etc.
Moreover, EPS can be also produced to become ceiling tiles, cornices and etc for the building decoration.
What Are the Benefits of EPS
Expanded Polystyrene (EPS) offers several benefits across various industries and applications. Here are some key advantages of EPS:
Insulation Properties:
EPS is widely recognized for its excellent thermal insulation properties. It is an efficient insulator that helps maintain temperature stability in buildings, reducing energy consumption for heating or cooling.
Lightweight:
EPS is a lightweight material, making it easy to handle and transport. This characteristic is particularly advantageous in construction, packaging, and other applications where weight is a consideration.
Shock Absorption:
EPS has superior shock-absorbing qualities, making it ideal for protective packaging. Its ability to cushion and absorb impact energy makes it valuable for shipping delicate and fragile items, such as electronics and glass.
Versatility:
EPS is a versatile material that can be easily shaped, molded, and cut into various forms. Its adaptability makes it suitable for a wide range of applications, from construction and packaging to crafting and custom designs.
Cost-Effective:
EPS is a cost-effective material, both in terms of production and application. Its affordability makes it a popular choice for insulation in construction, as well as for packaging solutions.
Water-Resistant:
EPS is inherently water-resistant, as its closed-cell structure prevents water absorption. This property is beneficial in construction applications, where moisture resistance is important.
Chemical Resistance:
EPS is resistant to chemicals, making it suitable for applications where exposure to certain substances is a consideration. This property enhances its durability in various environments.
Buoyancy:
Due to its closed-cell structure, EPS is buoyant and does not absorb water. This makes it suitable for use in applications such as marine floats and buoys.
Ease of Installation:
In construction, EPS insulation panels are easy to install, contributing to time and labor savings. The lightweight nature of EPS also makes it easier to handle during construction projects.
Recyclability:
While challenges exist, EPS is recyclable, and efforts are being made to improve recycling infrastructure. Recycled EPS can be used to create new products, reducing the demand for virgin materials.
Energy-Efficient Production:
The manufacturing process of EPS requires less energy compared to some alternative materials, contributing to its energy efficiency and lower environmental impact during production.
While EPS offers these benefits, it is important to consider its environmental impact, especially in terms of recycling and waste management. Ongoing efforts focus on improving the sustainability of EPS and finding alternative materials with reduced environmental implications.
Environmental Facts About EPS
While Expanded Polystyrene (EPS) has several advantageous properties, it is important to consider the environmental aspects. Here are some environmental facts about EPS:
Non-Biodegradable:
EPS is non-biodegradable, meaning it does not naturally break down over time. This characteristic raises concerns about its impact on landfill waste and the environment.
Recyclability:
EPS is recyclable, but recycling facilities for EPS may not be as widely available compared to other materials. Efforts are being made to improve EPS recycling processes, but accessibility varies by region.
Volume and Lightweight:
While EPS is voluminous and lightweight, it can take up significant space in landfills. Its low density contributes to the perception of a larger environmental footprint, even if the material itself is lightweight.
Energy Efficiency in Production:
The manufacturing process of EPS requires less energy compared to some alternative materials. The low energy consumption during production contributes to its overall environmental profile.
Air and Resource Emissions:
During the production of EPS, emissions of volatile organic compounds (VOCs) and other air pollutants can occur. Additionally, the extraction and processing of the raw materials for EPS, such as styrene, have environmental implications.
Waste Reduction Initiatives:
Initiatives and programs exist to reduce EPS waste, including encouraging the use of recycled EPS in various applications. Efforts to minimize the environmental impact of EPS involve waste reduction strategies and promoting recycling where feasible.
Alternative Materials and Solutions:
Some environmental concerns associated with EPS have led to the exploration of alternative materials and sustainable packaging solutions. Biodegradable alternatives and materials with lower environmental impacts are being researched and developed.
Lifecycle Assessments:
Conducting comprehensive lifecycle assessments (LCAs) helps evaluate the overall environmental impact of EPS, considering factors from raw material extraction to production, use, and disposal. LCAs are valuable tools for understanding the environmental implications of different materials.
End of Life About EPS
The end-of-life considerations for Expanded Polystyrene (EPS) involve how the material is managed and disposed of once it has served its primary purpose. Here are key points related to the end-of-life phase for EPS:
Landfill Disposal:
One common end-of-life scenario for EPS is disposal in landfills. As EPS is non-biodegradable, it does not break down naturally over time. Its lightweight and bulky nature can contribute to the use of valuable landfill space.
Recycling:
Recycling is a more environmentally preferable option for EPS disposal. Some regions have established EPS recycling programs, where used EPS products are collected, compacted, and recycled into new materials. Commonly recycled EPS items include packaging materials and insulation.
Challenges in Recycling:
Despite its recyclability, EPS recycling faces challenges, such as transportation costs due to its low weight-to-volume ratio. Additionally, not all recycling facilities are equipped to process EPS, limiting the accessibility of recycling options in certain areas.
Expanded Polystyrene Packaging Recycling:
Efforts are being made to increase EPS packaging recycling rates. Many packaging recycling centers now accept EPS, especially post-consumer foam packaging, to divert it from landfills and encourage more sustainable disposal practices.
Alternative Disposal Methods:
Some regions explore alternative methods for EPS disposal, including energy recovery through incineration. When properly controlled, incineration can generate energy, but it also raises concerns about air emissions and the release of potentially harmful byproducts.
Product Stewardship and Extended Producer Responsibility (EPR):
Product stewardship and extended producer responsibility initiatives advocate for manufacturers to take responsibility for their products throughout their entire lifecycle. This includes developing strategies for the responsible disposal and recycling of EPS products.
Research into Sustainable Alternatives:
Ongoing research and development focus on finding sustainable alternatives to EPS or enhancing its environmental profile. This includes exploring biodegradable materials and developing more eco-friendly foam alternatives.
Public Awareness and Education:
Public awareness and education play a crucial role in encouraging responsible disposal practices. Informing consumers about recycling options and the environmental impact of various disposal methods can influence choices at the end of an EPS product’s life.
Addressing the end-of-life phase of EPS involves a combination of recycling efforts, waste management strategies, exploring alternative disposal methods, and promoting public awareness to minimize the environmental impact of the material after its initial use.
What Is The Difference Between EPS vs XPS?
EPS (Expanded Polystyrene) and XPS (Extruded Polystyrene) are both types of rigid foam insulation materials, but they have distinct differences in terms of manufacturing processes, physical properties, and applications.
Here’s a breakdown of the key differences between EPS and XPS:
Comparison Table:
Property | EPS (Expanded Polystyrene) | XPS (Extruded Polystyrene) |
---|---|---|
Manufacturing Process | Bead expansion with blowing agent | Continuous extrusion process |
Cell Structure | Predominantly closed-cell | Uniform closed-cell structure |
Density | Variable, depending on application | Higher density, better compressive strength |
R-Value | Depends on density, lower R-value for lower density | Higher R-value per inch of thickness |
Water Absorption | Potential for water absorption, especially in lower-density forms | Lower water absorption, more moisture-resistant |
Applications | Construction insulation, packaging, molded products | Below-grade insulation, under-slab insulation, roofing systems |
It’s important to consider these differences when choosing between EPS and XPS, as the suitability of each material depends on the specific requirements of the intended application.
Quote Us for EPS
If you have any questions about EPS (expanded polystyrene), please feel free to contact us at any time, and welcome to contact us at any time if you are looking for the reliable EPS material manufacturer.