Expanded Polystyrene (EPS) is a versatile and widely used material known for its lightweight, insulating properties. This is the step-by-step manufacturing process of how expanded polystyrene is made and provides insight into its production and applications.
The manufacturing of Expanded Polystyrene (EPS) involves a three-step foaming process, using pentane gas as the primary physical foaming agent stored in liquid form within the raw material particles.
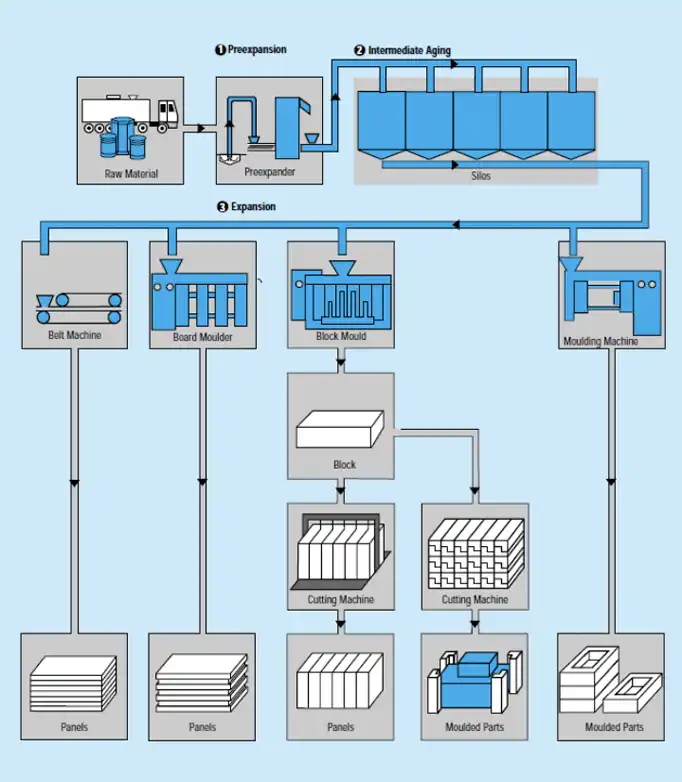
First Foaming: Pre-Expanding EPS Crystals
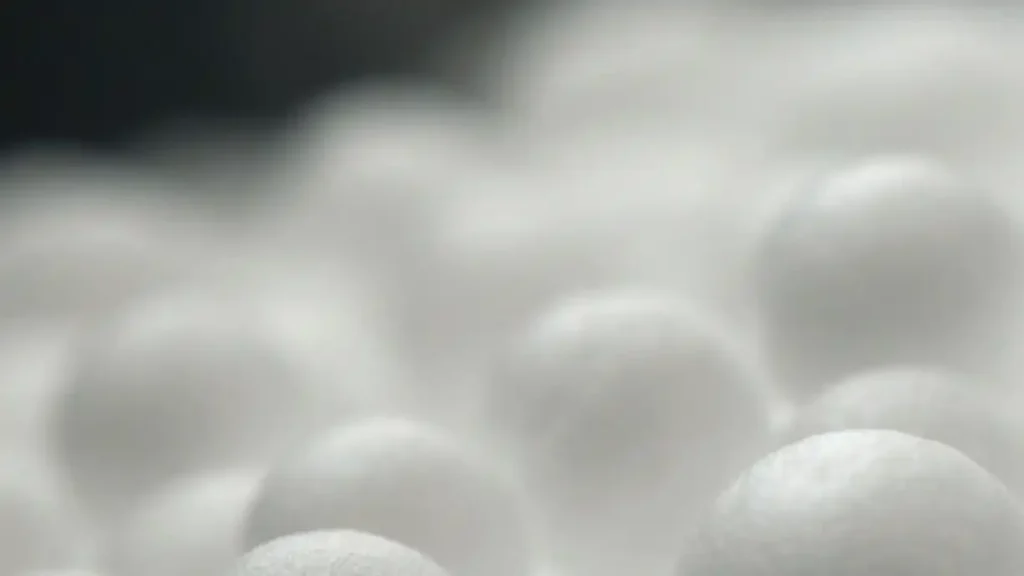
The first foaming, known as pre-expansion, involves expanding individual EPS crystal particles into swollen monomer particles.
The foaming principle works as follows: EPS raw material is heated with steam. When the steam temperature exceeds 80 degrees Celsius (ideal range: 93-102 degrees), polystyrene particles begin to soften. The foaming agent distributed within them undergoes gasification due to the heat, creating pressure that causes the beads to expand, forming non-connected voids.
Steam also permeates into the already expanded voids, increasing the overall pressure inside them. As steam continues to be introduced, the pressure and volume of the beads steadily increase. If steam is continuously applied to the beads, their volume will keep expanding until each thin wall of the voids ruptures.
Continuous steam penetration during pre-expansion is crucial, as the speed of steam entering the voids must exceed the speed at which the foaming agent escapes from the voids. This prevents the foaming agent from escaping, allowing the polymer to stretch into a rubbery state with enough strength to balance internal pressure, thus achieving pre-expansion. Throughout this process, the beads must remain dispersed and freely flowing, typically achieved through continuous mixing of beads and steam in a stirred vessel.
Principle of Foaming: EPS raw material is heated with steam. When the steam temperature surpasses 80 degrees Celsius (ideal range: 93-102 degrees), polystyrene particles start softening. The foaming agent within the particles vaporizes under heat, creating pressure that expands the beads, forming non-connected voids. Continuous steam entry and pressure increase cause the beads to expand until each thin wall of the voids ruptures.
Importance of Steam Permeation: Continuous steam penetration is vital during pre-expansion, increasing the total pressure inside the voids. This ensures the foaming agent remains within the voids, allowing the polymer to stretch like rubber, balancing internal pressure and achieving pre-expansion. The process requires the beads to maintain a dispersed and freely flowing state.
Aging: Storing Pre-Expanded Beads
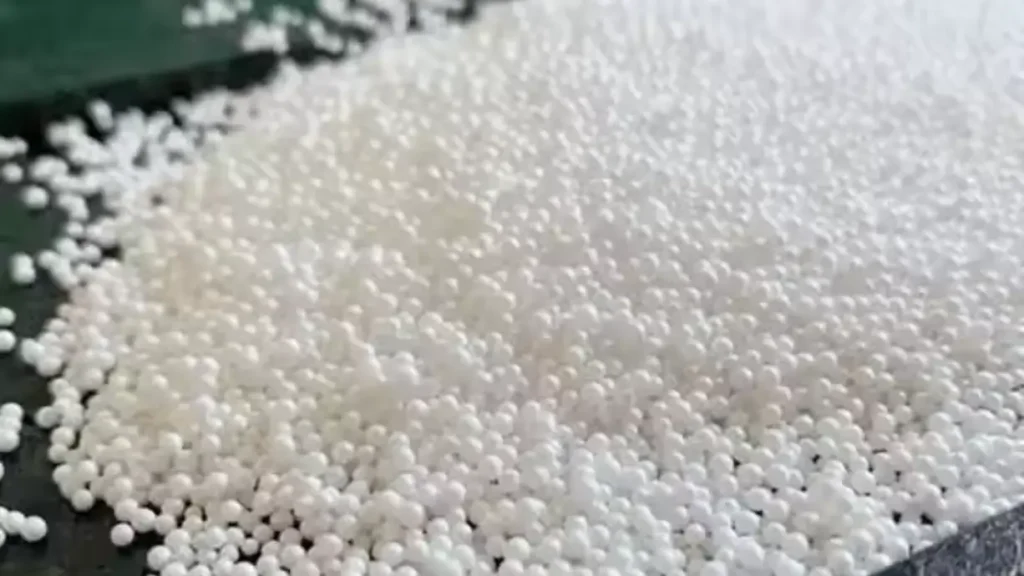
After pre-expansion, the beads undergo a period of storage known as aging to allow them to absorb air. During the aging process, the beads are cooled by air, causing the foaming agent and water vapor inside the voids to condense into a liquid, creating a vacuum within the voids.
Aging involves allowing air to permeate through the thin walls of the voids, balancing the pressure inside with the external pressure. At this stage, the particles that underwent pre-expansion gain elasticity. It’s essential to note that the storage period for the pre-expanded beads should not be excessively long, as the foaming agent diffuses outward during the aging process.
Generally, lighter foam densities have shorter aging times, while heavier densities require longer periods for proper aging.
Second Foaming: Molding Process
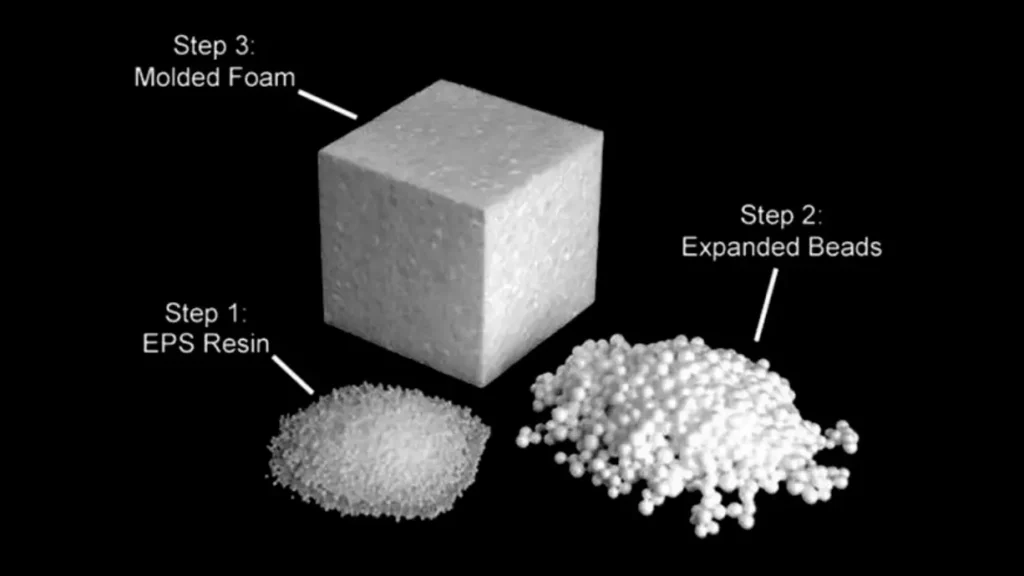
The second foaming, known as the molding process, consists of two stages: steam heating and cooling for shaping. After aging, the pre-expanded beads are subjected to steam heating.
In a brief heating period of approximately 20-60 seconds, air is prevented from escaping. The beads undergo rapid expansion due to heating, generating pressure. The total pressure exceeds the steam pressure applied externally to the beads.
At this point, the polymer softens, and the pressure inside the voids surpasses the external pressure, causing the beads to expand once again. The expanded beads fill the gaps between them, forming a solid block with the same shape as the mold. This results in the creation of foam plastic products, which are then cooled by water for final setting.
Conclusion
Understanding the step-by-step manufacturing process of Expanded Polystyrene sheds light on the intricate methods involved in creating this versatile and widely used material. From pre-expansion to molding, each phase contributes to the final product’s properties and applications.
If you want to know more details about expanded polystyrene production, please feel free to contact us at any time. And please feel free to quote us now to get qualified eps samples.