When you hold a lightweight EPS foam tray, do you ever wonder how it gets its airy, yet strong, structure? The secret lies in something called a blowing agent. These seemingly simple compounds are the true heroes behind the scenes, transforming solid plastic beads into the versatile foam we rely on for countless applications.
This blog post will delve into the fascinating world of blowing agents specifically used in the manufacturing of Expanded Polystyrene (EPS). We’ll uncover how these agents work their magic, from initiating the initial expansion of tiny polystyrene beads to creating the final, perfectly formed and functional EPS product.
What are Blowing Agents for Foams?
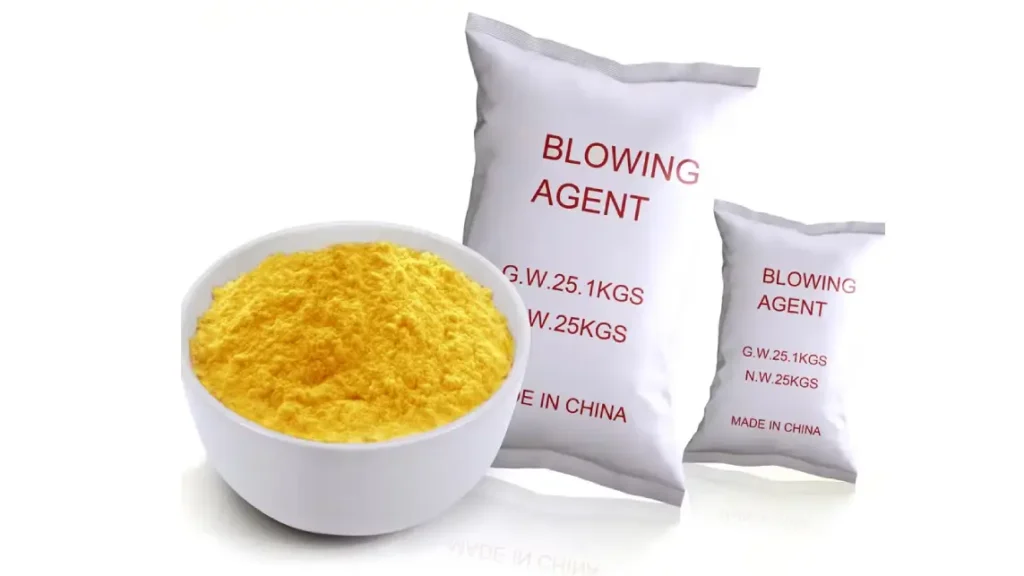
Blowing agents are crucial substances used in the manufacturing of foam materials, like EPS, to create their characteristic cellular structure. These blow agents, which can be physical or chemical, work by producing gas bubbles within a polymer matrix as it cools or cures.
When exposed to heat or pressure changes, physical blowing agents (like pentane in EPS production) vaporize and expand, while chemical blowing agents decompose to release gases such as nitrogen or carbon dioxide. This gas expansion is what “blows up” the material, reducing its density and imparting properties like lightweightness, thermal insulation, and cushioning.
Foam Blowing Agents Examples
Blowing agents for foams fall into two main categories: physical and chemical. Physical blowing agents are substances that are typically gases at the foaming temperature and expand directly, or liquids that vaporize, like pentane, which is a primary example used in EPS production. Chemical blowing agents, on the other hand, undergo a chemical reaction when heated, decomposing to release gases that create the foam structure.

Common examples include:
Physical Blowing Agents:
- Pentane (n-pentane, iso-pentane, cyclo-pentane): Widely used for EPS and XPS (extruded polystyrene) foams, known for low GWP.
- Carbon Dioxide (CO2): Can be used as a liquid injected directly or generated by chemical reactions (e.g., with water in polyurethanes).
- Hydrofluoroolefins (HFOs) and Hydrochlorofluoroolefins (HCFOs): Newer generation, low Global Warming Potential (GWP) alternatives, replacing older fluorocarbons.
- Hydrofluorocarbons (HFCs): Previously common, but being phased out due to high GWP.
- Chlorofluorocarbons (CFCs) and Hydrochlorofluorocarbons (HCFCs): Older agents, largely phased out globally due to their ozone-depleting potential.
Chemical Blowing Agents:
- Azodicarbonamide (ADC): A common organic chemical blowing agent that decomposes to release nitrogen gas.
- Sodium Bicarbonate (Baking Soda): Decomposes to release carbon dioxide gas, often used in less critical foam applications.
- Isocyanates reacting with Water: Used in polyurethane foams, this chemical reaction itself generates CO2 which acts as a blowing agent.
Blowing Agent for Polyethylene Foam
Polyethylene foam, distinct from EPS (Expanded Polystyrene), is also manufactured using blowing agents to create its characteristic cellular structure. The choice of blowing agent for polyethylene (PE) foam depends heavily on the desired properties of the final product, such as cell structure (open or closed cell), density, flexibility, and environmental considerations. PE foams are widely used for cushioning, insulation, and various industrial applications due to their durability and resistance to moisture.
Both physical and chemical blowing agents are employed in polyethylene foam production. Physical blowing agents like butane, nitrogen, or carbon dioxide are often injected directly into the molten polyethylene during an extrusion process.
Chemical blowing agents, such as azodicarbonamide (AZ) or sodium bicarbonate, are compounded into the PE resin and decompose upon heating to release gases. Newer, more environmentally friendly options like Hydrofluoroolefins (HFOs) are increasingly being adopted to replace older blowing agents with higher global warming potential.
Common blowing agents for polyethylene foam include:
Physical Blowing Agents:
- Butane
- Nitrogen (N2)
- Carbon Dioxide (CO2)
- Hydrofluoroolefins (HFOs)
Chemical Blowing Agents:
- Azodicarbonamide (AZ)
- Sodium Bicarbonate (NaHCO3)
How to Use Blowing Agents for EPS
Understanding how blowing agents transform tiny polystyrene beads into rigid EPS foam is crucial. This process precisely controls heat and pressure to expand the beads, fuse them, and create the lightweight, insulating material used in various applications, from packaging to construction.
Step 1: Pre-Expansion
The initial step involves pre-expanding raw polystyrene beads, which contain the blowing agent (typically pentane). In a pre-expander, the beads are exposed to steam. This heat causes the pentane to vaporize and expand, simultaneously softening the polystyrene, leading the beads to puff up significantly into smaller, light “pre-puffs.”
The pre-puffs are then pneumatically conveyed to large silos. Here, they undergo a crucial aging period, allowing them to cool, dry, and reach a stable internal pressure. This stabilization is vital, as it prevents collapse during subsequent processing and ensures the beads have the necessary resilience for the final molding stage.
Step 2: Molding
Aged pre-puffs are fed into a closed mold, which is shaped like the final EPS product (e.g., a tray or block). Steam is injected into the mold. The heat from the steam causes the pentane inside the pre-puffs to expand further, softening the polystyrene again and forcing the beads to tightly fuse together.
This fusion creates a solid, coherent EPS part that perfectly replicates the mold’s interior. After the fusion is complete, the mold is rapidly cooled, typically with water. This cooling sets the shape of the EPS product, preventing it from deforming upon ejection and ensuring its dimensional stability.
Foam Blowing Agent Safety
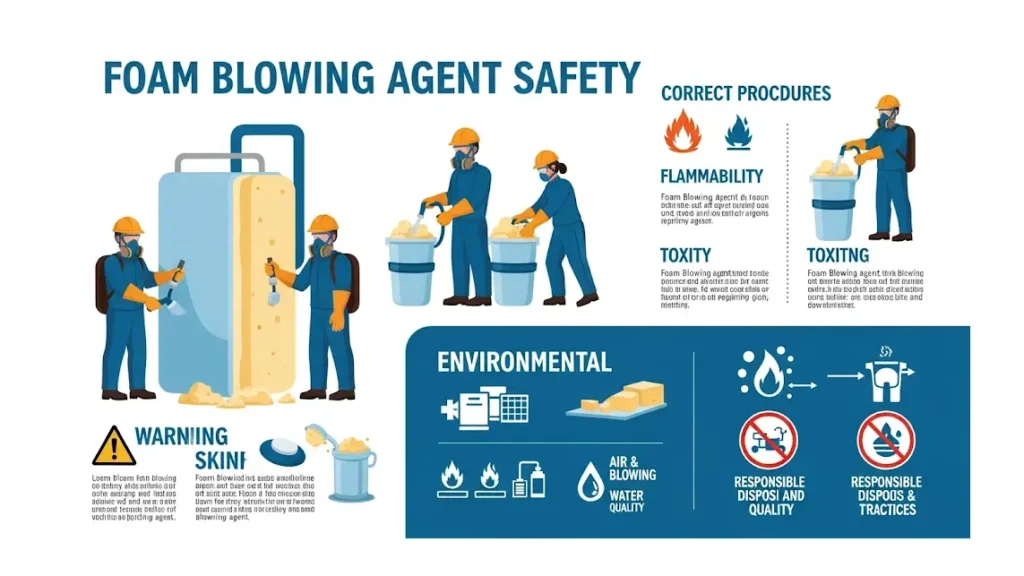
The safety of foam blowing agents is a critical consideration, encompassing both occupational health during manufacturing and their environmental impact after release. Many traditional blowing agents, particularly older generations of fluorocarbons like CFCs and HCFCs, were found to have significant negative effects, contributing to ozone depletion and possessing high Global Warming Potentials (GWPs).
While these have been largely phased out, newer alternatives still require careful handling due to flammability, potential for inhalation risks, or other specific hazards, necessitating strict ventilation, personal protective equipment (PPE), and proper storage protocols in industrial settings.
Occupational Safety:
- Flammability: Some blowing agents, like pentane, are highly flammable and require stringent fire safety measures.
- Inhalation Risks: Vapors or decomposition products can cause respiratory irritation or other health issues if not properly ventilated.
- Chemical Exposure: Direct skin or eye contact with certain agents can cause irritation.
- Explosion Risk: Improper handling or temperature control can lead to rapid gas release and pressure build-up.
Environmental Impact:
- Ozone Depletion Potential (ODP): Older CFCs and HCFCs significantly depleted the ozone layer.
- Global Warming Potential (GWP): Many blowing agents are potent greenhouse gases, contributing to climate change. HFCs, while not ozone-depleting, have high GWPs and are being phased out in favor of low-GWP alternatives like HFOs and hydrocarbons.
- Volatile Organic Compounds (VOCs): Some blowing agents may contribute to air pollution as VOCs.
Why Use Blowing Agents for EPS Foam?
Blowing agents are absolutely essential for creating EPS (Expanded Polystyrene) foam because they are responsible for its distinctive cellular structure, which underpins all of its beneficial properties. Without a blowing agent, polystyrene would remain a solid plastic, incapable of providing the lightweight, insulating, and cushioning characteristics that make EPS so valuable.
They literally “inflate” the plastic, turning a small amount of material into a large volume of foam.
- Material Efficiency: By expanding the plastic, blowing agents enable the creation of large, functional products from minimal raw material.
- Weight Reduction: Blowing agents create air-filled cells, dramatically reducing the density and weight of the final EPS product.
- Thermal Insulation: The trapped air within the foam cells acts as an excellent insulator, slowing heat transfer.
- Shock Absorption/Cushioning: The cellular structure allows EPS to absorb impact energy, protecting fragile items.
Is There a Natural Foaming Agent?
Yes, there are natural foaming agents, particularly in the context of food, personal care products, and some traditional uses. Unlike the synthetic or petrochemical-derived blowing agents used in industrial foam production like EPS, natural foaming agents are typically compounds found in plants or animal products.
These substances, often called saponins (from plants like soapwort, yucca, or quinoa) or proteins (like egg whites or whey protein), work by reducing the surface tension of a liquid, allowing air to be incorporated and stable bubbles to form. While they create foam, their application is generally in aqueous systems for frothing, cleansing, or aeration, rather than creating rigid, low-density foam structures for packaging or insulation like EPS.
Conclusion
We’ve journeyed through the intriguing process of how blowing agents, particularly pentane, are indispensable to EPS manufacturing. These unsung heroes are not just chemicals; they are the architects of the foam’s unique properties, enabling everything from protective packaging to efficient insulation. Understanding their role truly highlights the innovation behind EPS.
The evolution of blowing agent technology continues, driven by both performance demands and environmental responsibility. As industries seek more sustainable and efficient solutions, the methods and materials used to expand EPS will undoubtedly keep advancing, ensuring its continued relevance in diverse applications.
For businesses looking to leverage the benefits of EPS products, understanding this foundational aspect is key. Whether you need protective packaging, insulation, or custom solutions, get wholesale EPS foam products from us, crafted with precision and the latest manufacturing expertise.