Air compressors are like the backbone of factories and workshops worldwide in today’s world of pneumatic tools.
What is an Air Compressor, believe it or not, they’re a new kid on the block when you think about the history of machines.
What is Air Compressor?
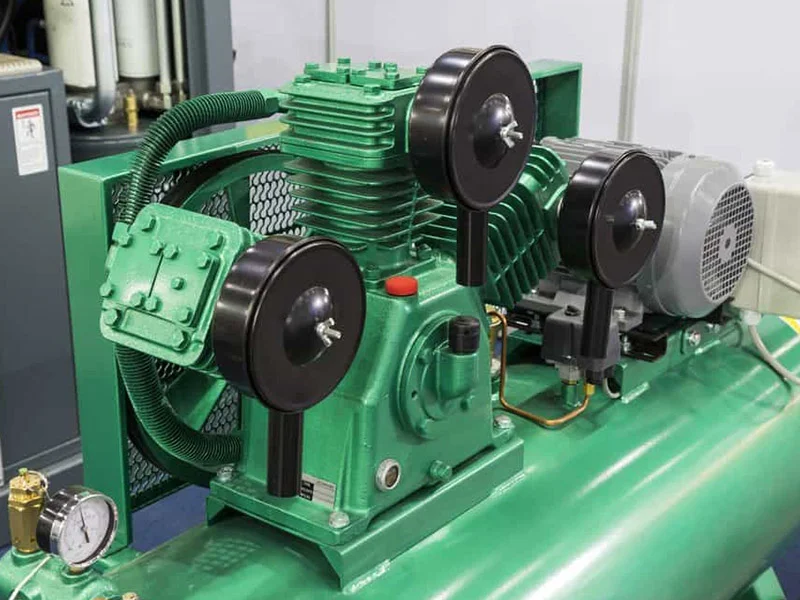
An air compressor is a mechanical device that converts power into potential energy stored in pressurized air. This compressed air can be utilized for various applications, ranging from inflating tires to operating pneumatic tools.
How Do Air Compressors Work?
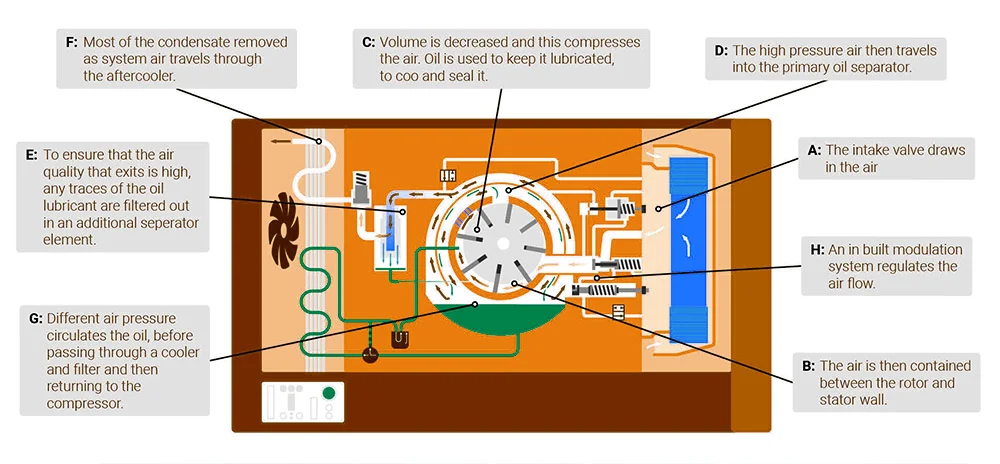
How Air Compressors Work
Air Intake:
The process begins with the air intake, where ambient air is drawn into the compressor through an intake valve or filter.
Compression:
Once inside the compressor, the air is compressed using one of several methods. The most common types of compressors are reciprocating (piston) compressors and rotary screw compressors.
Reciprocating Compressors:
These compressors use pistons driven by a crankshaft to compress air. As the piston moves downward, air is drawn into the cylinder. When the piston moves upward, the air is compressed and pushed out through a discharge valve.
Rotary Screw Compressors:
These compressors use twin rotating screws to compress air. As the screws rotate, they trap air between the lobes and the compressor housing. The air is then compressed as the screws continue to rotate, and it is pushed out through a discharge port.
Air Storage:
The compressed air is discharged into a storage tank or receiver where it is stored at high pressure until needed.
Pressure Regulation:
In many applications, the compressed air must be regulated to a specific pressure. This is typically achieved using pressure regulators or control systems that adjust the compressor’s output to maintain a constant pressure.
Application:
The compressed air is then piped to the point of use where it powers pneumatic tools, and machinery, controls processes, or performs other tasks.
Cycle:
The compressor continues to operate in a cycle, drawing in air, compressing it, and discharging it as needed to maintain the required pressure and supply of compressed air.
Mechanics of Air Compressors
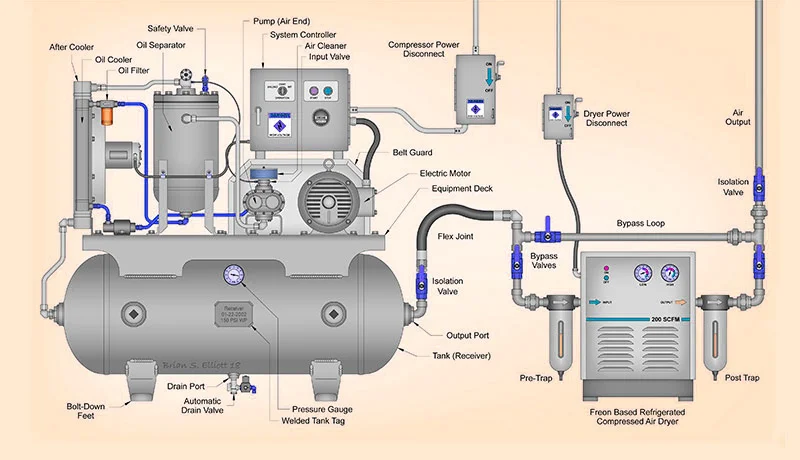
Intake of Air:
Air compressors start by drawing atmospheric air through an intake valve or filter. This air is typically filtered to remove any contaminants or particles that could damage the compressor or affect the quality of the compressed air.
Compression:
The heart of the compressor is where air gets compressed. This can be done through various mechanisms:
Reciprocating Compressors:
These compressors use pistons within cylinders. As the piston moves downward, it creates a vacuum, drawing air into the cylinder. When the piston moves back up, it compresses the air, reducing its volume and increasing its pressure.
Rotary Screw Compressors:
These compressors use intermeshing helical rotors to compress air. As the rotors rotate, air is trapped in the spaces between them and the compressor housing. As the rotors continue to rotate, the air is compressed and pushed towards the outlet.
Heat Generation:
Compression of air generates heat due to the increase in pressure. This heat needs to be managed to prevent damage to the compressor and ensure the quality of the compressed air. Some compressors use intercoolers or aftercoolers to remove excess heat from the compressed air.
Storage:
The compressed air is then stored in a tank or receiver where it is held at a high pressure until needed. This storage allows for a steady supply of compressed air, reducing the workload on the compressor and ensuring a consistent pressure output.
Pressure Regulation:
Compressed air often needs to be regulated to a specific pressure for different applications. Pressure regulators or control systems are used to adjust the compressor’s output to maintain the desired pressure.
Distribution and Application:
The compressed air is then distributed through piping to the point of use where it powers pneumatic tools, machinery, or other devices.
Maintenance: Proper maintenance is crucial for the efficient operation of air compressors. This includes regular inspection, lubrication, and replacement of worn parts to ensure optimal performance and longevity.
What is Air Displacement?
Air displacement lies at the heart of every air compressor, driving its functionality. In the compression process, the internal mechanisms of the compressor engage to propel air through the chamber. There are two primary methods of air displacement employed for this purpose:
Positive Displacement:
This method is prevalent in most air compressors. It involves drawing air into a chamber, where the volume of the chamber is reduced to compress the air. Subsequently, the compressed air is transferred into a storage tank for future use.
Dynamic Displacement:
Also known as nonpositive displacement, this approach utilizes an impeller equipped with rotating blades to intake air into the chamber. The kinetic energy generated by the blade movement accelerates air pressure buildup swiftly. Dynamic displacement is commonly employed in turbocompressors due to its rapid operation and capacity to generate large volumes of compressed air. Turbochargers in automobiles frequently utilize dynamic displacement air compressors.
Air Compressor Power Ratings What is CFM Air Compressor?
CFM stands for “Cubic Feet per Minute.” It is a measure of the volumetric flow rate of air that an air compressor can deliver or the amount of air that passes through a system in one minute.
In the context of air compressors, CFM is an important metric as it indicates the compressor’s capacity or the volume of air it can produce at a given pressure level. Essentially, CFM tells you how much air the compressor can deliver to power pneumatic tools, machinery, or other devices.
When choosing an air compressor, it’s essential to consider both the pressure (usually measured in pounds per square inch or PSI) and the CFM rating. The CFM requirement depends on the specific tools or equipment you plan to use with the compressor. Different tools have different CFM requirements, so it’s crucial to match the compressor’s CFM rating with the requirements of your tools to ensure they operate effectively.
For example, if you have a pneumatic tool that requires 5 CFM at 90 PSI, you would need an air compressor capable of delivering at least 5 CFM at 90 PSI to power that tool properly.
In summary, CFM is a measure of airflow capacity and is a critical factor to consider when selecting an air compressor for your specific application.
What is an Air Compressor Used For?
Air compressors have a wide range of applications across various industries and settings due to their ability to generate and store compressed air. Some common uses of air compressors include:
Powering Pneumatic Tools:
Air compressors are extensively used to power pneumatic tools such as drills, nail guns, impact wrenches, sanders, grinders, and paint sprayers. These tools rely on compressed air to perform various tasks efficiently.
HVAC Systems:
Air compressors play a crucial role in heating, ventilation, and air conditioning (HVAC) systems. They are used to compress refrigerant gases in air conditioning units, providing the necessary pressure to circulate and cool air within buildings.
Spray Painting and Finishing: Air compressors power spray guns used for painting cars, furniture, and other surfaces. They deliver a consistent stream of compressed air to atomize paint and apply it evenly, resulting in smooth finishes.
Cleaning and Blowing:
Air compressors are used for cleaning tasks such as blowing dust and debris from surfaces, machinery, and work areas. They are also used in applications like pressure washing and cleaning equipment in industries such as automotive, manufacturing, and agriculture.
Construction and Demolition: In construction sites, air compressors power pneumatic tools for tasks like driving nails, cutting metal, breaking concrete, and drilling holes. They provide portable and reliable power for a wide range of construction activities.
Medical Equipment:
Air compressors are used in medical devices such as nebulizers, which convert liquid medication into a fine mist for inhalation by patients with respiratory conditions.
Scuba Diving: High-pressure air compressors are used to fill scuba diving tanks with compressed air for recreational and professional diving purposes.
Food and Beverage Industry:
Air compressors are employed in food processing and packaging operations for tasks like controlling pneumatic valves, operating conveyor systems, and providing air for product handling.
These are just a few examples of the diverse applications of air compressors across various industries and sectors. Their versatility, efficiency, and reliability make them indispensable tools in numerous settings.
What is an Air Compressor Used for in an Industry?
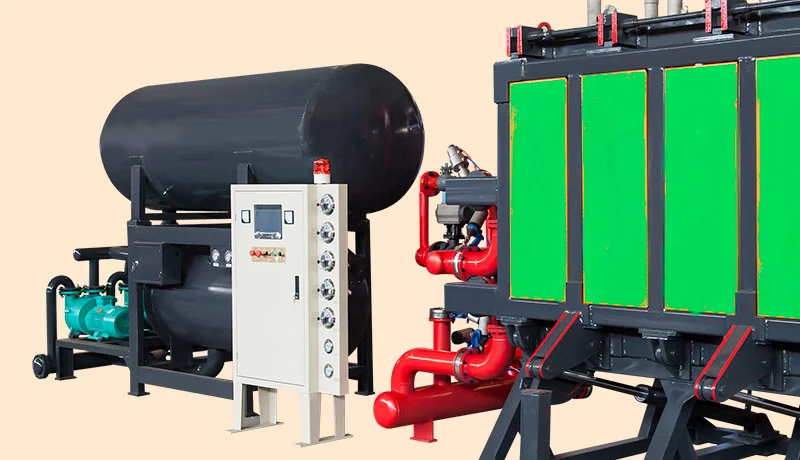
Automation and Control Systems:
Air compressors provide compressed air for operating pneumatic actuators and cylinders in automation and control systems. This enables precise and controlled movement of machinery, valves, and components in manufacturing processes, assembly lines, and industrial equipment.
Instrumentation and Process Control:
Compressed air is used in instrumentation and process control systems to actuate valves, regulate flow rates, and control pressure levels in industrial processes such as chemical processing, refining, and wastewater treatment.
Material Handling and Conveying:
Air compressors power pneumatic conveying systems used for transporting bulk materials such as powders, granules, and pellets in industries like food processing, pharmaceuticals, plastics, and agriculture. These systems utilize compressed air to convey materials through pipelines or ducts to different processing or storage locations.
Power Generation and Energy Storage:
In some industries, air compressors are used as energy storage devices in compressed air energy storage (CAES) systems. These systems store excess energy from renewable sources or off-peak electricity generation by compressing air into underground reservoirs or storage tanks. The compressed air can later be released to drive turbines and generate electricity during periods of high demand.
Let me give you an example, In EPS (Expanded Polystyrene) production lines, air compressors are commonly used in the process of molding or shaping the expanded polystyrene foam.
Types of Air Compressors
There are several types of air compressors, each with its own unique design, operating principles, and applications. Here are some common types of air compressors:
Reciprocating (Piston) Compressors:
Reciprocating compressors use pistons driven by a crankshaft to compress air.
They are available in both single-stage and two-stage configurations.
Single-stage compressors compress air in a single step, while two-stage compressors compress air in two stages for higher pressures.
They are versatile and widely used in small to medium-scale applications such as workshops, automotive repair, and construction.
Rotary Screw Compressors:
Rotary screw compressors use rotating screws (male and female rotors) to compress air.
As the screws rotate, air is trapped between the lobes and compressed as it moves along the rotors.
They are known for their continuous and efficient operation, making them suitable for industrial applications with high air demand.
Rotary screw compressors are commonly used in manufacturing, automotive, and large-scale industrial processes.
Centrifugal Compressors:
Centrifugal compressors use a rotating impeller to accelerate air and convert kinetic energy into pressure.
They are dynamic compressors, meaning they continuously accelerate the air to high speeds before slowing it down to increase pressure.
Centrifugal compressors are capable of delivering high flow rates and are used in large-scale industrial applications such as petrochemical plants, gas pipelines, and power generation.
Scroll Compressors:
Scroll compressors use spiral-shaped scrolls to compress air.
One scroll remains stationary while the other orbits eccentrically, trapping and compressing air between the scrolls.
They are known for their quiet operation, reliability, and compact design.
Scroll compressors are commonly used in applications such as air conditioning, refrigeration, and medical equipment.
Axial Compressors:
Axial compressors are primarily used in gas turbine engines and jet engines for aircraft propulsion and power generation.
They use multiple stages of rotating blades to compress air axially along the compressor shaft.
Axial compressors are known for their high efficiency and ability to generate high pressures and flow rates.
Portable and Tire Inflators:
These are compact, lightweight compressors designed for portability and convenience.
They are often used for inflating tires, sports equipment, inflatable toys, and air mattresses.
Portable compressors typically use piston or diaphragm mechanisms and are powered by electricity, gasoline engines, or rechargeable batteries.
Each type of air compressor has its advantages, limitations, and suitability for specific applications. The choice of compressor depends on factors such as required pressure, flow rate, duty cycle, space constraints, and budget.
Air Compressor Maintenance
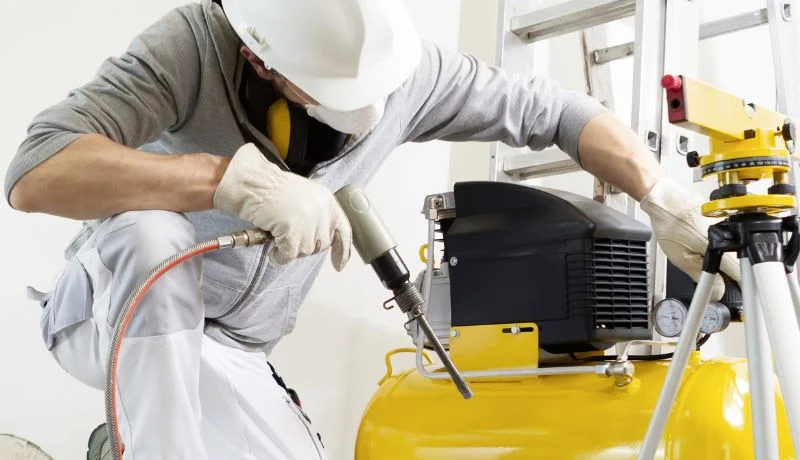
Proper maintenance of your air compressor is essential to ensure its longevity and optimal performance. Here are some key maintenance tasks to keep your air compressor in top condition:
Check Oil Levels:
In a rotary screw compressor, oil should be changed about every 7000-8000 hours. Regularly inspect the oil levels in your compressor’s crankcase. Low oil levels can lead to increased friction and premature wear of internal components. Refer to your compressor’s manual for the recommended oil type and interval for oil changes.
Inspect for Leaks:
Periodically check for air leaks in the compressor system, including hoses, fittings, and connections. Leaks can lead to decreased efficiency and wasted energy. Repair any leaks promptly to maintain optimal air pressure.
Clean Air Filters:
Clean or replace the air filters according to the manufacturer’s recommendations. Dirty air filters restrict airflow, reducing the compressor’s efficiency and potentially causing overheating. Regular maintenance of air filters ensures proper air intake and quality.
Drain Condensate:
Moisture can accumulate in the compressor tank over time, leading to rust and corrosion. Drain the condensate from the tank regularly to prevent water buildup. Use a moisture trap or automatic drain valve to remove condensate efficiently.
Inspect Belts and Pulleys:
Check the condition of drive belts and pulleys for signs of wear or damage. Replace worn-out belts and ensure proper tension to maintain smooth operation and prevent slippage.
Clean Cooling System:
Keep the compressor’s cooling system clean and free from debris, dust, and dirt. Ensure adequate airflow around the compressor to prevent overheating. Regularly inspect cooling fins and clean them if necessary to optimize cooling efficiency.
Check Safety Features:
Verify that all safety features, such as pressure relief valves and safety switches, are functioning correctly. Test these features periodically to ensure they activate as intended in case of emergencies.
Inspect Electrical Components:
Inspect electrical connections, wires, and components for signs of damage or wear. Tighten loose connections and replace any faulty electrical parts to prevent electrical hazards and ensure reliable operation.
By following these maintenance guidelines, you can prolong the lifespan of your air compressor and ensure safe and efficient operation for years to come. Regular maintenance not only prevents costly repairs but also enhances the performance and reliability of your compressor.
Conclusion
In conclusion, air compressors play a vital role in numerous industries and applications worldwide. From powering pneumatic tools to supporting HVAC systems and even contributing to energy storage, their versatility and efficiency make them indispensable. With various types available, each tailored to specific needs, air compressors continue to drive productivity and innovation across diverse sectors.
FAQs
What’s the difference between oil-lubricated and oil-free air compressors?
Oil-lubricated compressors require regular oil changes and offer quieter operation and longer lifespan. Oil-free compressors eliminate the need for oil changes but may have a shorter lifespan and produce more noise.
What is the test method for commercial and industrial air compressors?
The test method for commercial and industrial air compressors typically involves evaluating various performance parameters to ensure they meet industry standards and specifications. Some common test methods include:
CFM and PSI Testing:
Measure the compressor’s cubic feet per minute (CFM) output at various pressure levels (PSI) to verify its capacity and performance.
Efficiency Testing:
Assess the compressor’s energy efficiency by measuring power consumption and comparing it to the amount of compressed air produced.
Noise Level Testing:
Evaluate the compressor’s noise emissions to ensure they comply with regulatory standards and workplace safety requirements.
Reliability and Durability Testing:
Conduct tests to assess the compressor’s reliability, durability, and lifespan under various operating conditions, including temperature extremes and continuous operation.
Vibration Testing:
Measure the compressor’s vibration levels to ensure they are within acceptable limits and do not indicate potential mechanical issues or premature wear.
Leakage Testing:
Check for air leaks in the compressor system, including fittings, hoses, and valves, to ensure efficient operation and prevent energy waste.
Safety Testing:
Verify that the compressor meets safety standards and regulations, including pressure relief valve testing, electrical safety checks, and component integrity assessments.
Are Air Compressors Energy-Efficient?
Air compressors consume up to 10% of the global industrial electricity. “Oil-Free” rotary screws and reciprocating compressors also lose efficiency over time due to wear on the PTFE-like coating on the screws and deterioration of the lubricant, and compressor’s internal mechanisms causing them to consume greater amounts of electricity.