In an era where environmental conservation is a global priority, industries are constantly seeking effective ways to reduce their carbon footprint and mitigate pollution. One such technology that has proven instrumental in controlling industrial pollution is the Thermal Oxidizer.
This piece explores the concept, operation, types, and benefits of thermal oxidizers, offering a comprehensive understanding of this crucial environmental technology.
What is a Thermal Oxidizer
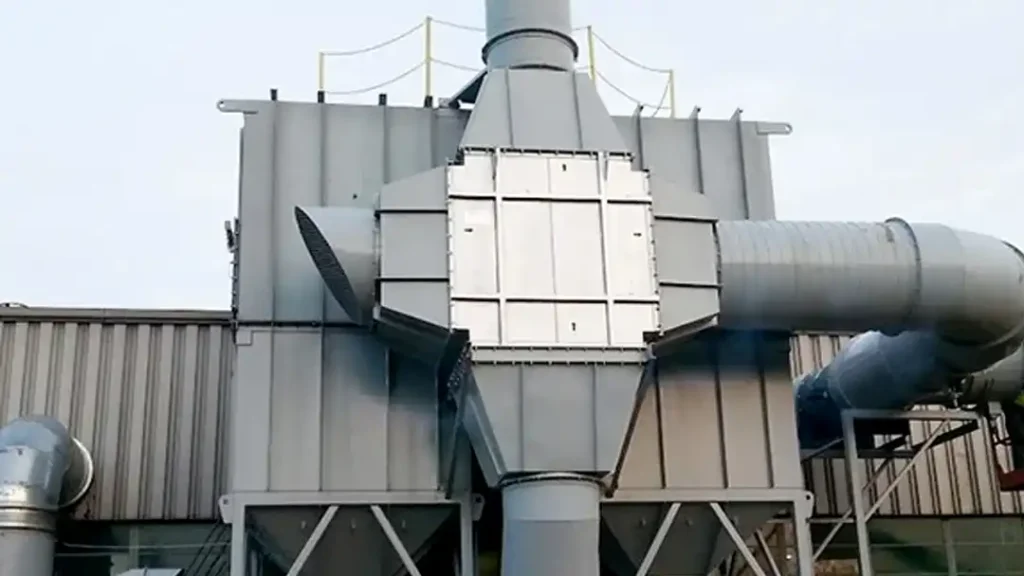
A Thermal Oxidizer, often referred to as a TO, is an industrial machine designed to decompose hazardous gases at high temperatures and convert them into less harmful byproducts before they are released into the atmosphere. The primary purpose of a thermal oxidizer is to treat air pollutants and volatile organic compounds (VOCs) that are often byproducts of various industrial processes.
How Does a Thermal Oxidizer Work?
The operation of a thermal oxidizer is based on the principle of thermal oxidation, which uses high temperatures, typically ranging between 815°C (1500°F) and 980°C (1800°F), to promote a chemical reaction. This reaction involves the oxidation of hazardous organic compounds to form carbon dioxide and water vapor.
The process within a thermal oxidizer can be broken down into three main stages:
- Preheating Stage: In this initial phase, the waste gas stream is directed into a heat exchanger where it is preheated before entering the combustion chamber.
- Combustion Stage: The preheated gases are then introduced into the combustion chamber, where they are heated to the required temperature to facilitate the oxidation process. The residence time (time the gases spend in the combustion chamber) is also crucial to ensure complete oxidation.
- Heat Recovery Stage: The hot, clean gas is then passed back through the heat exchanger to preheat the incoming waste gas, improving the overall energy efficiency of the system.
What Does a Thermal Oxidizer Do
A thermal oxidizer is an industrial machine designed to control air pollution by decomposing hazardous gases at high temperatures and converting them into less harmful byproducts before they are released into the environment.
Here’s a breakdown of what a thermal oxidizer does:
1. Treatment of Pollutants:
The primary function of a thermal oxidizer is to treat air pollutants, known as Volatile Organic Compounds (VOCs), and Hazardous Air Pollutants (HAPs). These harmful gases are often byproducts of various industrial processes such as manufacturing, chemical processing, and oil and gas production.
2. Thermal Oxidation:
Thermal oxidizers work on the principle of thermal oxidation, which uses high temperatures, typically between 815°C (1500°F) and 980°C (1800°F), to promote a chemical reaction. This reaction involves the oxidation of hazardous organic compounds to form carbon dioxide and water vapor, which are less harmful to the environment.
3. Energy Efficiency:
Most modern thermal oxidizers are designed to be energy efficient. They achieve this through heat recovery systems that capture and reuse the heat generated from the oxidation process. This heat is used to preheat the incoming waste gas stream, reducing the amount of supplemental fuel required and thus saving energy.
4. Compliance with Regulations:
By effectively controlling the emission of harmful gases, thermal oxidizers help industries comply with local and international environmental regulations. Failure to meet these regulations can result in hefty fines and sanctions, making thermal oxidizers an essential component of industrial operations.
Thermal Oxidation Advantages and Disadvantages
Thermal oxidation is a widely used method for the treatment of volatile organic compounds (VOCs), hazardous air pollutants (HAPs), and other industrial waste gases. Below is a detailed point-wise breakdown of its advantages and disadvantages:
Advantages of Thermal Oxidation
1. High Efficiency
- Destruction Efficiency: Thermal oxidizers can achieve destruction efficiencies of 95-99.99%, effectively reducing pollutants.
- Broad Applicability: Can be used to treat a wide range of organic compounds.
2. Reliability
- Proven Technology: Well-documented and extensively used in various industries, providing a track record of reliability.
- Operational Stability: Less susceptible to variability in waste gas composition compared to biological treatment methods.
3. Heat Recovery
- Energy Efficiency: Advanced systems like Regenerative Thermal Oxidizers (RTOs) and Recuperative Thermal Oxidizers are designed to recover heat, reducing fuel consumption.
- Cost Savings: Reduced operational costs through heat recovery, especially important in energy-intensive processes.
4. Environmental Compliance
- Regulatory Acceptance: Meets stringent environmental regulations by effectively reducing emissions of VOCs and HAPs.
- Permitting: Easier to obtain permits for thermal oxidizers compared to emerging or less proven technologies.
5. Flexibility
- Scalability: Can be scaled up or down to meet the specific requirements of different processes.
- Adaptability: Can handle varying concentrations and types of pollutants.
6. Safety
- Contained Process: Minimizes the risk of releasing untreated pollutants into the environment.
Disadvantages of Thermal Oxidation
1. High Initial Cost
- Capital Expenditure: Initial costs for purchasing and installing thermal oxidizers can be significant, especially for complex systems like RTOs.
- Auxiliary Components: Additional costs for components, such as backup fuel systems, heat exchangers, and control systems.
2. Operational Costs
- Fuel Consumption: Continuous fuel requirements can lead to high operational costs, particularly in non-heat-recovery systems.
- Maintenance: Regular maintenance is required to ensure optimal performance, which can add to operational expenses.
3. Energy Intensity
- High Temperatures: Operation at high temperatures (up to 1000°C) necessitates considerable energy input, making it less sustainable in regions with expensive fuel resources.
- Emission of CO2: Combustion processes inherently produce carbon dioxide, contributing to greenhouse gas emissions.
4. Complex Installation
- Space Requirements: Installation can be complex and may require significant space in industrial settings.
- Integration: Integrating the system with existing plant infrastructure can be a logistical challenge.
5. Specific Applications
- Limited to Organic Compounds: Primarily effective for organic pollutants; other methods may be needed for inorganic or particulates.
- Temperature Sensitivity: Certain pollutants might decompose into hazardous byproducts if not properly managed.
6. Environmental Impact
- Byproducts: The production of secondary pollutants (e.g., NOx) may require additional control systems.
- Resource Consumption: Use of natural gas or other fuels increases resource consumption and environmental footprint.
Types of Thermal Oxidizers
There are several types of thermal oxidizers, each designed to handle specific types of waste gases and operational conditions. The most common types include:
- Direct Fired Thermal Oxidizers (DFTO): Also known as afterburners, DFTOs are the simplest form of thermal oxidizers. They are highly efficient and suitable for waste streams with high VOC concentrations.
- Regenerative Thermal Oxidizers (RTO): RTOs are known for their high energy efficiency. They utilize ceramic heat exchange media to recover and reuse heat, making them ideal for low VOC concentrations.
- Catalytic Thermal Oxidizers: These oxidizers use a catalyst to promote the oxidation process at lower temperatures, thus saving energy. They are suitable for clean, low particulate waste gas streams.
What is the Temperature of Thermal Oxidizer
A thermal oxidizer operates at extremely high temperatures to effectively oxidize harmful pollutants.
The exact operating temperature can vary depending on the specific type of thermal oxidizer and the nature of the pollutants, but generally, the temperature range is between 815°C (1500°F) and 980°C (1800°F).
This high-temperature environment facilitates the chemical reaction that transforms volatile organic compounds (VOCs) and hazardous air pollutants (HAPs) into less harmful substances, typically carbon dioxide and water vapor.
The precise temperature needed within this range depends on the type and concentration of the pollutants, the residence time (how long the pollutants stay in the oxidizer), and the specific requirements of the process and regulatory environment.
Benefits of Thermal Oxidizers
Thermal oxidizers offer several benefits, key among them being:
- Pollution Control: They efficiently convert harmful pollutants into less harmful substances, thus reducing industrial pollution.
- Energy Efficiency: With heat recovery systems, thermal oxidizers can reuse heat from the oxidation process, reducing energy consumption.
- Regulatory Compliance: They help industries meet local and international environmental regulations regarding air pollution.
- Versatility: Thermal oxidizers can handle a wide range of waste gases, making them suitable for various industrial applications.
Conclusion
Thermal Oxidizers represent a pivotal advancement in industrial pollution control technology. By converting harmful emissions into less detrimental substances, they play a significant role in environmental conservation.
As industries continue to seek sustainable and efficient waste management solutions, the importance of understanding and optimizing the use of thermal oxidizers cannot be overstated.