In the modern industrial landscape, maintaining a balance between operational efficiency and environmental responsibility is crucial. One of the key players in achieving this balance is a device known as a thermal oxidizer. But how exactly do these machines work?
Let’s dive in.
What is a Thermal Oxidizer
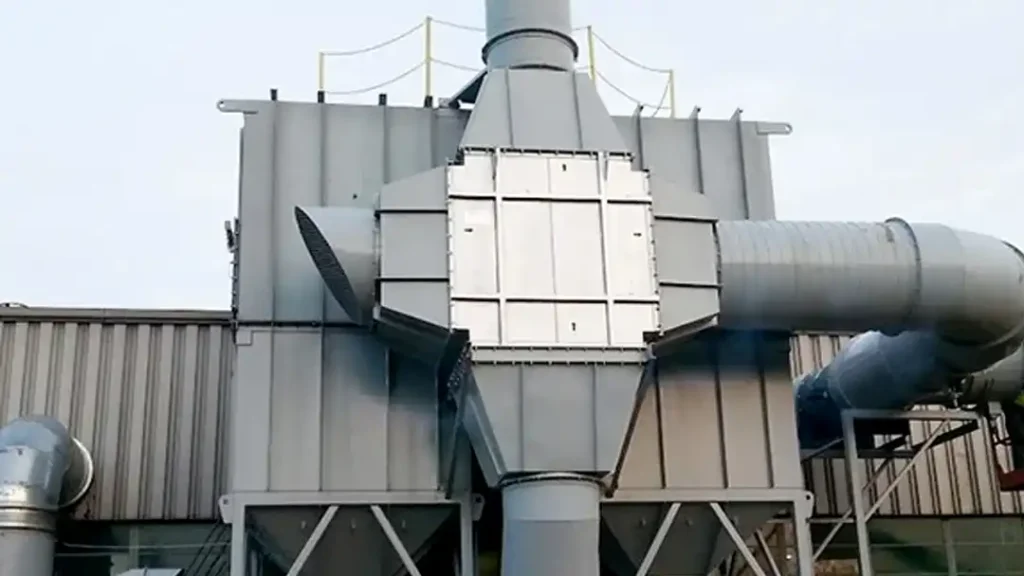
A thermal oxidizer is a piece of equipment used in industrial settings to help reduce harmful emissions. Its primary function is to decompose hazardous gases at high temperatures, transforming them into less harmful byproducts before they are released into the environment.
These machines play a vital role in controlling air pollution, treating Volatile Organic Compounds (VOCs) and Hazardous Air Pollutants (HAPs) that are often byproducts of various industrial processes.
The Working Principle of Thermal Oxidizers
The fundamental principle behind the operation of thermal oxidizers is thermal oxidation. This process involves the use of high temperatures, typically between 815°C (1500°F) and 980°C (1800°F), to promote a chemical reaction. This reaction oxidizes the hazardous organic compounds, converting them into carbon dioxide and water vapor, which are significantly less harmful to the environment.
The Process Flow of Thermal Oxidizers
The operation of a thermal oxidizer involves several steps:
- Collection of Pollutants: The process begins with the collection of waste gases from the industrial process. These gases are directed into the thermal oxidizer through a system of ducts.
- Heating: The waste gases are then heated to the required temperature in the combustion chamber of the oxidizer. This is achieved either by directly firing a burner (in direct-fired oxidizers) or by using heat recovered from the oxidation process itself (in recuperative or regenerative oxidizers).
- Oxidation: Once the gases reach the required temperature, the oxidation reaction takes place. The VOCs and HAPs in the waste gases react with the oxygen in the air to form carbon dioxide and water vapor.
- Cooling and Heat Recovery: After the oxidation process, the hot gases are cooled. In energy-efficient thermal oxidizers, the heat from these gases is recovered and used to preheat the incoming waste gases, reducing the amount of supplemental fuel needed.
- Emission: The treated gases, now primarily composed of carbon dioxide and water vapor, are then released into the atmosphere through a stack.
The Importance of Thermal Oxidizers
1. Environmental Protection:
Arguably the most significant role of thermal oxidizers is their contribution to environmental protection. They treat harmful emissions, specifically Volatile Organic Compounds (VOCs) and Hazardous Air Pollutants (HAPs), produced during various industrial processes. By operating at high temperatures, they oxidize these pollutants into less harmful substances – typically carbon dioxide and water vapor – before they are released into the atmosphere. This process significantly reduces the environmental impact of industrial operations.
2. Regulatory Compliance:
Environmental regulations around the world have become increasingly stringent, requiring industries to control and limit their pollutant emissions. Thermal oxidizers help businesses meet these regulatory standards by effectively treating harmful gases before they are emitted. Compliance with these regulations not only helps protect the environment but also prevents the company from incurring penalties, fines, or potential shutdowns.
3. Energy Efficiency:
Modern thermal oxidizers are designed with energy efficiency in mind. They typically include heat recovery systems that capture and reuse the heat generated during the oxidation process. This recovered heat can be used to preheat the incoming waste gas stream or even other processes within the facility, reducing the overall energy consumption and operational costs.
4. Operational Safety:
By eliminating hazardous gases, thermal oxidizers also contribute to a safer working environment. Certain VOCs and HAPs can pose health risks to employees or even be combustible. Treating these gases reduces these risks, contributing to a safer workplace.
5. Versatility:
Thermal oxidizers can be used in a wide range of industries, including oil and gas, chemical manufacturing, food processing, and more. Their versatility makes them a valuable asset in any industrial setting where VOCs and HAPs are a byproduct.
How Does a Regenerative Thermal Oxidizer Work
A Regenerative Thermal Oxidizer (RTO) is a type of thermal oxidizer that uses a unique heat recovery process to minimize operational costs and enhance efficiency. Let’s break down how it works:
1. Waste Gas Inflow
The process begins when the untreated, pollutant-laden exhaust gases from an industrial process are directed into the RTO system. The gases are usually ducted into one of the system’s multiple ‘energy recovery canisters’ filled with ceramic heat exchange media.
2. Heat Absorption
The waste gases first pass through the heat exchange media, which is designed to absorb the heat from the incoming gas. This preheats the gases before they reach the combustion chamber, reducing the amount of additional energy required to reach the necessary oxidation temperature.
3. Thermal Oxidation
The preheated gases then enter the combustion chamber, where they are heated to the required oxidation temperature, typically between 815°C (1500°F) and 980°C (1800°F). At these high temperatures, the Volatile Organic Compounds (VOCs) and Hazardous Air Pollutants (HAPs) in the waste gases are oxidized, converting them into carbon dioxide and water vapor.
4. Heat Recovery
The treated gases, now hot from the oxidation process, are then directed to exit the system through a different energy recovery canister. As the hot gases pass through the heat exchange media in this canister, the media absorbs the heat. The cooled, clean gases are then released into the atmosphere.
5. Regeneration Cycle
The key to the RTO’s efficiency is the ‘regeneration’ cycle. After the heat exchange media in a canister has absorbed heat from the outgoing gases, the flow of gases is switched (or ‘valved over’). The incoming untreated gases are now directed through this hot canister, where the heat is transferred to the incoming gases. This cycle allows the RTO to recover and reuse up to 95% of the heat generated in the oxidation process, significantly reducing the system’s fuel consumption and operational costs.
Conclusion
In conclusion, thermal oxidizers are integral to maintaining a clean, safe, and sustainable industrial environment. Their role in managing air pollution underscores the importance of investing in and maintaining high-quality pollution control equipment.