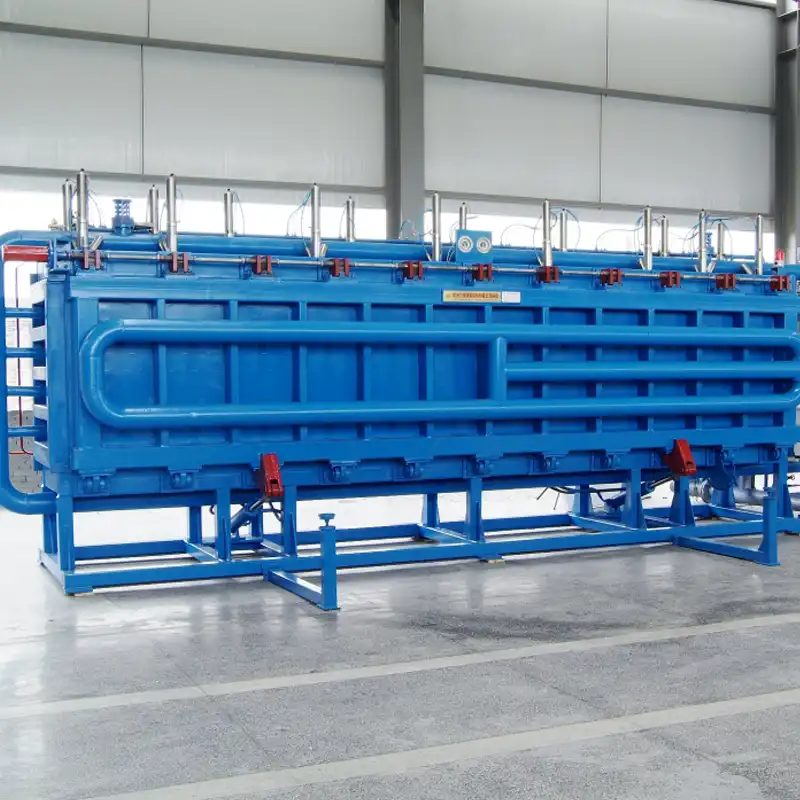
Fully Automatic EPS Sandwich Panel Machine
Streamline Your EPS Panel Production with a Fully Automatic Machine! Tired of manual labor and inefficiency in your EPS panel production? Upgrade to a Fully Automatic EPS Sandwich Panel Machine and revolutionize your business!
Why Choose Our EPS Foam Blocks
Fully automatic EPS sandwich panel machines are available in a variety of specifications and models, but they all share the same basic operating principle. They utilize a hydraulic system and PLC control program to fill the mold cavity with pre-expanded and matured EPS beads. Steam is then introduced directly into the mold cavity through vents in the mold walls using a steam heating system. The residual foaming agent inside the beads softens and expands due to the heat.
The expanding beads fill the entire mold cavity of the machine due to the mold’s constraints, resulting in a completely bonded single unit. After cooling and curing, the finished product can be removed from the machine by opening it.
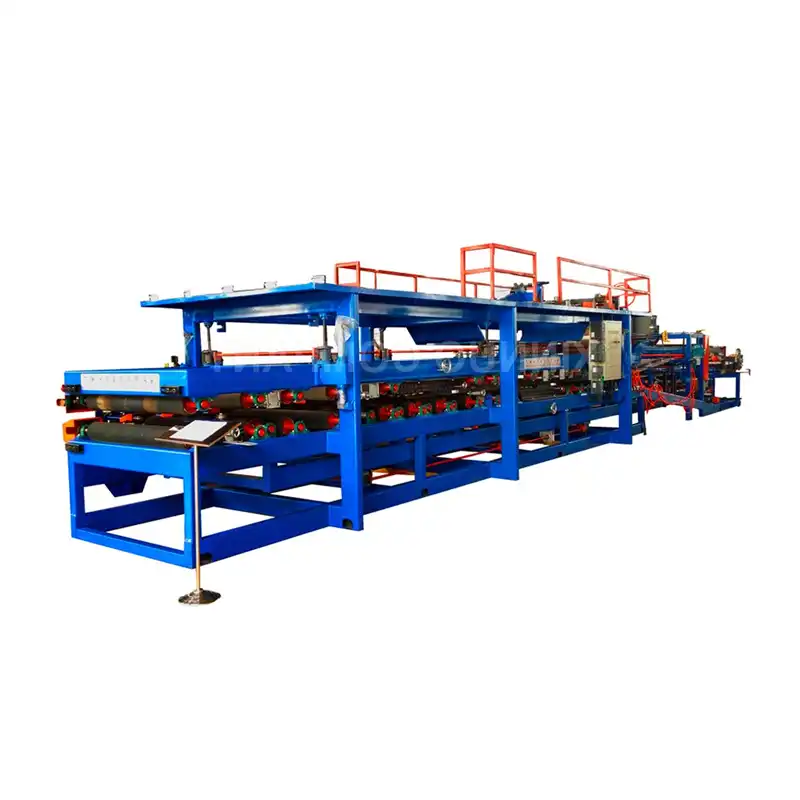
Key Components and Processes:
Pre-expansion and Maturation: EPS beads are subjected to pre-expansion and maturation to ensure uniform expansion and consistent density.
Mold Filling: The pre-expanded and matured EPS beads are loaded into the mold cavity.
Steam Heating: Steam is introduced into the mold cavity to soften and expand the EPS beads further.
Molding and Bonding: The expanding beads fill the entire mold cavity, conforming to its shape and adhering to each other due to the heat and pressure.
Cooling and Curing: The molded EPS panel is cooled and cured to solidify the bond between the beads and achieve the desired product properties.
Panel Ejection: The finished EPS sandwich panel is ejected from the mold.
Fully Automatic EPS Sandwich Panel Machine Working Process
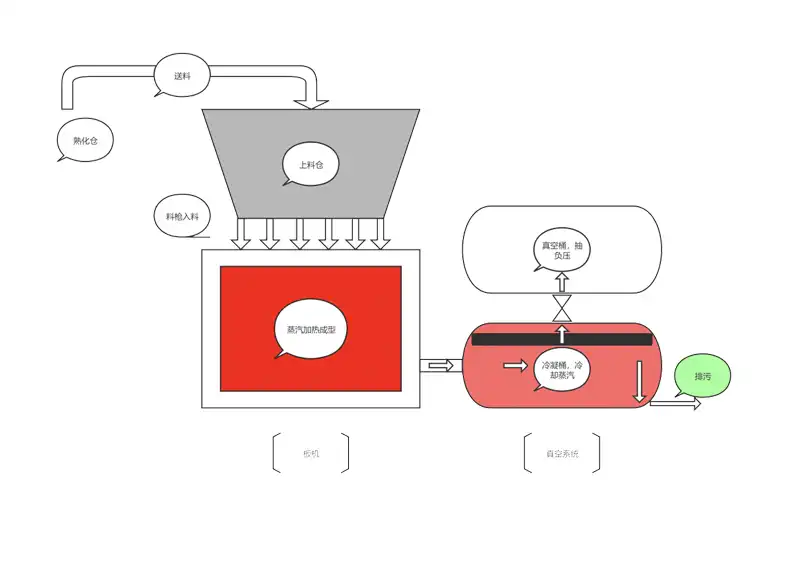
The Automated Journey of an EPS Sandwich Panel: Inside a Fully Automatic Machine
Fully automatic EPS sandwich panel machines take pre-expanded EPS beads and transform them into finished insulation panels with remarkable efficiency.
Here’s a breakdown of the working process of the automatic EPS sandwich panel making machine :
1. Prepping the Players:
The Beads: EPS beads, the core component, undergo pre-expansion and maturation to ensure uniform expansion and consistent density throughout the panel.
2. Filling the Mold:
Ready, Set, Load! The prepped EPS beads are precisely loaded into the mold cavity of the machine. This cavity determines the final shape and size of the finished panel.
3. The Power of Steam:
Heating Up the Action: A steam heating system comes into play. Steam is introduced directly into the mold cavity through vents in its walls.
4. Expansion and Bonding:
Heat Does the Trick: The heat from the steam activates the residual foaming agent inside the beads, causing them to soften and expand further.
Mold Your Destiny: Confined within the mold cavity, the expanding beads fill every nook and cranny, conforming to the mold’s shape.
The Bonding Force: As the beads expand and press against each other due to the heat, they fuse together, forming a single, solid panel.
5. Setting and Cooldown:
Taking Shape: Once the expansion and bonding are complete, the machine allows the molded EPS panel to cool down. This cooling process solidifies the bond between the beads and ensures the panel retains its desired shape and properties.
6. Unveiling the Finished Product:
Voila! Once cooled, the machine automatically opens the mold, and the finished EPS sandwich panel is ejected, ready for further processing or use.
Fully Automatic EPS Sandwich Panel Machine 5 systems
Feeding System
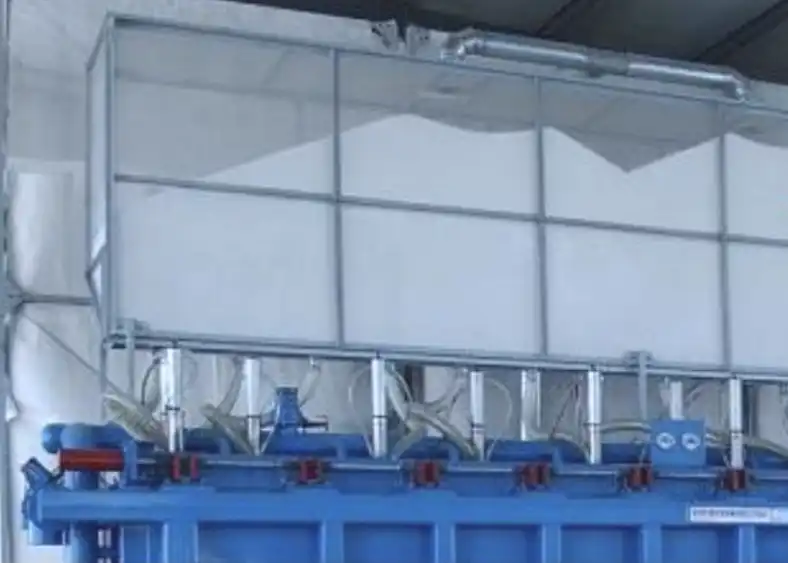
- Purpose: The feeding system is responsible for supplying the pre-expanded EPS beads to the forming machine.
- Components: It typically consists of a silo, conveyor belt, and dosing device to ensure a consistent and controlled supply of beads.
Forming Machine
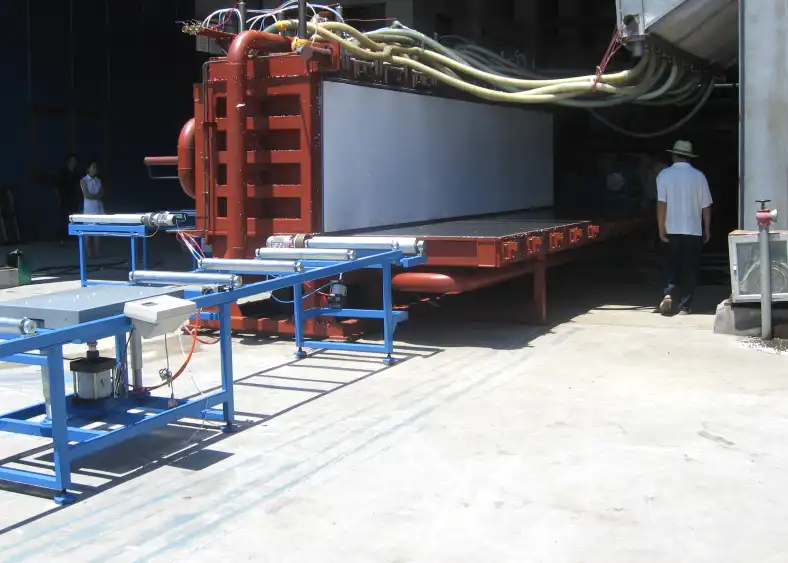
- Purpose: The forming machine shapes the EPS beads into the desired panel profile.
- Components: It comprises a series of rollers that gradually deform the beads into the desired shape and thickness.
Cooling System
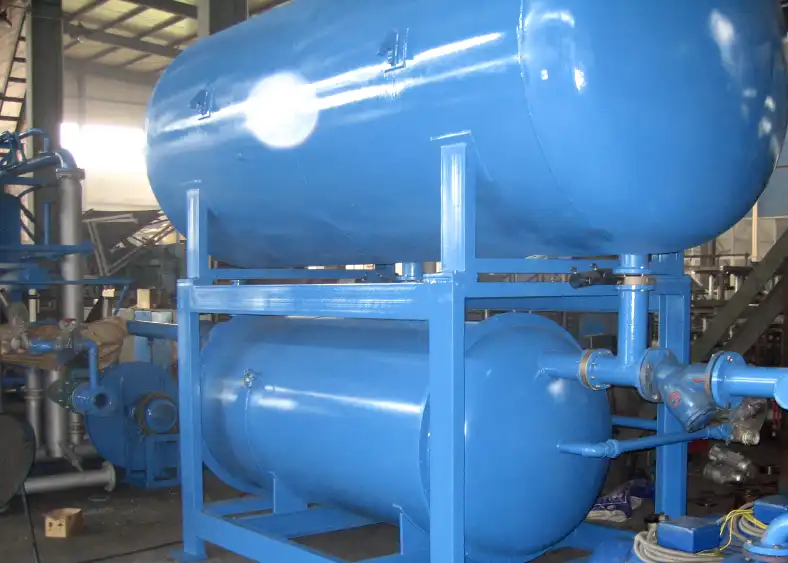
- Purpose: The cooling system rapidly cools the formed EPS panel to solidify the bond between the beads and set the panel’s shape.
- Components: It often employs water-cooled or air-cooled blowers to circulate cool air around the panel.
Hydraulic System

- Purpose: The hydraulic system provides the power to operate the various mechanisms of the machine, including the feeding system, forming machine, and cutting system.
- Components: It consists of a hydraulic pump, reservoir, valves, and cylinders to control the movement and force of the machine’s components.
Weighing System
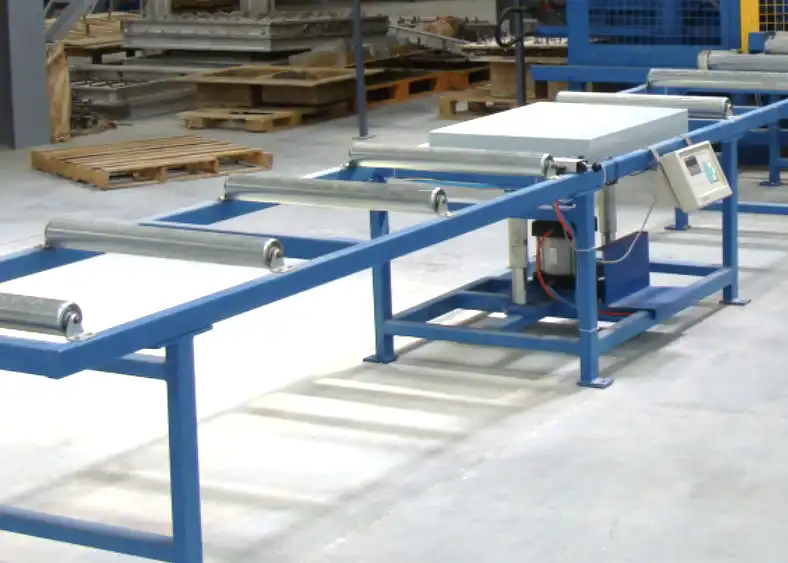
- Purpose: The weighing system ensures that each panel meets the specified weight requirements.
- Components: It typically involves a load cell or weighing platform that measures the weight of the panel as it exits the forming machine.
The five main components – feeding system, forming machine, cooling system, hydraulic system, and weighing system – work in perfect harmony within a fully automatic EPS sandwich panel machine. Each part plays a crucial role:
- The feeding system delivers a consistent flow of beads.
- The forming machine shapes the beads into the desired panel profile.
- The cooling system solidifies the bond and sets the panel’s shape.
- The hydraulic system powers the machine’s operations.
- The weighing system ensures panels meet the specified weight requirements.
By working together, these components enable the machine to produce high-quality EPS sandwich panels efficiently and consistently. This translates to increased production output, improved product quality, and reduced labor costs, making fully automatic EPS sandwich panel machines a valuable asset for manufacturers in the construction and insulation industries.
Fully Automatic EPS Sandwich Panel Machines: Horizontal vs. Vertical
Fully automatic EPS sandwich panel machines offer a streamlined and efficient way to produce high-quality EPS panels. But before you jump in, it’s important to understand the two main types available: horizontal and vertical.
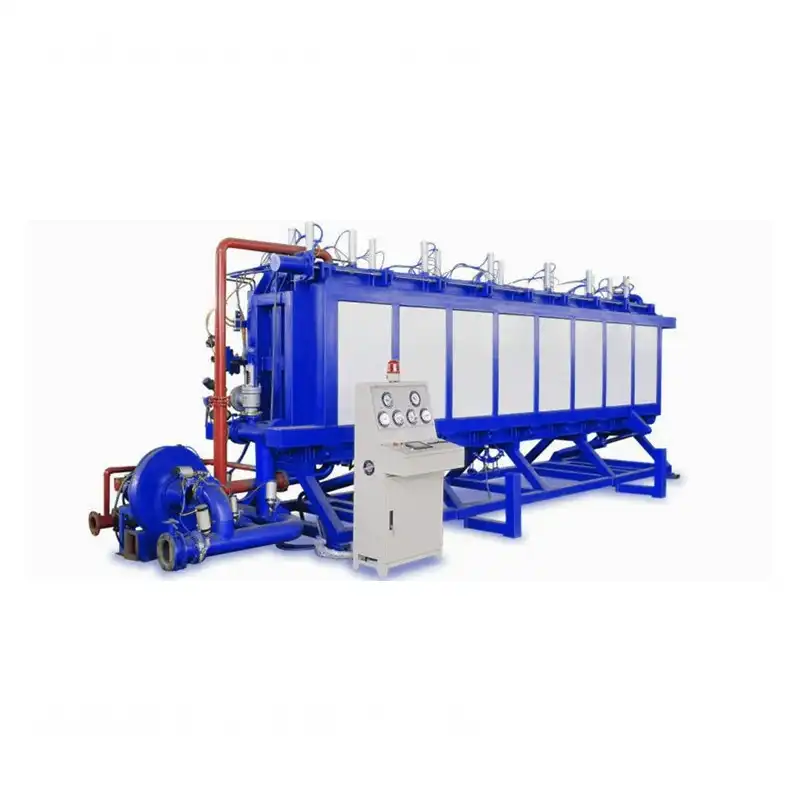
- Orientation: The mold lays flat in a horizontal position.
- Applications: Ideal for high-volume production due to their ability to handle larger capacities.
- Strengths: Can produce panels in a wider range of thicknesses and lengths.
- Considerations: May require a larger footprint compared to vertical machines.
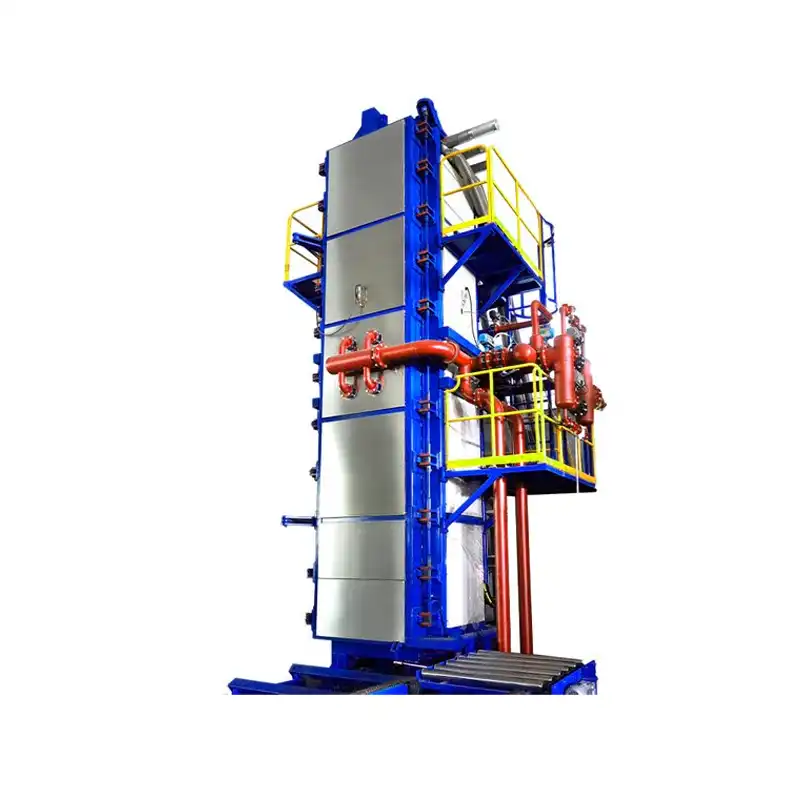
- Orientation: The mold stands upright in a vertical position.
- Applications: Well-suited for smaller production facilities or those with space constraints due to their compact design.
- Strengths: More space-saving compared to horizontal models.
- Considerations: May have limitations on the maximum thickness and length of panels they can produce.
Fully Automatic EPS Sandwich Panel Machine cooling Methods
Cooling is a crucial step in the EPS (expanded polystyrene) sandwich panel production process, as it affects the final product’s quality and performance. Two common cooling methods are vacuum cooling and air cooling.

Vacuum cooling utilizes a vacuum pump to lower the air pressure within the mold cavity, allowing EPS beads to evaporate at a lower boiling point and absorb heat, achieving rapid cooling.
Advantages:
- Fast cooling speed, shortening the production cycle
- Uniform cooling effect, consistent panel density
- High flatness of finished panels, less prone to deformation
Disadvantages:
- Higher equipment cost
- Higher maintenance requirements
- Higher energy consumption
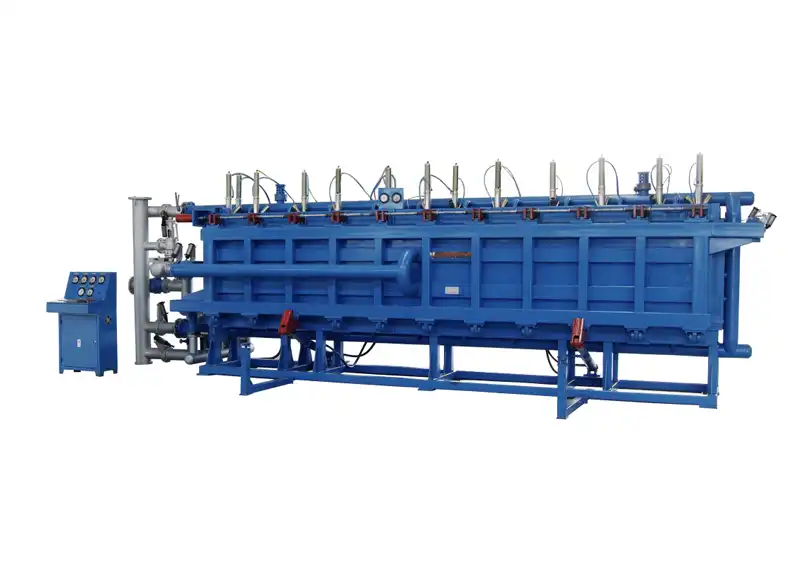
Air cooling employs fans to blow cold air into the mold cavity, carrying away the heat released by EPS beads, thereby achieving cooling.
Advantages:
- Lower equipment cost
- Simple maintenance
- Lower energy consumption
Disadvantages:
- Slower cooling speed, longer production cycle
- Cooling effect is affected by air speed and volume, panel density consistency may be poor
- Finished panels may exhibit slight warping
FAQs about EPS Foam Blocks
What are the benefits of using a fully automatic EPS sandwich panel machine?
- Increased production output
- Improved product quality consistency
- Reduced labor costs
- Enhanced safety through automation
What are the different applications of EPS sandwich panels?
- Construction (walls, roofs, insulation)
- Cold storage facilities and refrigerated trucks (thermal insulation)
- Packaging (lightweight, shock-absorbing, and insulating properties)
How do fully automatic EPS sandwich panel machines work?
- Pre-expanded EPS beads are loaded into the feeding system.
- The forming machine shapes the beads into the desired panel profile.
- The cooling system rapidly cools the formed panel to solidify the bond.
- The hydraulic system powers the various machine functions.
- The weighing system ensures panels meet the specified weight requirements.
What are the five main components of a fully automatic EPS sandwich panel machine?
- Feeding System: Supplies pre-expanded EPS beads.
- Forming Machine: Shapes the EPS beads into the panel profile.
- Cooling System: Cools the formed panel to solidify the bond.
- Hydraulic System: Powers the machine’s operations.
- Weighing System: Ensures panels meet weight specifications.