Have you ever wondered how your favorite plastic water bottle started its life? The answer lies in tiny, hard pellets called plastic granules. These unassuming particles are the foundation of countless plastic products, from packaging to toys to automotive parts. But what exactly are they, and how do they transform into the items we use every day?
In this guide, let’s dive into the world of plastic granules.
What Are Plastic Granules?
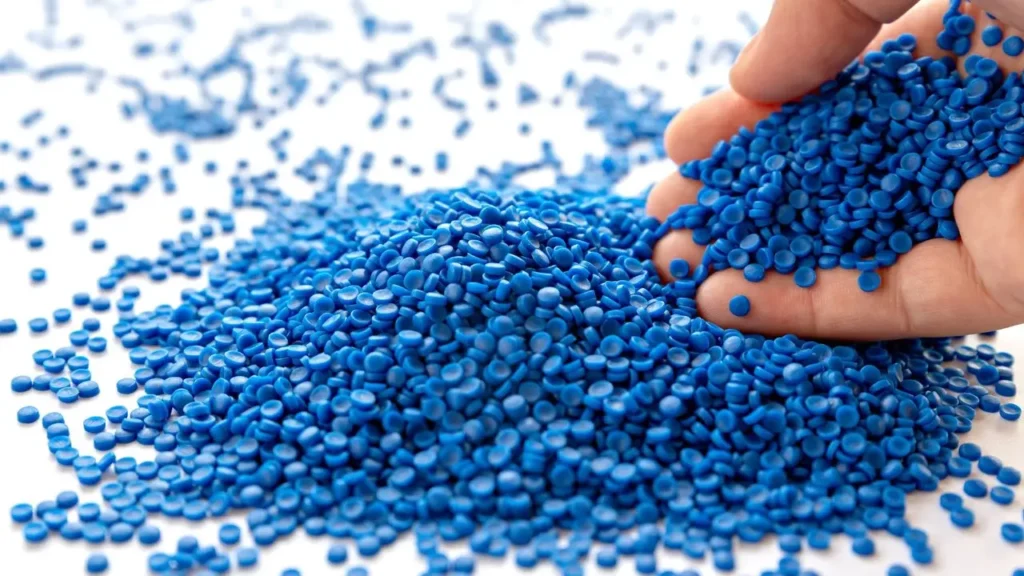
Plastic granules, also known as resin pellets or nurdles, are small, hard particles that serve as the raw material for a vast array of plastic products.
They are typically about the size of a grain of rice and come in various colors and shapes depending on the type of plastic they represent.
These tiny spheres are produced through a chemical process involving polymers, which are large molecules made up of repeating subunits. Once created, plastic granules are transported to manufacturing facilities where they undergo a process of heating, melting, and molding to form the final plastic product.
What are Plastic Granules Used for?
Plastic granules, often referred to as plastic pellets or nurdles, are the building blocks for a vast array of products.
They are tiny, resin-based particles that are melted and molded into various shapes and sizes.
Here are some of the primary uses of plastic granules:
- Packaging: Bottles, containers, bags, films, and other packaging materials.
- Automotive industry: Interior and exterior components, bumpers, dashboards, seats, and more.
- Electronics: Components, casings, and insulation.
- Construction: Pipes, fittings, insulation, and building materials.
- Medical industry: Medical equipment, syringes, containers, and packaging.
- Textiles: Synthetic fibers for clothing and other fabrics.
- Agriculture: Films for greenhouses, irrigation, and silage storage.
- Consumer goods: Toys, household items, appliances, and more.
Essentially, plastic granules are incredibly versatile and form the basis for countless products we use daily.
Would you like to learn more about a specific application or the plastic production process?
How to Make Plastic Granules?
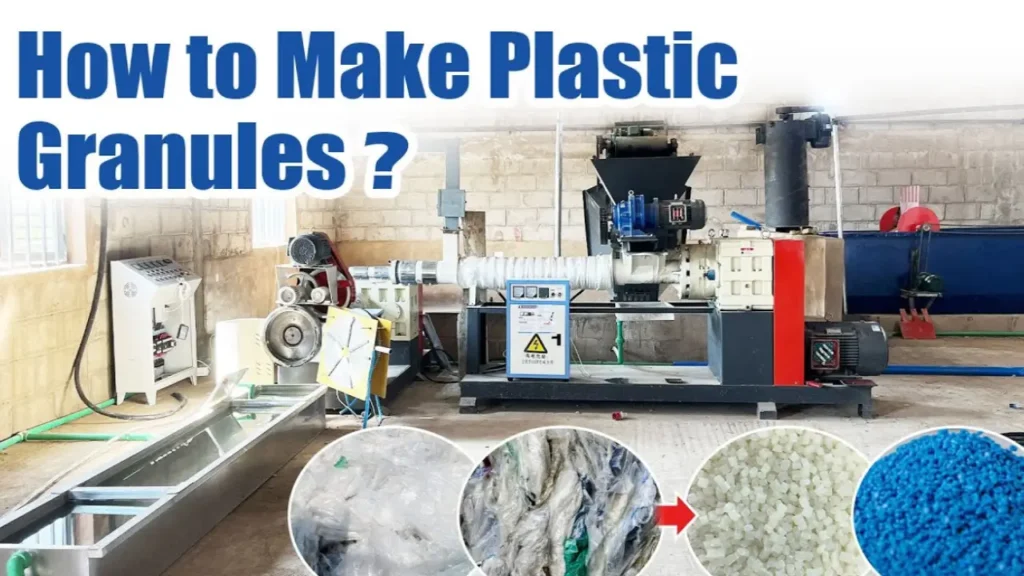
How are plastic granules made?
Plastic granules are typically produced through an industrial process, but it’s possible to understand the general steps involved.
Here’s a simplified step about how to make granules made in the following?
The Process
- Plastic Collection: This involves gathering plastic waste, such as bottles, containers, or other plastic products.
- Sorting and Cleaning: The collected plastic is sorted based on type (e.g., PET, HDPE, PVC) and cleaned to remove impurities like labels, caps, and food residue.
- Shredding: The cleaned plastic is shredded into small pieces to facilitate the melting process.
- Washing: The shredded plastic undergoes a washing process to remove any remaining contaminants.
- Drying: The plastic is dried to remove moisture, which is crucial for the melting process.
- Melting: The dried plastic is melted in an extruder, a machine that uses heat and pressure to liquefy the plastic.
- Pelletizing: The molten plastic is forced through a die with small holes, forming strands that are cut into pellets.
- Cooling: The pellets are cooled to solidify them.
- Packaging: The plastic granules are packaged for storage and transportation.
Important Considerations
- Type of Plastic: Different types of plastic have varying melting points and properties, requiring specific processing conditions.
- Equipment: The production of plastic granules requires specialized machinery, including shredders, washers, extruders, and pelletizers.
- Quality Control: Ensuring the purity and consistency of the plastic granules is essential for their use in manufacturing.
- Environmental Impact: The recycling of plastic into granules helps reduce plastic waste but still requires energy and resources.
It’s important to note that producing plastic granules on a small scale is challenging and might not be economically feasible. The process typically requires industrial-sized equipment and expertise.
How to Make Plastic Granules Using a Plastic Granulator
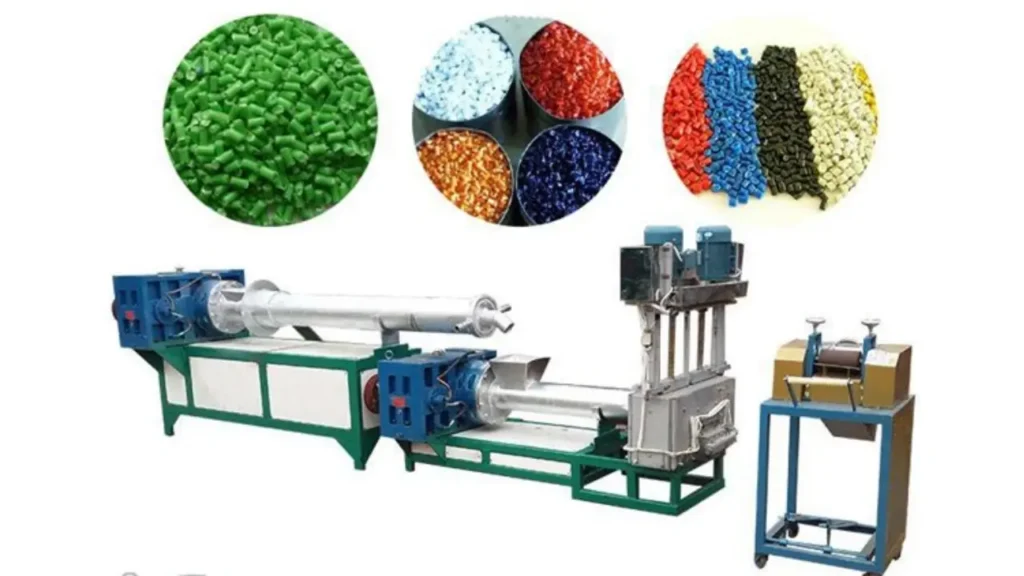
A plastic granulator is a key piece of equipment in the plastic recycling process, but it’s just one part of the overall operation.
The Plastic Granulation Process
- Plastic Collection and Sorting: The process begins with collecting plastic waste. This waste is then sorted based on the type of plastic to ensure compatibility and quality of the recycled product.
- Plastic Cleaning and Shredding: The collected plastic is cleaned to remove impurities, labels, and contaminants. It’s then shredded into smaller pieces.
- Plastic Drying: Moisture can degrade the quality of the recycled plastic, so it’s essential to dry the shredded plastic before granulation.
- Plastic Granulation: This is where the granulator comes in. It melts the plastic and forces it through a die to form strands, which are then cut into small pellets or granules.
- Cooling and Filtration: The granules are cooled to solidify and then filtered to remove any impurities.
The Role of the Plastic Granulator
A plastic granulator essentially melts and cuts plastic into small, uniform pellets. It consists of a hopper to feed the plastic, a heating chamber to melt the material, a die to form the plastic strands, and a cutting mechanism to create the granules.
Different types of granulators exist, including:
- Strand pelletizers: Melt plastic into strands and cut them into pellets.
- Blade granulators: Shear plastic into smaller pieces using blades.
- Crusher granulators: Break down plastic into smaller pieces through crushing.
Additional Considerations
- Plastic Type: Different plastics have varying melting points and processing requirements.
- Granule Size: The desired size of the granules will influence the die and cutting mechanism.
- Energy Efficiency: Modern granulators focus on energy efficiency to reduce operating costs.
- Safety: Proper safety measures must be in place to protect operators and equipment.
While a plastic granulator is a crucial component, the entire recycling process requires careful planning and equipment selection to produce high-quality plastic granules.
Would you like to know more about specific types of plastic granulators or the challenges involved in plastic recycling?
How to Make Biodegradable Plastic Granules?
Creating biodegradable plastic granules on a small scale is challenging and often requires specialized equipment and knowledge. While there are simple experiments to demonstrate the concept of bioplastics, industrial-scale production is a complex process.
General Process Overview:
- Bio-based Material Selection: Typically, materials like cornstarch, plant oils, or other renewable resources serve as the base.
- Polymerization: The selected material undergoes a chemical process to form long chains of molecules (polymers).
- Compounding: Additional ingredients like plasticizers, fillers, and stabilizers might be added to achieve desired properties.
- Extrusion: The compounded material is melted and pushed through a die to form strands.
- Pelletization: The strands are cut into small pellets or granules.
- Cooling and Drying: The granules are cooled and dried to prepare them for further processing.
Key Challenges and Considerations:
- Material Availability: Ensuring a consistent supply of bio-based materials can be challenging.
- Cost-Effectiveness: The production process often requires specialized equipment and can be more expensive than traditional plastics.
- Performance: Biodegradable plastics might not always match the performance of traditional plastics in terms of strength, durability, or flexibility.
- Biodegradability Standards: Different countries have varying standards for biodegradable plastics, which can impact product development.
Research and Development:
The field of biodegradable plastics is rapidly evolving. Many companies and research institutions are working to develop new materials and processes to improve the performance and cost-effectiveness of these products.
While it’s possible to experiment with making small quantities of bioplastics at home, industrial-scale production requires significant investment and expertise.
How Many Types of Plastic Granules Are There?
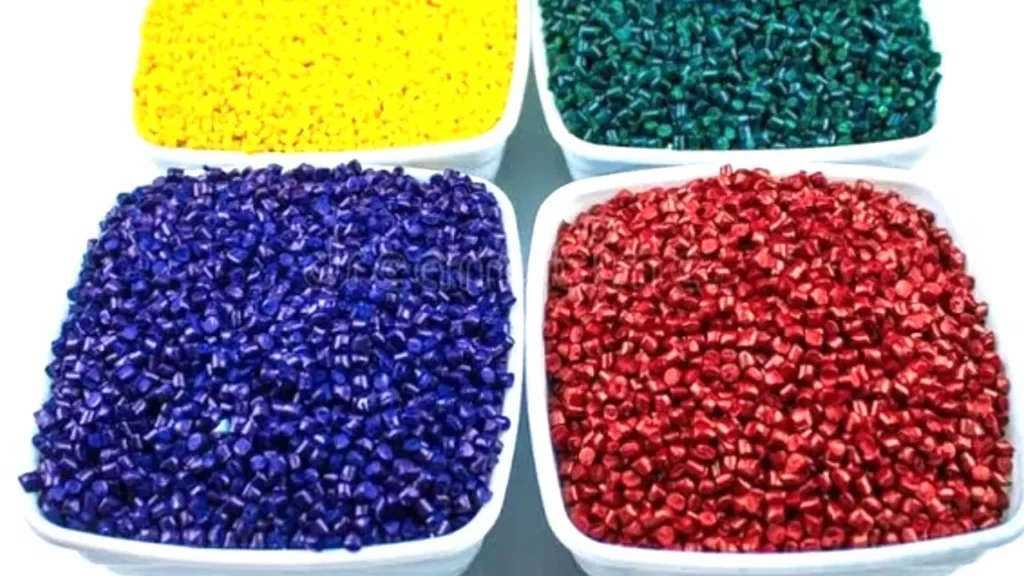
Types of Plastic Granules
There are numerous types of plastic granules, each with unique properties and applications. While the exact number can vary depending on specific classifications and additives, the most common types fall under the following categories:
Based on Resin Type:
- Polyethylene (PE): Includes Low-Density Polyethylene (LDPE), High-Density Polyethylene (HDPE), and Linear Low-Density Polyethylene (LLDPE).
- Polypropylene (PP): Known for its rigidity and heat resistance.
- Polystyrene (PS): Used in packaging, insulation, and consumer products.
- Polyvinyl Chloride (PVC): Versatile plastic used in construction, plumbing, and packaging.
- Polyethylene Terephthalate (PET): Commonly used for beverage bottles and food packaging.
- Acrylonitrile Butadiene Styrene (ABS): Offers a good balance of strength, stiffness, and toughness.
- Nylon (PA): Known for its strength and durability.
- Polycarbonate (PC): Offers high impact resistance and transparency.
Based on Other Characteristics:
- Virgin granules: Produced from raw materials.
- Recycled granules: Produced from recycled plastic waste.
- Color masterbatch: Granules containing pigments for coloring plastics.
- Additive masterbatch: Granules containing additives for specific properties (e.g., flame retardants, UV stabilizers).
It’s important to note that this is not an exhaustive list, and new types of plastic resins are constantly being developed.
Would you like to learn more about a specific type of plastic granule or its applications?
Conclusion
In conclusion, plastic granules, the fundamental building blocks of countless products, play a pivotal role in modern manufacturing. Understanding their properties, production processes, and applications is essential for anyone involved in the plastics industry. From their creation to their transformation into everyday items, plastic granules offer a fascinating glimpse into the world of polymer science.
Are you ready to explore the potential of plastic granules for your business? Contact us today to discuss your specific requirements and receive a customized quote. Our team of experts is eager to assist you in finding the perfect plastic granule solution. Let’s work together to shape the future of plastics!