ICF blocks, or Insulated Concrete Forms, are innovative building materials revolutionizing the construction industry. These blocks combine the strength of concrete with the insulation properties of foam, offering numerous benefits in terms of energy efficiency, durability, and ease of construction.
What Are ICF Blocks?
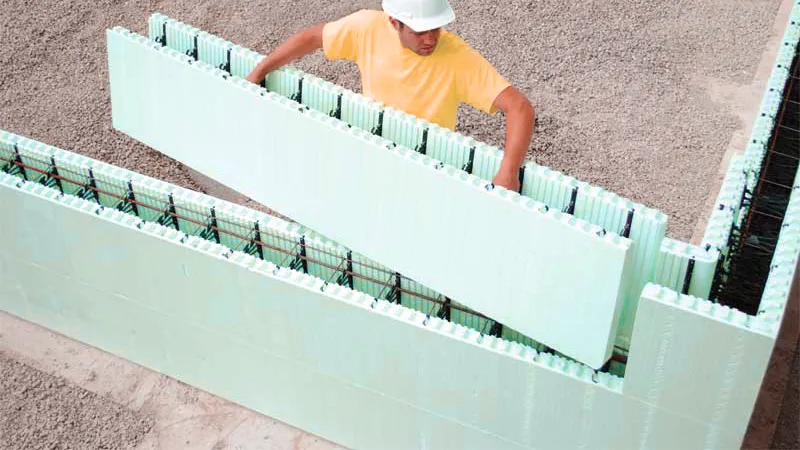
Insulated Concrete Forms (ICF) are hollow foam blocks that are stacked into the shape of the exterior walls of a building, reinforced with steel rebar, and then filled with concrete.
ICF combines one of the finest insulating materials – Expanded Polystyrene (EPS) – with one of the strongest structural building materials – steel-reinforced concrete. The result is a wall system of unmatched comfort, energy efficiency, strength, and noise reduction.
ICF construction provides structural advantages for any building. Insulating concrete forms provide benefits to both builders and building owners alike.
What are ICF Blocks Made of?
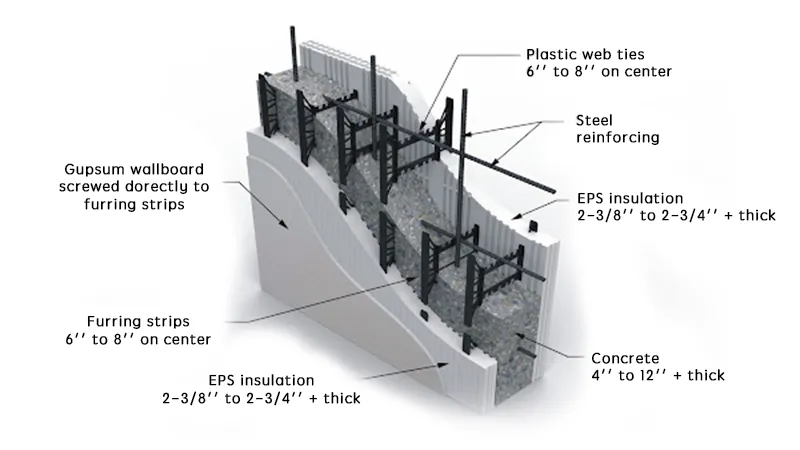
ICF blocks are typically composed of two main components: expanded polystyrene (EPS) foam and reinforced concrete. These materials work in synergy to provide structural integrity, thermal insulation, and soundproofing capabilities to buildings.
Expanded Polystyrene (EPS) Foam
EPS foam is a lightweight, rigid material derived from polystyrene beads that have been expanded and fused.
The foam panels used in ICF blocks are designed with interlocking mechanisms to ensure stability and ease of assembly during construction.
EPS foam is known for its excellent insulation properties, reducing heat transfer and energy consumption for heating and cooling.
Reinforced Concrete
The core of an ICF block is typically filled with reinforced concrete, which provides strength, durability, and stability to the building structure.
Reinforced concrete is made by mixing cement, aggregates (such as sand and gravel), water, and reinforcing materials such as steel bars or fibers.
The combination of EPS foam and reinforced concrete creates a composite material that offers the benefits of both insulation and structural support.
The Manufacturing Process of ICF Blocks
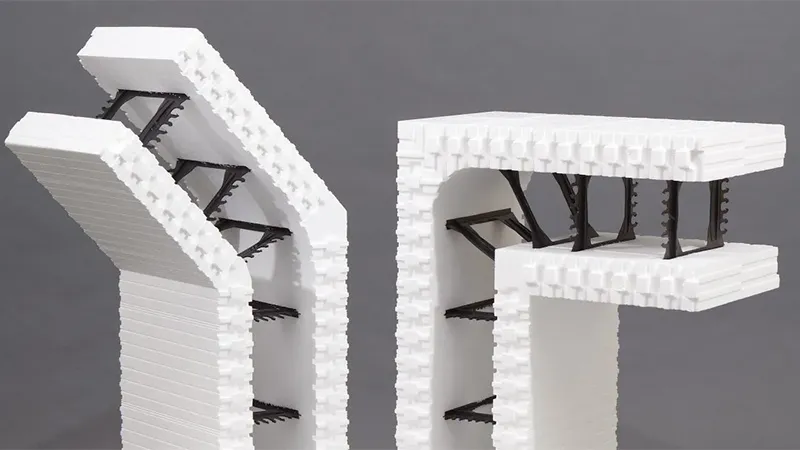
EPS Foam Production: Polystyrene beads are expanded using steam to create EPS foam blocks of varying densities. These foam blocks are then shaped and molded to the desired dimensions for ICF blocks.
Assembly of ICF Blocks: The EPS foam panels are assembled with precision to form the walls of ICF blocks. Interlocking mechanisms and grooves are incorporated into the panels to facilitate easy stacking and alignment during construction.
Reinforced Concrete Core: Once the EPS foam panels are assembled, the core of the ICF blocks is filled with reinforced concrete. The concrete mixture is poured into the hollow core of the blocks, encapsulating the EPS foam and creating a solid, reinforced structure.
Curing and Finishing: After the concrete has been poured, the ICF blocks undergo a curing process to allow the concrete to harden and gain strength. Once cured, the blocks can be finished with additional treatments or coatings as needed for aesthetic or functional purposes.
What is The Cost of ICF Blocks?
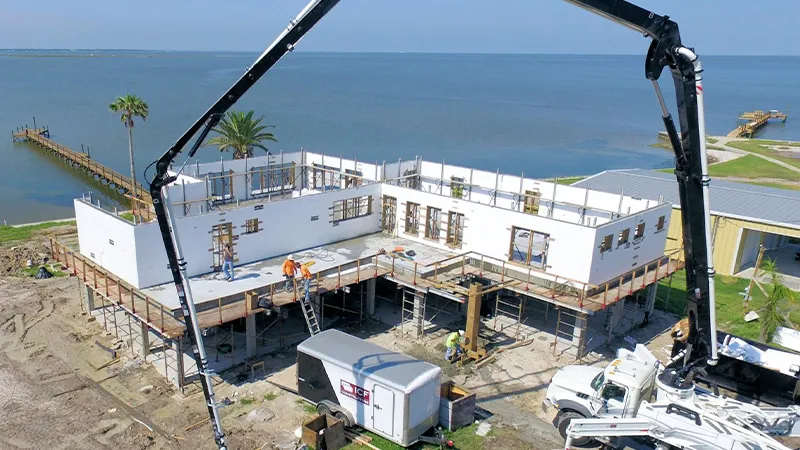
The cost of ICF blocks can vary depending on several factors such as the brand, quality, thickness, and local market conditions. On average, the cost of ICF blocks ranges from $10 to $20 per square foot of wall area, including materials and labor.
Factors Influencing Cost:
- Type and Brand: Different manufacturers offer ICF blocks with varying features, quality standards, and pricing. Higher-end brands may cost more but often come with additional benefits such as better insulation properties or ease of installation.
- Thickness: The thickness of the ICF blocks can affect their cost. Thicker blocks provide higher insulation levels but may be more expensive compared to thinner blocks.
- Quality of Materials: The quality of EPS foam and reinforced concrete used in the ICF blocks can influence their cost. High-quality materials may have a higher upfront cost but can result in long-term savings through energy efficiency and durability.
- Local Market: Regional factors such as supply and demand, labor costs, and transportation expenses can impact the overall cost of ICF blocks. Prices may vary from one location to another.
- Installation Costs: In addition to the cost of the blocks themselves, labor and installation charges can contribute significantly to the total cost of using ICF blocks. Factors such as complexity of design, site conditions, and contractor rates can affect installation costs.
Benefits of Cost Consideration:
- Energy Savings: Despite the initial investment, ICF blocks can lead to long-term cost savings through reduced energy consumption for heating and cooling. Their high insulation properties help maintain indoor comfort levels with less reliance on HVAC systems.
- Durability and Maintenance: The durability of ICF buildings can result in lower maintenance and repair costs over time compared to traditional construction methods. ICF structures are resistant to pests, mold, and moisture damage, reducing the need for frequent repairs.
- Insurance Savings: Some insurance companies offer discounts for buildings constructed with ICF blocks due to their resilience against fire, storms, and other hazards. These potential savings should be factored into the overall cost analysis.
- Long-Term Value: Investing in high-quality ICF blocks can enhance the resale value of a property. Buyers often appreciate the energy efficiency, durability, and comfort benefits associated with ICF construction, which can translate into higher property value.
Why Build With ICF Blocks?
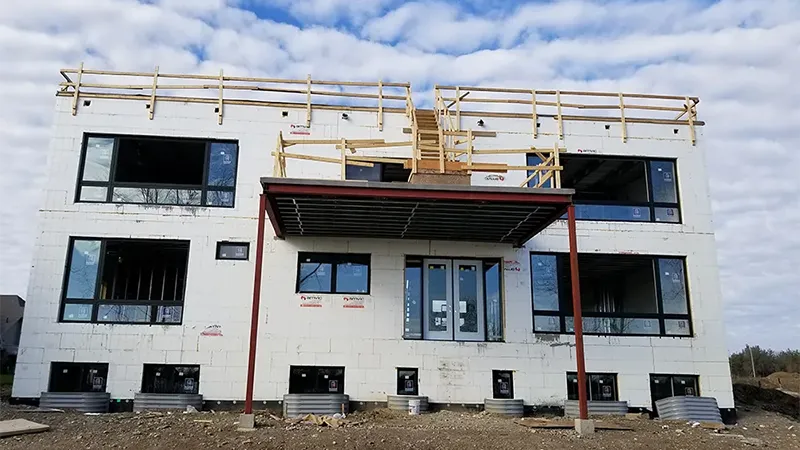
Building with ICF blocks offers several compelling reasons that make them a preferred choice for many construction projects:
- Energy Efficiency: ICF blocks provide superior insulation compared to traditional building materials, reducing energy consumption for heating and cooling. This leads to lower utility bills and a more comfortable indoor environment year-round.
- Durability: The combination of reinforced concrete and EPS foam in ICF blocks creates a strong and durable building structure. ICF buildings are resistant to fire, pests, mold, and moisture, resulting in reduced maintenance costs and longer lifespan.
- Soundproofing: ICF blocks offer excellent soundproofing capabilities, creating quieter indoor spaces by reducing external noise transmission. This is particularly beneficial for residential, commercial, and industrial buildings located in noisy environments.
- Speed of Construction: ICF blocks are easy to assemble and install, leading to faster construction times compared to traditional building methods. The interlocking design and lightweight nature of the blocks simplify the construction process, saving time and labor costs.
- Environmental Sustainability: Using ICF blocks promotes sustainable construction practices. The recyclable nature of EPS foam reduces waste, while the energy-saving properties contribute to lower greenhouse gas emissions and environmental impact.
- Resilience: ICF buildings are highly resilient against extreme weather conditions such as hurricanes, earthquakes, and storms. The structural integrity of ICF blocks makes them a reliable choice for regions prone to natural disasters.
- Cost Savings: While the initial cost of ICF blocks may be higher than traditional materials, the long-term savings in energy costs, maintenance, insurance premiums, and potential resale value can outweigh the upfront investment.
- Versatility: ICF blocks can be used in various types of construction, including residential homes, commercial buildings, industrial facilities, and multi-story structures. They are suitable for walls, foundations, and even roofs, offering versatility and flexibility in design.
- Health and Comfort: The thermal insulation properties of ICF blocks help maintain consistent indoor temperatures, improving comfort levels for occupants. Additionally, the absence of air leaks and drafts enhances indoor air quality, promoting a healthier living or working environment.
How Long Does ICF Blocks Last?
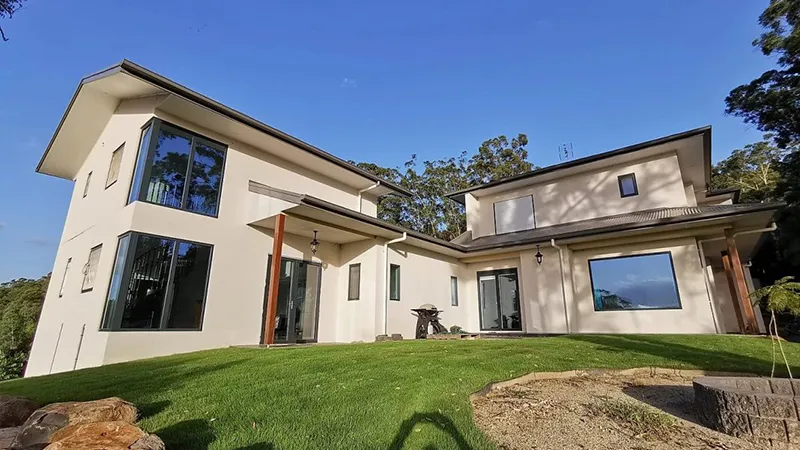
ICF blocks are known for their durability and longevity, with a typical lifespan of 50 to 100 years or more.
Factors that contribute to the longevity of ICF blocks include the quality of materials used, proper installation, and regular maintenance.
Reinforced concrete, a key component of ICF blocks, is renowned for its durability and ability to withstand environmental factors such as moisture, pests, fire, and structural loads. The EPS foam insulation within ICF blocks is also designed to withstand the test of time, especially when protected from direct sunlight and physical damage.
With proper care and maintenance, such as periodic inspections for cracks or damage and addressing any issues promptly, ICF buildings can maintain their structural integrity and performance for decades, providing a long-lasting and reliable construction solution.
Conclusion
ICF blocks offer a myriad of benefits that make them a highly desirable choice for modern construction projects. Their combination of energy efficiency, durability, soundproofing, ease of construction, environmental sustainability, resilience, and long-term cost savings sets them apart as a superior building material.
Additionally, with proper care and maintenance, ICF buildings can last for several decades, providing a reliable and comfortable living or working environment for occupants.
Overall, the advantages of building with ICF blocks make them a smart investment for builders, homeowners, and property developers looking to create efficient, durable, and sustainable structures.