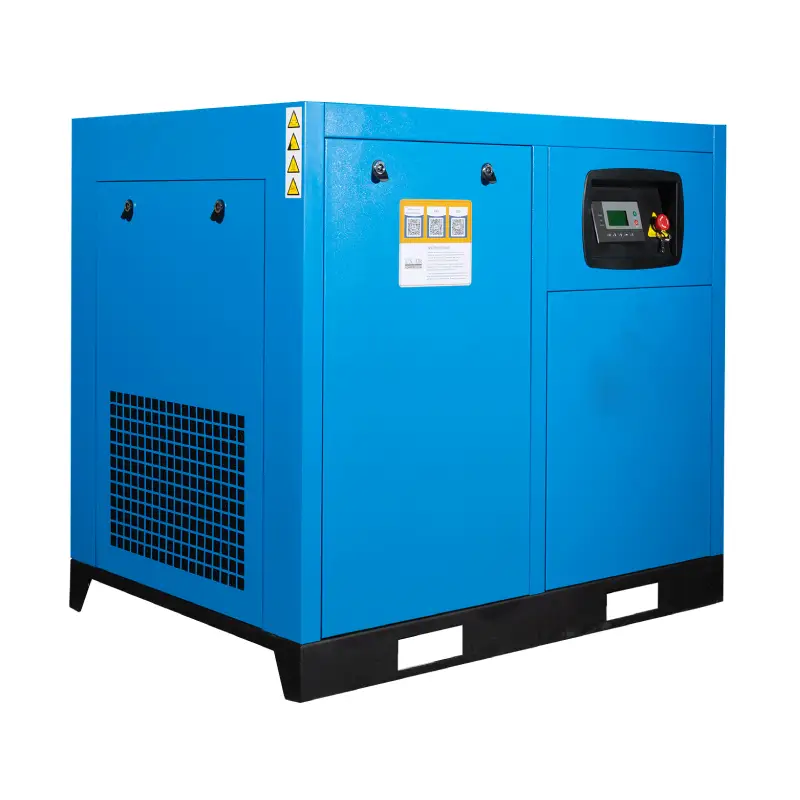
Is your current air compressor system a drag on your productivity? Rotary screw air compressors can be the game-changer your industrial operation needs.
Rotary Screw Air Compressor
Boost Efficiency, Slash Costs
Rotary screw compressors are renowned for their ability to deliver exceptional compressed air output while consuming less energy. This translates to significant savings on your electricity bills, putting more money back in your pocket.
Unmatched Reliability
Built with robustness in mind, rotary screw compressors are designed for continuous operation. They can handle the demanding workloads of industrial environments without breaking a sweat, ensuring your production lines keep humming.
Minimize Downtime, Maximize Profits
With fewer moving parts compared to other compressor types, rotary screw models require less frequent maintenance. This translates to less downtime for your equipment, keeping your operation running smoothly and maximizing your profitability.
Consistent Air Quality
Rotary screw compressors deliver a steady flow of clean, dry air, crucial for powering sensitive pneumatic tools and processes. This reduces the risk of contamination and ensures optimal performance from your equipment.
rotary screw air compressor Applications
Rotary Screw Air Compressors for Manufacturing
Rotary screw air compressors are the workhorses of many manufacturing facilities. Their ability to deliver a continuous stream of high-pressure air makes them ideal for powering a wide range of pneumatic tools and equipment that keep production lines running smoothly. Here are some specific examples:
Assembly Line Efficiency: Imagine a car assembly line. Rotary screw compressors provide the muscle behind the screwdrivers, nut drivers, and riveters that efficiently assemble vehicles.
Precision Finishing: Sanding, grinding, and buffing tools used for shaping and smoothing manufactured goods rely on the steady flow of compressed air from rotary screw compressors to achieve a flawless finish.
A Picture-Perfect Paint Job: In paint booths, rotary screw compressors ensure a consistent supply of air for spray guns, guaranteeing a smooth, professional-looking finish on everything from cars to furniture.
Precise Plastic Molding: The high-pressure air generated by rotary screw compressors is critical for operating plastic molding machines. These machines use compressed air to force molten plastic into molds to create various shapes. Consistent air pressure ensures precise molding and quality products.
Rotary Screw Air Compressors for Automotive Applications
The automotive industry relies heavily on rotary screw air compressors to keep vehicles moving through the repair and production processes. Here’s a look at some key applications:
Tire Inflation Done Right: From ensuring proper tire pressure on everyday vehicles to racing cars, rotary screw compressors provide the reliable air source needed for fast and accurate tire inflation.
A Flawless Finish Every Time: Body shops and paint booths depend on rotary screw compressors to deliver a consistent stream of air for spray guns. This ensures an even application of paint for a perfect, long-lasting finish.
Body Shop Muscle: A variety of pneumatic tools used in body shops, such as sanders, drills, and grinders, rely on the power of rotary screw compressors to operate efficiently.
Rotary Screw Air Compressors for Construction
Construction sites are another domain where rotary screw air compressors play a vital role. Their ability to withstand demanding conditions and deliver reliable power makes them essential for operating a variety of heavy-duty equipment:
Jackhammers: Breaking up tough concrete and asphalt is no sweat for jackhammers powered by rotary screw compressors. The steady flow of compressed air provides the necessary force to break through even the most stubborn surfaces.
Impact Wrenches: Tightening and loosening nuts and bolts on construction equipment is a breeze with impact wrenches driven by rotary screw compressors. These powerful tools deliver the necessary torque quickly and efficiently.
Pavement Breakers: Ripping up old roads and sidewalks requires serious muscle. Rotary screw compressors provide the air power needed for pavement breakers to make short work of tough jobs.
Sandblasters: Cleaning and preparing surfaces for new construction or coatings often involves sandblasting. Rotary screw compressors ensure a consistent flow of abrasive material for effective cleaning.
Rotary Screw Air Compressors for Food and Beverage Production Flowing
Rotary screw air compressors play a crucial role in ensuring the smooth operation of food and beverage production facilities. Their ability to deliver clean, dry air is essential for various processes:
Bottling and Canning Lines: From conveying empty bottles and cans to operating filling and capping machines, rotary screw compressors provide the clean, dry air required throughout the bottling and canning process.
Efficient Conveying: Manufacturing facilities rely on conveyor belts to move products throughout the production process. Rotary screw compressors ensure a steady supply of air to operate these conveyor systems efficiently.
Precise Mixing and Blending: Many food and beverage products require accurate mixing and blending of ingredients. Rotary screw compressors provide the clean air needed to operate pneumatic mixing equipment.
FAQs about rotary screw air compressor
what is rotary screw air compressor
A rotary screw air compressor is a type of industrial air compressor that uses a rotating screw mechanism to compress air. They are known for their efficiency, reliability, and ability to deliver a continuous flow of compressed air. This makes them ideal for a wide range of industrial applications such as:
- Manufacturing
- Construction
- Automotive
- Food and Beverage Production
how a rotary screw air compressor works
- Intake: The compressor sucks in air through an inlet valve.
- Compression: Two intermeshing helical rotors trap air and continuously squeeze it as they rotate, reducing its volume and increasing the pressure.
- Injection (Oil-injected models only): In oil-injected models, oil is injected into the chamber for lubrication and cooling during compression.
- Separation (Oil-injected models only): The oil is then separated from the compressed air before it exits the system.
- Discharge: The compressed air is discharged from the chamber and into a storage tank, or directly used for various applications.