In the realm of construction and engineering, the concept of lightweight fill plays a crucial role in achieving structural stability and efficiency. Lightweight fill is a material used to fill voids or support structures requiring minimal weight without compromising strength or durability. This material is often selected based on its ability to provide adequate support while reducing the overall load on the underlying substrate or foundation.
Understanding the characteristics, applications, and benefits of lightweight fill is essential for engineers, architects, and builders alike, as it contributes significantly to the sustainable and efficient construction practices of today. This article explores the various types of lightweight fill, their uses in different construction scenarios, and the advantages they offer in enhancing project performance and longevity.
What Is A Lightweight Fill?
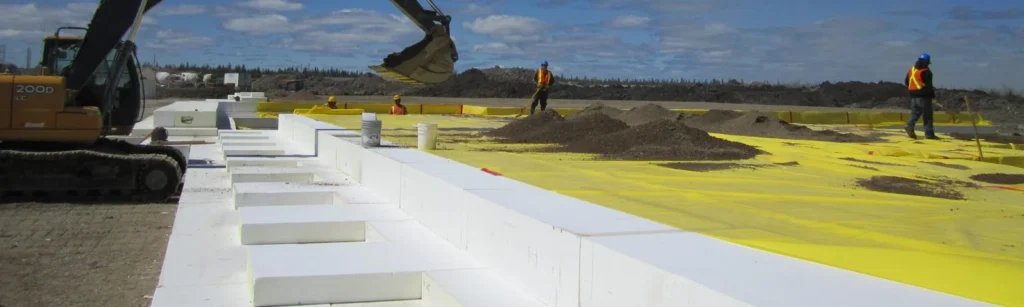
A lightweight fill is a construction material specifically chosen for its ability to fill voids or provide structural support while minimizing overall weight. This characteristic not only reduces the load on foundations and substrates but also promotes sustainable building practices.
Engineers and builders select lightweight fill based on its favorable strength-to-weight ratio, ensuring both durability and structural integrity are maintained throughout the project lifecycle. This makes lightweight fill an essential component in modern construction methods aiming to optimize efficiency and longevity.
Types Of Lightweight Fill
You’ll encounter three main categories of low-density fills in construction:
Cementitious
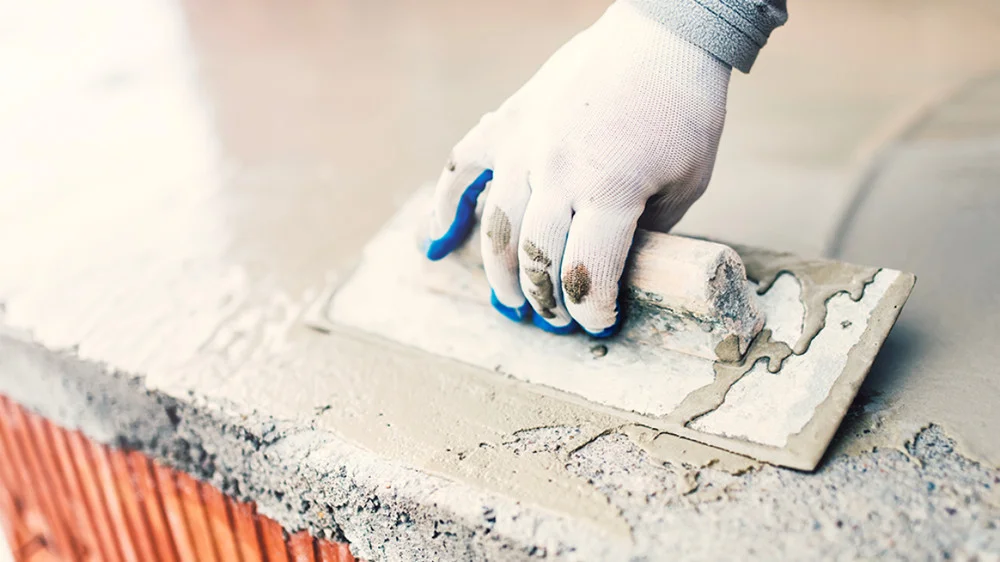
Cementitious materials encompass a diverse range of substances crucial to construction, with cellular concrete and lightweight aggregate concrete standing out as notable innovations in the field. Cellular concrete, a type of cementitious material, is renowned for its unique composition of Portland cement, water, and air bubbles or foam.
This lightweight yet sturdy material is achieved through a precise blending process that introduces air or foam into the mixture, reducing its density while maintaining structural integrity. Cellular concrete finds extensive use in construction due to its exceptional thermal insulation properties, fire resistance, and ability to be easily pumped or poured into place.
Applications range from filling voids and stabilizing slopes to insulating roofs and constructing lightweight floors. Lightweight aggregate concrete, another key cementitious variant, incorporates lightweight aggregates such as expanded shale, expanded clay, or lightweight volcanic materials.
These aggregates are characterized by their low density and high strength-to-weight ratio, making them ideal for applications where reducing overall structural load is critical. Lightweight aggregate concrete offers enhanced durability, thermal insulation, and acoustic properties compared to traditional concrete, making it suitable for various construction projects ranging from residential buildings to infrastructure and industrial facilities.
Plastics
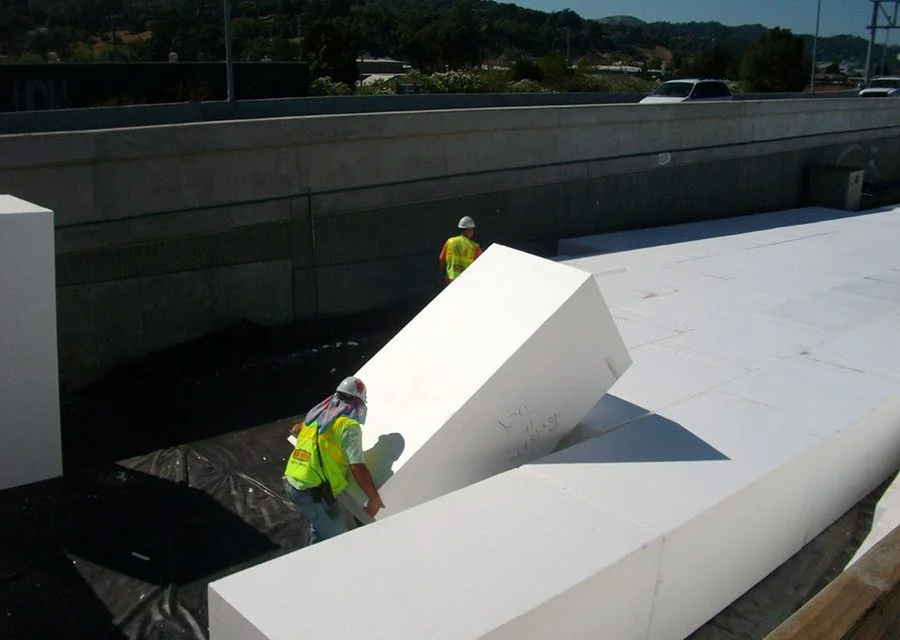
Plastics encompass a diverse range of materials utilized across numerous industries, including construction, packaging, automotive, and electronics. This category includes high-density polyurethanes (HDPU) and expanded polystyrenes (EPS), each serving distinct roles based on their properties and applications.
High-density polyurethanes (HDPU) are known for their exceptional durability and versatility. They are widely used in construction as insulation materials, in marine applications for buoyancy and structural reinforcement, and in industrial settings for thermal and acoustic insulation. HDPU can be formulated to achieve varying densities and strengths, making them suitable for both lightweight filling and heavy-duty structural support.
Expanded polystyrenes (EPS), on the other hand, are lightweight and rigid foams derived from styrene monomer. They are renowned for their excellent thermal insulation properties and are commonly used in building construction, packaging, and as protective materials in the transportation of fragile goods. EPS offers superior shock absorption capabilities and moisture resistance, making it ideal for applications where maintaining structural integrity and thermal efficiency are paramount.
In construction, both HDPU and EPS play pivotal roles in enhancing energy efficiency, structural integrity, and sustainability. HDPU’s ability to support heavy loads with minimal weight makes it an ideal choice for infrastructure projects requiring strong yet lightweight materials. EPS, with its superior insulation properties, contributes to reducing heating and cooling costs in buildings while minimizing environmental impact.
Aggregates
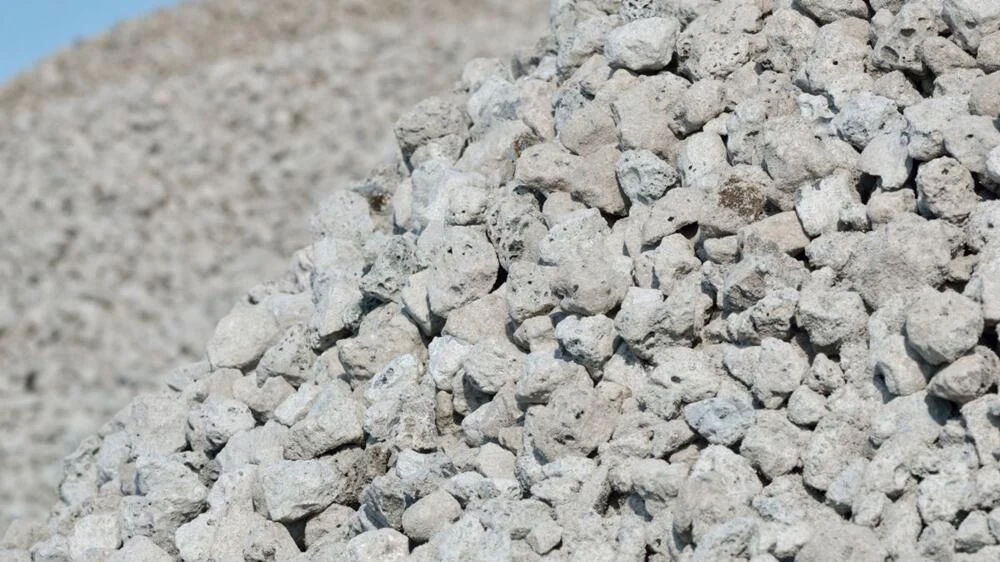
Aggregates are essential components in construction, with foamed glass, expanded shale, and expanded clay representing innovative options known for their unique properties and versatile applications.
Foamed glass aggregates are lightweight and made from recycled glass, processed to form porous, durable particles. They excel in thermal insulation, fire resistance, and resistance to moisture and chemicals. Common uses include lightweight concrete production, insulation fills, and drainage applications due to their structural stability and environmental benefits.
Expanded shale aggregates are produced by expanding natural shale rock at high temperatures, resulting in lightweight, porous particles with excellent durability and resistance to frost and chemicals. These aggregates are favored for structural fills, lightweight concrete, green roofs, and landscaping projects where drainage and soil improvement are essential.
Expanded clay aggregates are lightweight ceramic particles formed by expanding clay at high temperatures. They offer high compressive strength, low water absorption, and superior thermal and acoustic insulation properties. Expanded clay is used in lightweight concrete, insulation fills, and as a growing medium in agriculture and horticulture, providing optimal conditions for plant growth.
What Is Lightweight Fill Used For?
Axial Load Reduction
In construction scenarios where reducing axial loads is crucial, lightweight fill emerges as a pivotal solution. This material effectively minimizes the burden of dead loads on both compressible soils and the structures beneath them. It proves especially advantageous when building on sites with compressible soils, where traditional heavy materials might exacerbate settlement issues.
Moreover, lightweight fill is ideal for applications involving infrastructure such as pipes, tunnels, and basements, where minimizing additional weight is essential for long-term stability and structural integrity. By opting for lightweight fill, builders can successfully manage heavy loads without compromising the safety or longevity of the construction project.
Lateral Load Reduction
In applications aimed at reducing lateral loads, lightweight fill offers a cost-effective solution for minimizing the stress on walls and structures, thereby enabling more economical construction practices. For instance, filling the space between a permanent slope and a wall with CJFill-Ultra Lightweight cellular concrete at 25 pounds per cubic foot effectively eliminates passive earth pressure shortly after the material sets, typically within a few hours.
Utilizing low-density fills presents an economical approach to alleviating or compensating for structural loads. This strategy allows for smaller foundation footprints, reduces anticipated settlements, and avoids the expense associated with deep foundations.
Cellular concrete, a lightweight backfill commonly used behind MSE walls, helps mitigate settlement issues in bridge approach areas. Previous cellular concrete is employed to reduce the load on retaining walls by facilitating unrestricted water drainage and preventing the buildup of hydrostatic pressure.
In building construction, a common practice involves excavating and filling unsuitable soils with stone or flowable fill. Cellular concrete can enhance this method by further reducing loads on problematic soils while maintaining sufficient strength to support structural loads.
With the increasing utilization of less ideal urban land, which was previously undeveloped due to extensive geotechnical challenges, lightweight fill emerges as a viable and economical alternative to deep foundations in such settings. This approach not only optimizes construction costs but also maximizes land usage efficiency in urbanized areas.
Benefits Of Lightweight Filling Material
Reduced Structural Load
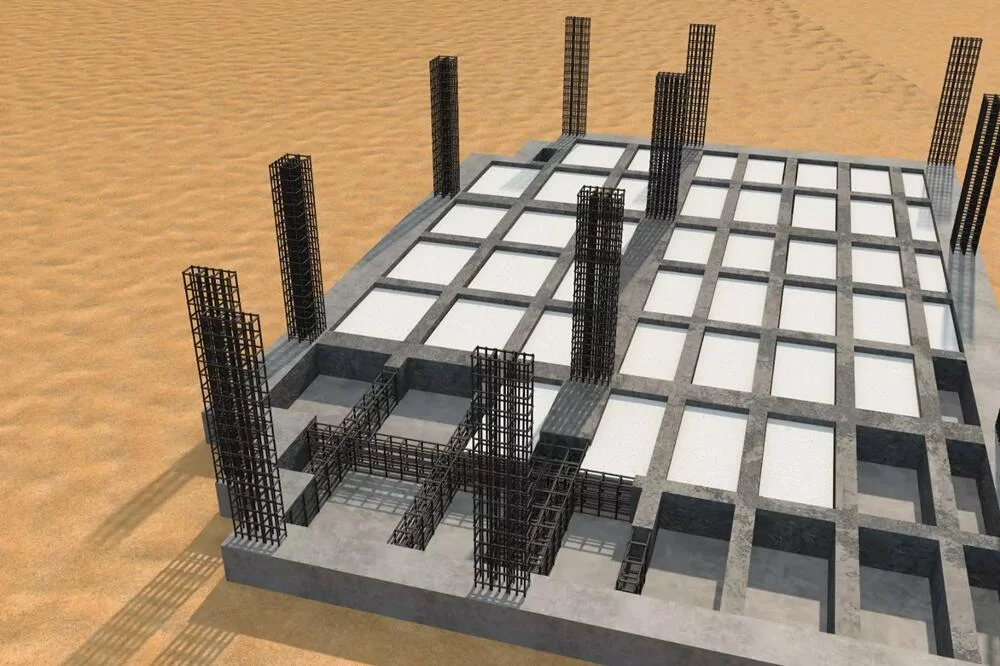
Lightweight fill materials, such as cellular concrete and geotechnical polyurethanes, significantly decrease the weight applied to underlying soils and structures. This reduction helps prevent excessive settlement and reduces the need for extensive foundation systems, thereby cutting overall construction costs.
Enhanced Construction Efficiency
Compared to traditional heavy materials, lightweight fills like cellular concrete and geotechnical polyurethanes are easier to transport, handle, and install. This ease of use translates into faster project completion times and reduced labor costs, improving overall construction efficiency.
Improved Thermal and Acoustic Insulation
Materials such as foamed glass and expanded polystyrene aggregates offer excellent thermal and acoustic insulation properties. They contribute to regulating indoor temperatures, reducing energy consumption, and enhancing occupant comfort in buildings.
Environmental Sustainability
Many lightweight fill materials are derived from recycled or sustainable sources, promoting green building practices. By reducing excavation needs and lowering carbon footprints during transportation, these materials minimize environmental impact and support sustainable construction practices.
Versatile Applications
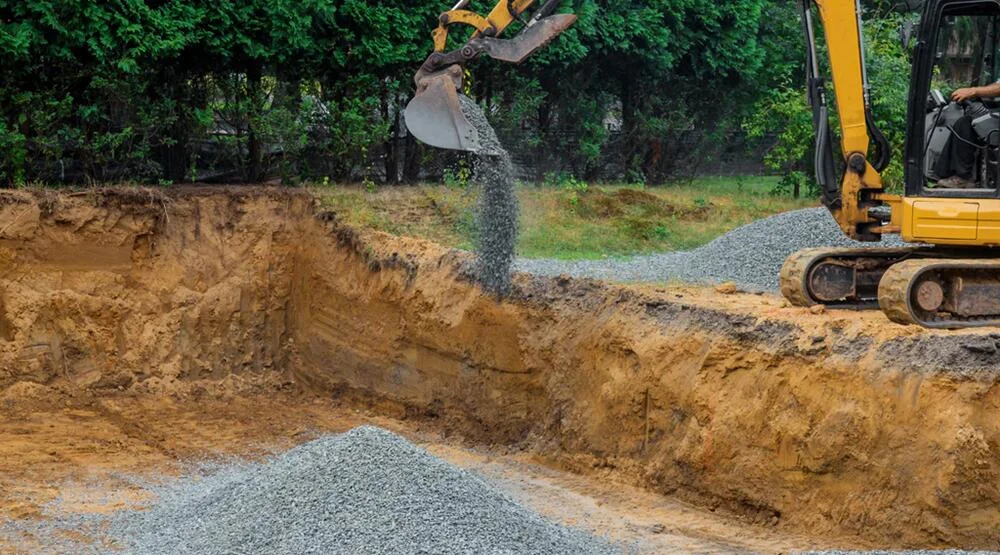
Lightweight fill can be customized to meet specific project requirements across various applications. Whether for backfilling around utilities, filling voids in road construction, or supporting sensitive infrastructure like pipelines and underground structures, lightweight fills offer versatile solutions.
Cost-effective Solutions
Cost-effective solutions are a hallmark of lightweight fills, minimizing excavation volumes and reducing the necessity for extensive foundation systems. This optimization of construction budgets ensures affordability without compromising structural integrity.
Limitations Of Lightweight Fill
Lightweight fills like Ultra Lightweight cellular concrete and geotechnical polyurethanes are typically unsuitable for distributing loads in applications such as footing construction or traffic-bearing surfaces like roads, parking lots, or sidewalks. When lightweight fills weigh less than 63 pounds per cubic foot, they tend to float.
Therefore, careful consideration is necessary during the design phase to ensure that the weight of the structure resting on the lightweight fill exceeds its buoyancy. One effective method to mitigate buoyancy is through the use of previous cellular concrete. This specialized material allows water to permeate through its matrix without causing flotation, facilitating drainage as water levels fluctuate.
However, saturated pervious cellular concrete can increase the loads on underlying soils or structures. Therefore, managing water infiltration and drainage effectively is crucial to maintaining the stability and performance of lightweight fills in various construction applications.
Conclusion
In conclusion, exploring lightweight fill reveals a versatile and advantageous solution in modern construction and infrastructure projects. By understanding its various types, including geofoam, foamed concrete, and recycled materials, as well as its wide-ranging uses from reducing structural loads to enhancing thermal insulation, stakeholders can capitalize on its benefits.
Lightweight fill not only offers cost-effective alternatives by minimizing excavation and construction time but also supports sustainable building practices. Its ability to mitigate settlement risks and improve overall construction efficiency underscores its significance in addressing engineering challenges.
As advancements continue in material science and construction methodologies, the role of lightweight fill is expected to expand, contributing further to resilient and efficient infrastructure development globally.
FAQ
1, What are the common types of lightweight fill?
Common types include geofoam (EPS), foamed concrete, expanded polystyrene, and recycled materials such as industrial waste or organic substances like wood chips.
2, How is lightweight fill installed?
Installation methods depend on the type of material used. Geofoam and foamed concrete, for example, are often delivered in blocks or as a liquid mixture that expands on-site. They are cut or shaped to fit specific project requirements and can be installed efficiently.
3, Is lightweight fill durable?
When properly designed and installed, lightweight fill materials exhibit durability and long-lasting performance. They are resistant to moisture, chemicals, and biological degradation, ensuring stability over the project’s lifespan.
4, What considerations are important when choosing lightweight fill?
Project-specific requirements such as load-bearing capacity and thermal insulation needs.
Environmental factors such as site conditions and sustainability goals.
Regulatory compliance with building codes and standards.
Cost-effectiveness and overall project budget.
5, Can lightweight fill be used in all construction projects?
Lightweight fill is suitable for many construction projects, but its suitability depends on project-specific factors such as soil conditions, structural requirements, and environmental considerations. Consulting with a qualified engineer or construction professional is recommended to determine the best material for each application.
6, Where can I get more information about using lightweight fill in my project?
For more information about using lightweight fill-in construction projects, including specific applications and technical details, contact a qualified construction materials supplier or consult with an experienced engineer or architect specializing in sustainable building practices.
7, How does lightweight fill contribute to sustainable construction practices?
Using recycled materials or environmentally friendly substances.
Reducing excavation needs and minimizing carbon footprints during transportation.
Enhancing energy efficiency in buildings by providing superior thermal insulation.