Compressed air is a versatile and widely-used form of energy, powering a variety of tools, equipment, and industrial processes. Compressing air into a tank allows for the storage and on-demand use of this valuable resource.
In this comprehensive guide, we will explore the principles of air compression, the selection of the right air compressor, the preparation and filling of the compressed air tank, as well as essential maintenance and safety considerations. By the end of this article, you will have a thorough understanding of how to effectively compress air into a tank and ensure its safe and efficient operation.
What is Air Compression?
Air compression is the process of taking ambient air and reducing its volume by applying pressure, which forces the air molecules into a smaller space. This increases the density, pressure, and temperature of the air, effectively storing energy within it.
Think of it like blowing up a balloon: you’re forcing more air into a confined space, increasing the pressure inside the balloon. When you release the balloon, the compressed air escapes, converting that stored potential energy into kinetic energy (making the balloon fly around).
In a mechanical sense, an air compressor is a device that converts power (from an electric motor, gasoline engine, etc.) into potential energy stored in pressurized air. It achieves this by drawing in air and then, through various mechanisms (like pistons or rotating screws), squeezing it into a smaller volume. This pressurized air is then typically stored in a tank for later use, where it can power tools, machinery, or other applications.
What is Air Compression Tank?
An air compression tank, also known as an air receiver tank, is a crucial component of a compressed air system that stores pressurized air after it’s generated by an air compressor. Its primary function is to provide a reservoir of readily available compressed air, acting as a buffer that helps to stabilize pressure fluctuations and reduce the frequency of the compressor cycling on and off.
This not only ensures a steady supply of air for tools and equipment, especially during peak demand, but also extends the lifespan of the compressor by minimizing wear and tear. Additionally, air tanks aid in cooling the compressed air, allowing moisture and other contaminants to condense and be drained, thereby improving air quality and protecting downstream equipment.
Air Compression Working Principle
Air compression fundamentally works on the principle of reducing the volume of a gas, which in turn increases its pressure and temperature. This concept is best understood through Boyle’s Law, which states that for a fixed amount of gas at a constant temperature, the pressure and volume are inversely proportional.
In an air compressor, mechanical energy (typically from an electric motor or gasoline engine) is converted into potential energy stored in the pressurized air. This is achieved by drawing in ambient air and then physically confining it within a smaller and smaller space, forcing the air molecules closer together.
There are two main categories of air compressors based on their working principle: positive displacement and dynamic displacement. Positive displacement compressors, such as reciprocating (piston) compressors and rotary screw compressors, operate by trapping a fixed volume of air and then mechanically reducing that volume.
For example, in a piston compressor, a piston moves within a cylinder, drawing in air on one stroke and then compressing it on the return stroke. Dynamic compressors, like centrifugal and axial compressors, work differently by accelerating the air to a high velocity using rapidly rotating blades (impellers) and then converting that kinetic energy into pressure by slowing down the airflow in a diffuser.
How to Compress Air Into a Tank?
Compressing air into a tank involves a systematic process to safely and efficiently store pressurized air for various applications. Understanding each step ensures proper operation and prevents potential hazards.
Step 1: Prepare the Air Compressor
Before starting, ensure your air compressor is in good working order and placed on a stable, level surface. Check the oil level in oil-lubricated compressors and ensure all connections, including hoses and fittings, are secure and free of leaks. This preparation is crucial for safe and efficient operation.
Make sure the power source is compatible and safely connected. For electric compressors, plug it into the correct outlet; for gas-powered units, ensure you have sufficient fuel. This initial setup prevents operational issues and ensures the compressor functions as intended, ready for the compression process.
Step 2: Connect Air Tools (If Applicable) and Open Tank Valve
If you plan to use air tools, connect them securely to the air hose and ensure all connections are tight. Then, locate the valve on your air tank and open it fully. This allows the compressed air to flow freely into the tank once the compressor starts, preventing pressure buildup in the compressor itself.
Ensure the tank valve is completely open to facilitate efficient air transfer from the compressor to the tank. A partially closed valve can restrict airflow, making the compressor work harder and potentially leading to overheating. Properly opening the valve is key for smooth operation.
Step 3: Start the Air Compressor
With all preparations complete, it’s time to start the air compressor. Locate the power switch or pull cord (for gas models) and activate the unit. The compressor will begin drawing in ambient air and compressing it, sending it towards the storage tank.
Monitor the pressure gauge as the tank fills, ensuring it operates within its safe working pressure range. Most compressors have an automatic shut-off when the desired pressure is reached, preventing over-pressurization. Allow the compressor to run until the tank is sufficiently filled.
Step 4: Monitor Pressure and Shut Down
As the air compressor runs, continuously monitor the pressure gauge on the tank to ensure it doesn’t exceed its maximum rated pressure. Most compressors are equipped with an automatic shut-off feature that activates once the set pressure is achieved.
Once the tank is filled to your desired pressure or the compressor shuts off automatically, turn off the compressor’s power. It’s always a good practice to then close the tank valve to retain the compressed air. Release any remaining pressure in the hose before disconnecting tools.
Step 5: Drain Condensation from the Tank
After each use, especially if the air compressor has been running for an extended period, it is crucial to drain any accumulated condensation from the tank. Locate the drain valve, typically at the bottom of the tank, and open it slowly to release the water.
This step is vital for preventing rust and corrosion inside the air tank, which can compromise its integrity and shorten its lifespan. Regularly draining condensation ensures the longevity of your air compressor and maintains the quality of the compressed air.
Types of Air Compressors
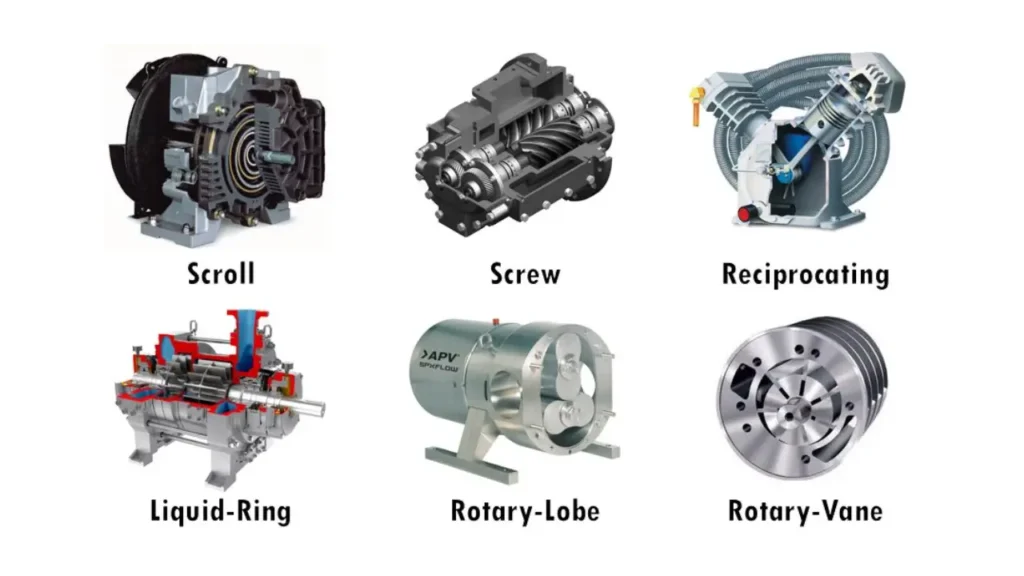
Air compressors are vital tools across various industries, distinguished by their operational mechanisms. Here are the primary types, each suited for different applications and demands:
Reciprocating Piston Air Compressor
The reciprocating piston air compressor is one of the most common types. It works by using a piston within a cylinder to compress air. As the piston moves down, it draws air into the cylinder, and as it moves up, it compresses the trapped air, pushing it out into a storage tank. These air compressors can be single-stage, compressing air once, or multi-stage, compressing air in several steps for higher pressures.
Rotary Screw Air Compressor
The rotary screw air compressor utilizes two intermeshing helical screws (rotors) to compress air. As the rotors turn, air is drawn in at one end, trapped between the screws, and then progressively compressed as it moves along the length of the rotors, exiting at the discharge end. These air compressors are known for their continuous airflow, quiet operation, and energy efficiency, making them ideal for industrial applications requiring a constant supply of compressed air.
Centrifugal Air Compressor
A centrifugal air compressor is a dynamic compressor that uses a rotating impeller to accelerate air to a high velocity. The high-velocity air then enters a diffuser where its kinetic energy is converted into pressure. These air compressors are typically used for very high-volume, low-pressure applications in large industrial settings, such as chemical plants and steel mills, due to their ability to produce oil-free air and handle large capacities.
Axial Air Compressor
The axial air compressor is another type of dynamic compressor that works by continuously compressing air as it flows axially through a series of rotating and stationary blades. Air passes through stages of rotors and stators, with each stage increasing the pressure. These air compressors are often found in gas turbines, jet engines, and large industrial processes where high flow rates and high efficiencies are crucial.
How to Choose the Right Air Compressors
Selecting the appropriate air compressor for your needs involves carefully considering several critical factors to ensure optimal performance, efficiency, and longevity. The first step is to accurately assess your air requirements, including the total air volume needed, the required pressure (PSI or bar), and the duty cycle (how often and how long the compressor will run).
Understanding these basics will narrow down your options significantly, as different compressor types excel in various operational demands. For instance, a small, intermittent task like inflating tires will demand a much different compressor than continuous operation of heavy-duty pneumatic tools in a manufacturing plant.
Once your air requirements are clear, you’ll need to evaluate the technical specifications of available air compressors against your needs. This includes power source, tank size, and portability, among other features. Consider the environment where the compressor will operate, factoring in noise levels and space constraints. Don’t forget to also consider ongoing maintenance requirements and the availability of parts and service in your local area.
- After-sales Service and Parts Availability: Ensure that parts and service support are readily available in your area (Qingdao, Shandong, China, for example) to minimize downtime.
- Air Volume (CFM/LPM): Determine the combined cubic feet per minute (CFM) or liters per minute (LPM) required by all the tools or equipment that will run simultaneously.
- Pressure (PSI/Bar): Identify the maximum pressure (pounds per square inch or bar) needed for your highest-pressure application.
- Duty Cycle: Assess how continuously the compressor will be running. Intermittent use allows for smaller tank sizes, while continuous operation demands a compressor designed for heavy-duty cycles.
- Power Source: Decide between electric (single-phase or three-phase), gasoline, or diesel power based on availability and portability needs.
- Tank Size: A larger tank provides more reserve air, allowing the compressor to cycle less frequently, which is beneficial for consistent demand.
- Portability: Consider if you need a stationary unit or a portable air compressor for on-the-go tasks.
- Noise Level: For indoor or residential use, a quieter compressor (measured in decibels – dB) might be a priority.
- Oil-lubricated vs. Oil-free: Oil-lubricated compressors typically offer longer life and quieter operation but require oil changes. Oil-free compressors are lower maintenance and crucial for applications requiring clean air (e.g., medical, food processing).
- Cost and Budget: Balance the initial purchase price with long-term operating costs, including energy consumption and maintenance.
- Brand Reputation and Warranty: Research reputable brands and understand the warranty coverage for peace of mind.
Conclusion
Understanding how to compress air into a tank safely and efficiently is crucial for anyone utilizing pneumatic systems, from DIY enthusiasts to large industrial operations. By following the outlined steps – from proper preparation and connection to careful monitoring and essential maintenance like draining condensation – you ensure the longevity of your equipment and the safety of your work environment. This comprehensive approach maximizes the benefits of your air compressor.
Proper air compression techniques not only guarantee optimal performance for your tools and machinery but also contribute significantly to energy efficiency and reduced operational costs. Regular maintenance, particularly condensation draining, prevents internal corrosion and extends the lifespan of your valuable equipment, ensuring a consistent and reliable supply of compressed air for all your applications.
For those looking to expand their capabilities or for businesses needing reliable storage solutions, remember that we offer wholesale compressor air tanks. Based in Qingdao, Shandong, China, we provide high-quality, durable air tanks designed to meet diverse industrial and personal needs, ensuring you have the right foundation for your compressed air systems.