Do you know EPS and styrofoam? They are two different types of foam material that can be used for various industries.
This blog post will show you the differences between EPS and Styrofoam.
What Is EPS?
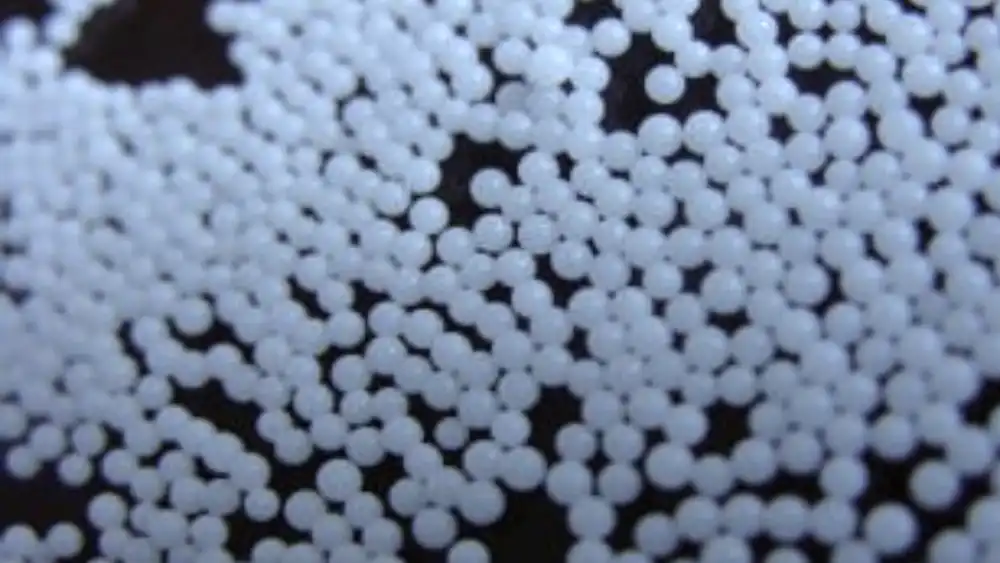
EPS stands for Expanded Polystyrene.
It is a lightweight, foam-like material that is commonly used in various applications such as packaging, insulation, and construction. EPS is made from polystyrene beads that are expanded using steam and then molded into different shapes.
It is known for its excellent thermal insulation properties, resistance to moisture and chemicals, and versatility in shaping. EPS is widely used in the manufacturing of packaging materials, insulation boards for buildings, and cushioning materials for electronics and appliances.
What Is Styrofoam?
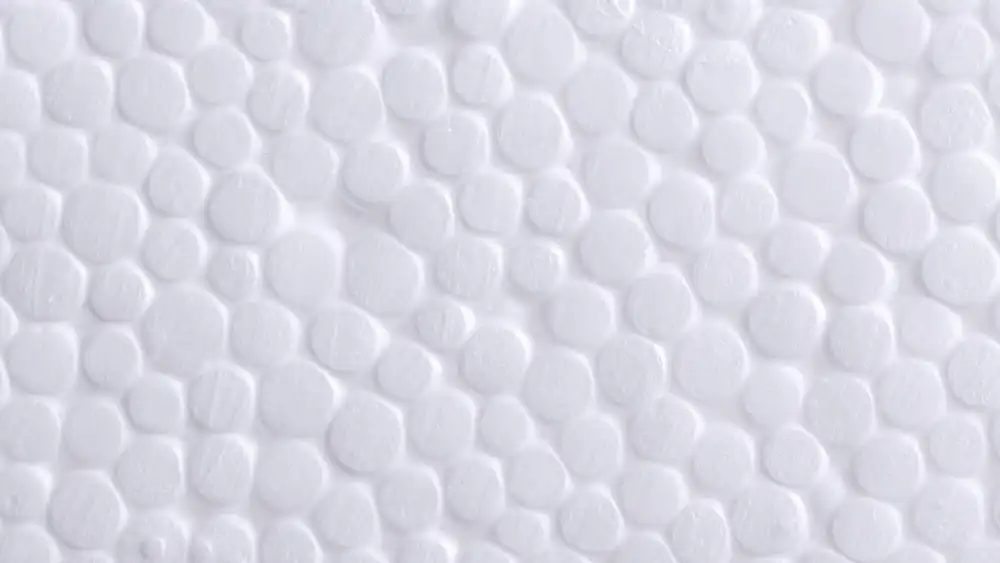
Styrofoam is a trademarked brand of extruded polystyrene foam, commonly used as a lightweight, foam-like material in packaging, insulation, and construction. It is manufactured through an extrusion process where polystyrene pellets are melted and forced through a die to form sheets of foam.
These sheets are then cut into the desired shape and size. Styrofoam is known for its high compressive strength, low thermal conductivity, water resistance, and smooth surface finish. It finds applications in insulation panels for construction, food and beverage containers, packaging materials, and various other products.
Composition and Production Process
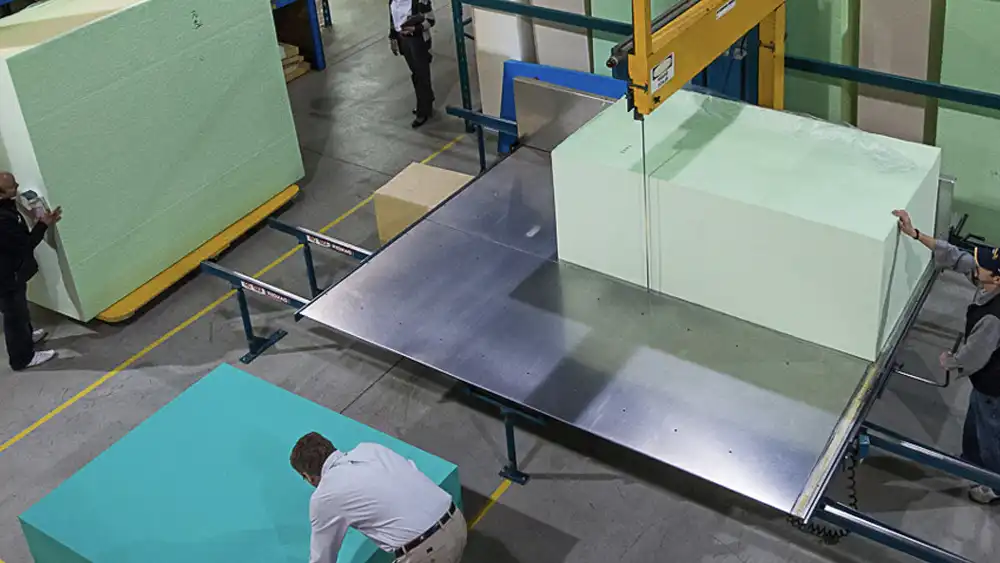
EPS:
Expanded Polystyrene (EPS) is composed of polystyrene beads that undergo a specific manufacturing process to achieve its foam-like structure. The production process typically involves the following steps:
- Pre-expansion: Polystyrene beads are pre-expanded using steam, which causes them to expand and become lighter.
- Molding: The expanded beads are then molded into various shapes and forms using molds and heat. This molding process allows for the creation of customized shapes and sizes.
- Fusing: After molding, the expanded beads are fused together using heat and pressure to form the final EPS product. This fusing process ensures structural integrity and stability.
Styrofoam:
Styrofoam, a brand of extruded polystyrene foam, undergoes a different production process compared to EPS. The production process for Styrofoam involves the following steps:
- Extrusion: Polystyrene pellets are melted and mixed with additives to enhance certain properties, such as rigidity and durability. The molten mixture is then extruded through a die, forming continuous sheets or boards of foam.
- Cooling and Shaping: As the extruded foam passes through the die, it undergoes rapid cooling, which solidifies the foam into its final shape. The foam is then cut into sheets or molded into specific shapes as needed for various applications.
- Finishing: After shaping, the Styrofoam products may undergo additional processes such as surface finishing or coating to improve appearance or performance.
While both EPS and Styrofoam are made from polystyrene, they differ in their production processes. EPS involves the expansion of pre-expanded beads, molding, and fusing, whereas Styrofoam is produced through extrusion, cooling, shaping, and finishing. These different manufacturing methods result in distinct properties and characteristics for each material.
Properties and Characteristics
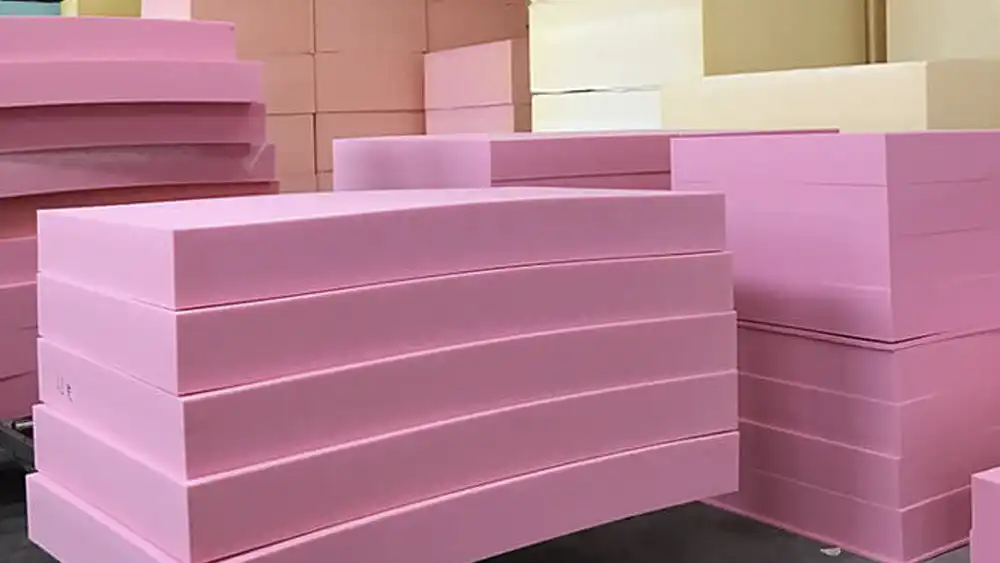
EPS:
- Lightweight: EPS is lightweight, making it easy to handle and transport.
- Excellent Thermal Insulation: EPS offers superb thermal insulation properties, helping to maintain temperature stability and energy efficiency.
- Moisture Resistance: EPS is resistant to moisture, making it suitable for use in humid environments or as packaging for moisture-sensitive items.
- Chemical Resistance: EPS exhibits resistance to many chemicals, enhancing its durability and longevity in various applications.
- Versatility: EPS is versatile and can be easily shaped and molded into different forms and sizes to suit specific needs.
- Affordability: EPS is cost-effective compared to some alternative materials, making it a popular choice for packaging and insulation applications.
Styrofoam:
- High Compressive Strength: Styrofoam possesses high compressive strength, making it suitable for load-bearing applications such as insulation in construction.
- Low Thermal Conductivity: Styrofoam has low thermal conductivity, providing effective insulation against heat transfer.
- Water Resistance: Styrofoam is resistant to water absorption, making it ideal for use in damp or wet environments without compromising its structural integrity.
- Smooth Surface Finish: Styrofoam typically has a smooth surface finish, making it suitable for applications where aesthetics are important, such as architectural models or decorative elements.
- Lightweight and Buoyant: Styrofoam is lightweight and buoyant, making it useful for flotation devices or in applications where weight is a concern.
- Chemical Stability: Styrofoam exhibits stability in the presence of many chemicals, ensuring its durability in various environments.
Both EPS and Styrofoam offer unique properties and characteristics that make them suitable for a wide range of applications. EPS excels in thermal insulation, moisture resistance, and versatility, while Styrofoam stands out for its high compressive strength, low thermal conductivity, and smooth surface finish.
Applications and Uses
EPS:
Packaging Materials: EPS is widely used in the packaging industry for various applications such as:
Packaging boxes
Protective packaging for fragile items
Insulated shipping containers for food and pharmaceuticals
Insulation: EPS is valued for its thermal insulation properties, making it suitable for:
Insulation boards for buildings and homes
Insulated concrete forms (ICFs) for construction projects
Roof insulation panels to improve energy efficiency
Geofoam: EPS is used as lightweight fill material in civil engineering and construction projects, including:
Road and highway construction
Bridge approaches and abutments
Retaining walls and slope stabilization
Cushioning Materials: EPS is utilized for cushioning and protecting delicate items during transportation and storage, such as:
Packaging inserts for electronics and appliances
Protective padding for furniture and glassware
Molded foam inserts for automotive components
Styrofoam:
Insulation Panels: Styrofoam’s high compressive strength and low thermal conductivity make it suitable for:
Insulation panels for walls, floors, and roofs in residential and commercial buildings
Underlayment for flooring to provide thermal and moisture resistance
Food and Beverage Containers: Styrofoam’s lightweight and insulating properties make it ideal for:
Disposable cups and plates for hot and cold beverages
Take-out containers for fast food and restaurants
Food trays for catering and events
Packaging Materials: Styrofoam is commonly used in packaging applications due to its:
Ability to protect fragile items during shipping and handling
Lightweight nature, reducing transportation costs
Moldability to create custom packaging shapes and sizes
Floral and Craft Products: Styrofoam’s versatility extends to:
Floral foam for arranging flowers and decorative displays
Craft foam sheets for art and DIY projects
Styrofoam balls and shapes for modeling and sculpting
Both EPS and Styrofoam have diverse applications across industries such as packaging, construction, and crafts. While EPS excels in insulation and geofoam applications, Styrofoam finds its niche in food packaging, insulation panels, and creative endeavors.
Environmental Impact
EPS
- Non-biodegradable and takes hundreds of years to decompose
- Can be recycled, but not widely accepted due to limited facilities and market demand
- Lightweight nature reduces carbon footprint during transportation
Styrofoam
- Not biodegradable and persists in the environment for centuries
- Limited recycling options, with most facilities only accepting clean, white foam
- Lightweight, reducing fuel consumption during transportation
Recycling and Disposal Methods
Both EPS and Styrofoam can be recycled, but the process is not as straightforward due to limited facilities and market demand. Some companies offer mail-back programs or drop-off locations for recycling these materials. Additionally, both can be compacted and used in various applications such as insulation or packaging filler.
Cost Comparison
In terms of cost, EPS tends to be more affordable compared to Styrofoam. This cost difference is attributed to the manufacturing processes and availability of raw materials. However, the overall cost may vary depending on factors such as quantity, location, and specific application.
Conclusion
In conclusion, while EPS and Styrofoam serve similar purposes in packaging and insulation, they have distinct differences in composition, properties, and environmental impact. While EPS is more widely used and recyclable to some extent, Styrofoam offers specific advantages in terms of strength and insulation properties. Moving forward, there is a need for greater emphasis on sustainable alternatives and recycling solutions to mitigate the environmental impact of these materials.
FAQs
Can EPS and Styrofoam be recycled together?
While both materials are recyclable, it’s best to check with local recycling facilities as they may have specific guidelines for each material.
Are there any health risks associated with using EPS or Styrofoam products?
When used as intended, EPS and Styrofoam products are generally considered safe. However, there may be concerns about chemical emissions during production and disposal.
Why is Styrofoam not widely accepted for recycling?
Styrofoam recycling faces challenges due to limited infrastructure and market demand for recycled materials. Additionally, contamination and the presence of dyes or adhesives can affect the recycling process.
What are some alternatives to EPS and Styrofoam?
Biodegradable materials such as molded pulp, mushroom packaging, or compostable plastics are emerging as alternatives to EPS and Styrofoam.
How can consumers reduce their use of EPS and Styrofoam products?
Consumers can opt for reusable or biodegradable alternatives, minimize single-use packaging, and support businesses that prioritize sustainable packaging solutions.