EPS Packaging: Prevent Product Damage and Protect Your Profits
Protect your products with lightweight, durable EPS packaging. Our custom solutions offer superior shock absorption and insulation, keeping your goods safe during transit. Reduce shipping costs and environmental impact without compromising protection. Contact us today for a free quote and discover the EPS difference.
Customize your desired EPS Packaging
Shape and Size:
- Precision Fitting: EPS packaging can be molded into virtually any shape to perfectly fit your product, minimizing empty space and maximizing protection.
- Customization: Whether you need a simple box or a complex insert, EPS can be tailored to your exact specifications.
Material Density
- Protection Level: Different densities of EPS offer varying levels of shock absorption and insulation.
- Weight Considerations: Balancing product protection with shipping costs requires careful selection of EPS density.
Surface Finish:
- Aesthetics: Choose from smooth, textured, or embossed finishes to enhance your product’s presentation.
- Functionality: Certain finishes can improve grip or provide additional protection.
Branding and Customization:
- Product Identity: Incorporate your brand’s logo, colors, and messaging directly onto the EPS packaging.
- Promotional Opportunities: Use the packaging as a marketing tool to increase brand visibility and engagement.
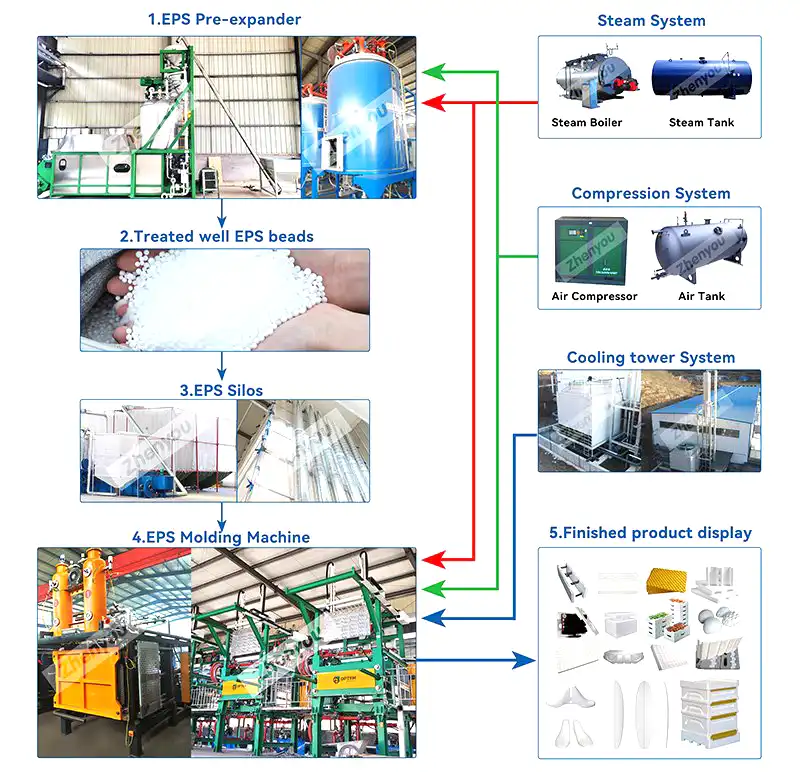
EPS Moulding Process
1. Pre-Expansion
- EPS Bead Preparation: Small polystyrene beads are prepared as the raw material.
- Expansion: The beads are heated with steam, causing them to expand significantly.
- Cooling: Expanded beads are cooled and dried.
2. Molding
- Mold Preparation: A mold with the desired shape is prepared.
- Bead Filling: Expanded beads are filled into the mold cavity.
- Heating and Fusion: Steam is injected into the mold, heating the beads and causing them to fuse together under pressure, forming the shape of the mold.
- Cooling: The molded product is cooled to solidify the EPS foam.
- Demolding: The finished product is removed from the mold.
Various EPS Packaging
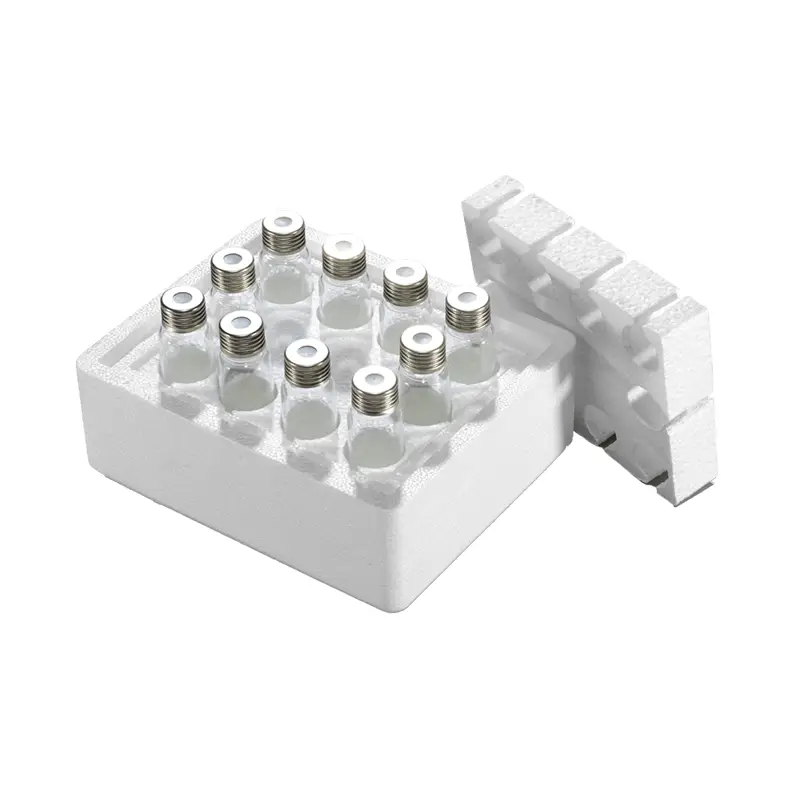
ePS foam packaging
Protect your products with Epsole’s high-performance EPS foam packaging. Our custom solutions offer superior insulation, shock absorption, and lightweight protection. Reduce shipping damages and enhance your brand image. Contact us today for a free quote and discover the Epsole difference.
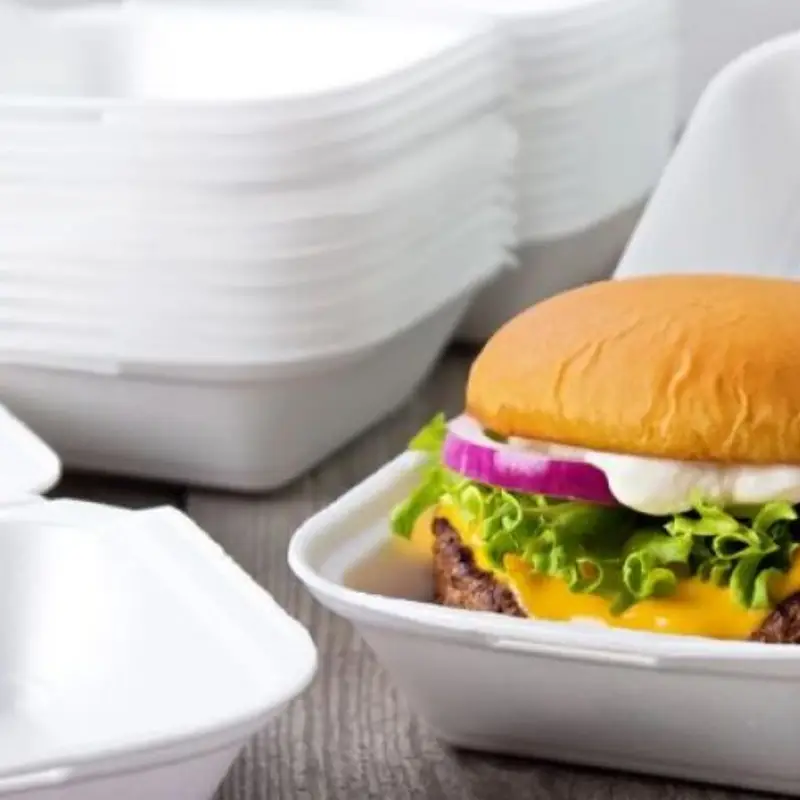
ePS food packaging
We offer superior EPS food packaging solutions. Our products protect freshness, maintain temperature, and reduce food waste. From sturdy fish boxes to delicate dessert containers, we customize packaging to meet your specific needs. Trust Epsole for safe, reliable, and eco-friendly food packaging. Contact us today to discuss your requirements.
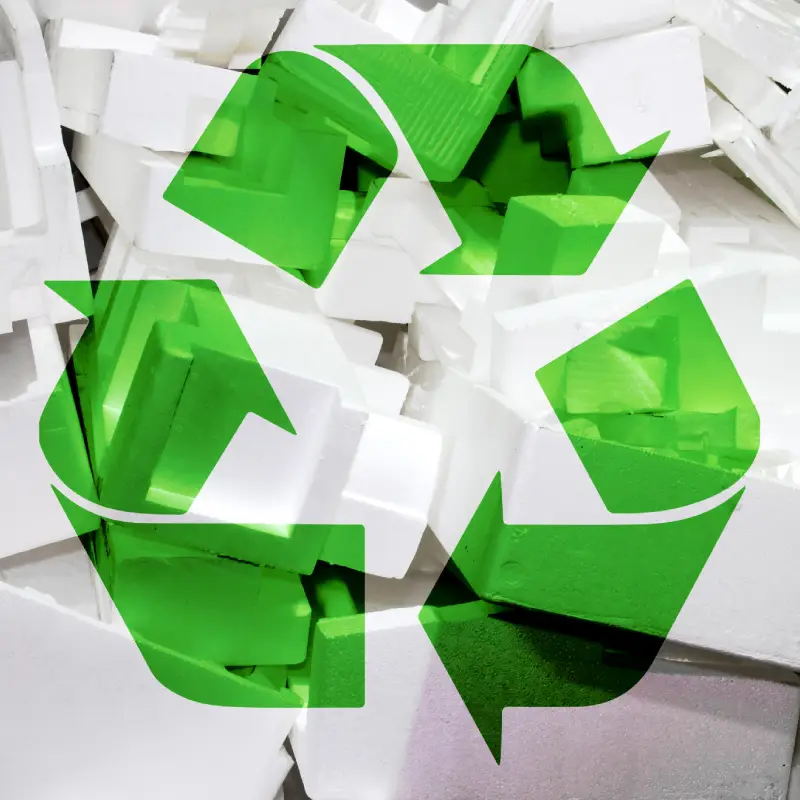
EPS packaging recycling
We at Epsole are committed to a sustainable future. Our EPS packaging is 100% recyclable. Cooperate with us in protecting the environment by using the recycling EPS packaging. For more info about wholesale recyclable EPS packaging, please hit the button below.
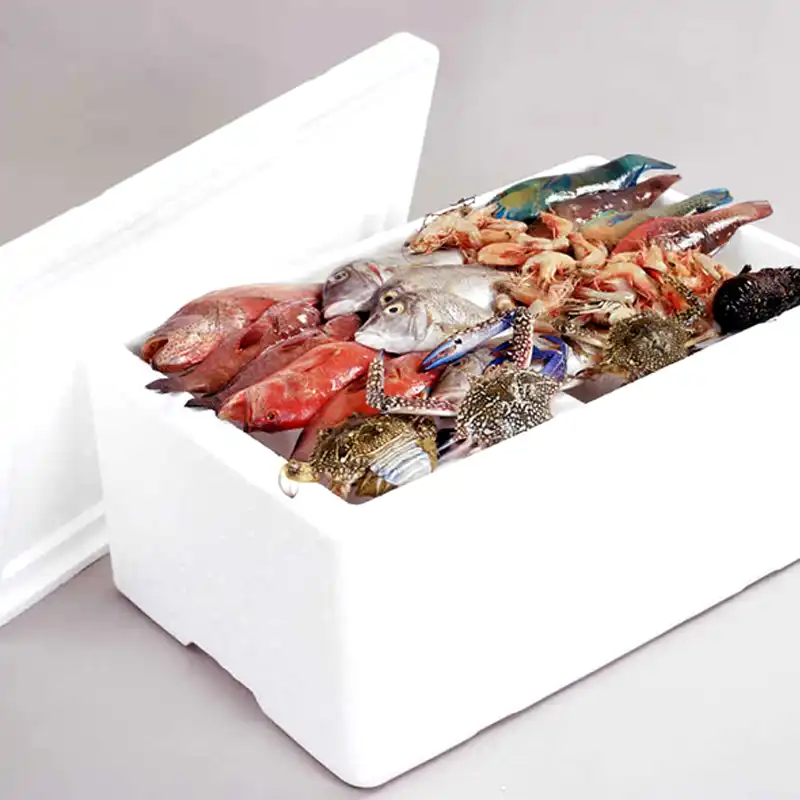
EPS Fish packaging
Protect your fresh catch with our durable, insulated EPS fish boxes. Our custom-designed boxes maintain optimal temperatures, preserving your fish’s quality. Reduce spoilage and increase profits. Contact us today to discuss your specific needs and get a quote.
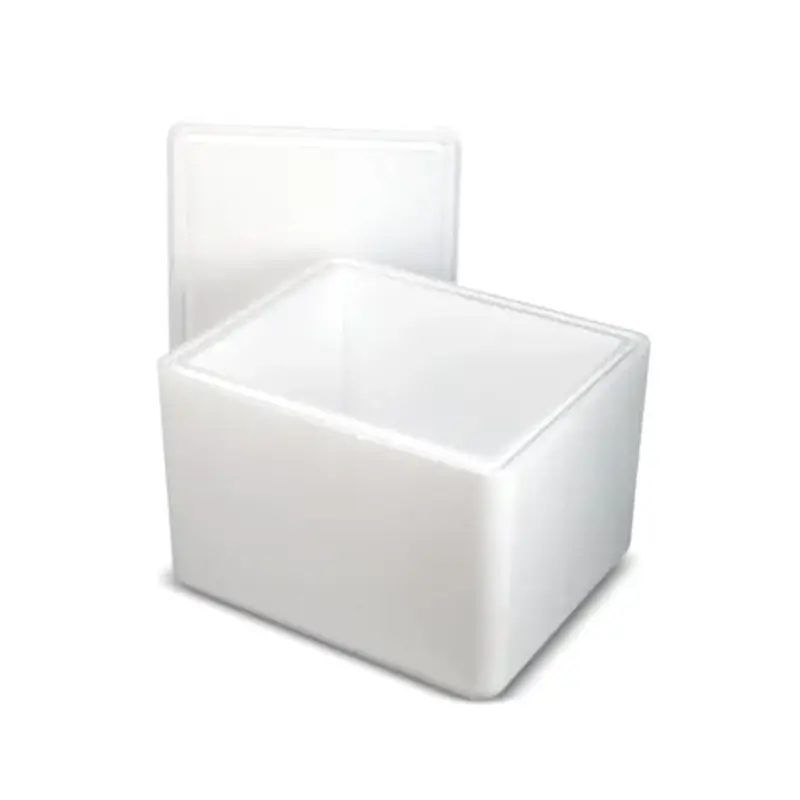
EPS thermocol box
Protect your valuable products with Epsole’s high-quality EPS thermocol boxes. Our custom-designed packaging solutions offer superior insulation, shock absorption, and durability. Contact us today to discuss your packaging needs and experience the Epsole difference.
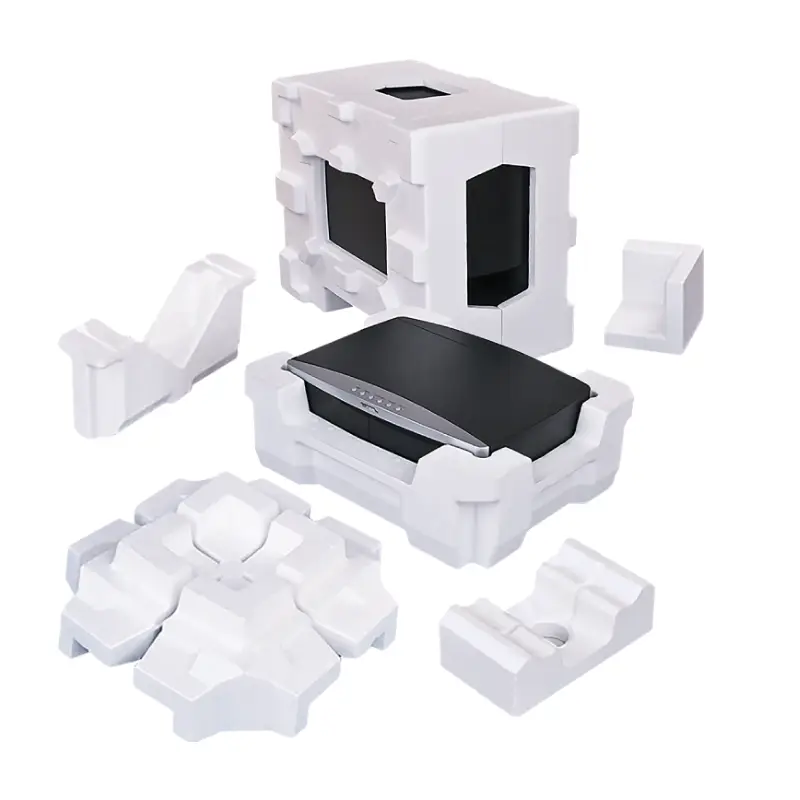
EPS moulded packaging
EPS molded packaging is a superior solution for safeguarding your valuable products during shipping and storage. Crafted from expanded polystyrene, EPS offers exceptional shock absorption, insulation, and lightweight properties.
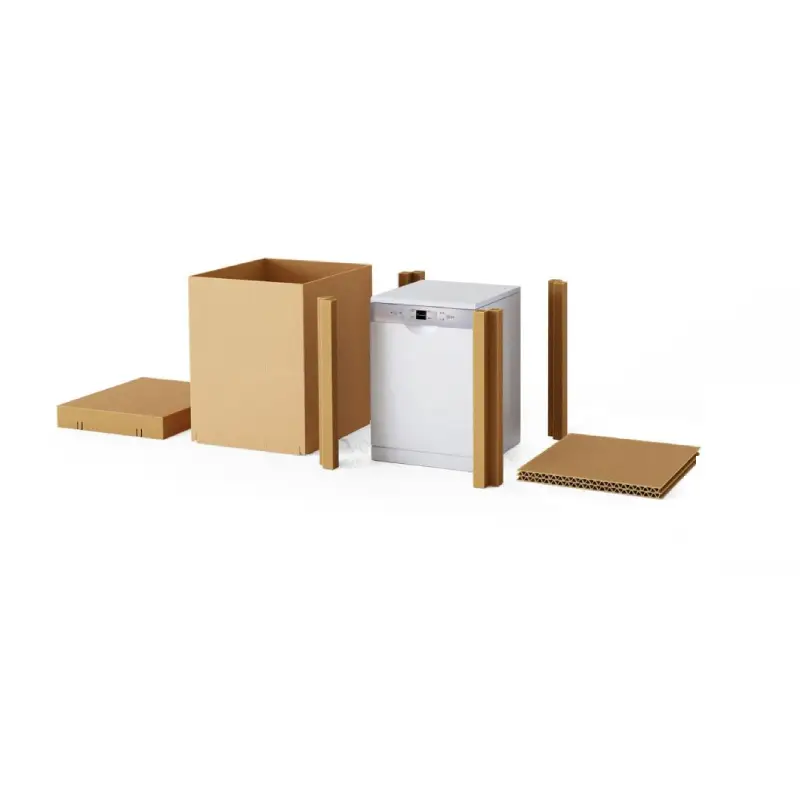
EPS Sustainable packaging
EPS (Expanded Polystyrene) has often been misunderstood as an environmentally harmful material. However, with a focus on recycling and innovation, the industry is making significant strides towards sustainability. Welcome to quote these EPS green packaging for your projects.
EPS Moulding Machine Needed
EPS Packaging FAQs
What is EPS Packaging
EPS packaging is a type of protective packaging made from expanded polystyrene (EPS), a lightweight, rigid foam material. Commonly known as “styrofoam,” EPS is widely used in various industries due to its excellent shock absorption, insulation, and cost-effectiveness.
Key characteristics of EPS packaging:
- Lightweight: Reduces shipping costs and environmental impact.
- Strong and durable: Protects products from damage during transportation.
- Excellent shock absorption: Safeguards fragile items.
- Insulating properties: Maintains product temperature.
- Cost-effective: Provides superior protection at a competitive price.
- Versatile: Can be molded into various shapes and sizes to fit different products.
What Are EPS Packaging Applications?
EPS packaging is incredibly versatile, finding application in numerous industries due to its protective, insulating, and lightweight properties. Here are some of the most common applications:
Electronics and Appliances
- Protection: EPS is ideal for protecting fragile electronics like TVs, computers, and smartphones from shocks and vibrations during shipping.
- Static protection: EPS helps prevent static electricity buildup, which can damage electronic components.
Food and Beverage
- Insulation: EPS containers keep food and beverages hot or cold, maintaining product quality.
- Freshness: EPS packaging protects perishable items like seafood and meat from temperature fluctuations.
- Hygiene: EPS is resistant to bacteria and mold, ensuring food safety.
Automotive
- Protective packaging: EPS is used to protect car parts and components during transportation.
- Insulation: EPS is employed in automotive interiors for thermal insulation.
Medical and Pharmaceutical
- Insulation: EPS packaging maintains the temperature of sensitive medical products like vaccines and pharmaceuticals.
- Protection: EPS protects fragile medical equipment during shipping.
Construction
- Insulation: EPS is used as insulation material in building construction.
- Packaging: EPS protects construction materials during transportation.
Other Applications
- Packaging for industrial products: EPS is used to protect various industrial goods, from machinery parts to chemicals.
- Consumer goods: EPS is found in packaging for toys, cosmetics, and other consumer products.
How to mold EPS packaging?
EPS (Expanded Polystyrene) packaging is molded through a process involving heat and pressure.
Here’s a simplified steps of molding EPS packaging:
The EPS Molding Process
- Pre-Expanded Beads: EPS begins as small polystyrene beads. These beads are pre-expanded with steam to increase their volume.
- Mold Preparation: A mold with the desired shape of the packaging is prepared.
- Bead Filling: The pre-expanded beads are filled into the mold cavity.
- Heating and Expansion: Steam is introduced into the mold, heating the beads and causing them to expand further. The pressure within the mold forces the beads to fuse together, taking the shape of the mold.
- Cooling: The molded product is cooled to solidify the EPS foam.
- Demolding: The finished EPS packaging is removed from the mold.
Key Equipment
- Mold: The heart of the process, determining the shape of the final product.
- Steam Generator: Provides the steam for bead expansion and fusion.
- Vacuum System: Helps remove moisture and air from the mold.
- Cooling System: Cools the molded product to solidify the EPS.
Factors Affecting EPS Molding
- Mold Design: The accuracy and complexity of the mold directly impact the final product.
- Steam Pressure and Temperature: Precise control is essential for consistent results.
- Bead Density: The density of the pre-expanded beads affects the final product’s density and strength.
- Molding Cycle Time: The duration of the molding process influences productivity.
Note: The actual process can be more complex, involving advanced machinery and precise control systems to ensure product quality and efficiency.