Hot wire foam cutters are indispensable tools for achieving precise, clean cuts in various foam types, from crafting to insulation. Unlike traditional blades, they melt rather than tear the foam, creating smooth edges with minimal debris.
Mastering the art of hot wire foam cutting requires understanding the best practices to ensure optimal results. This guide will delve into techniques and tips to help you achieve perfectly clean edges on all your foam projects, enhancing both aesthetics and functionality.
Getting Started with Hot Wire Foam Cutting (DIY Foam Cutting!)
For those new to hot wire cutting, fear not! It’s a relatively simple process that crafters of all experience levels can enjoy.
There are two main options to get started:
- Purchasing a Hot Wire Cutter: This is the easiest approach. Pre-made hot wire cutters are readily available at craft stores and online retailers. They come in various styles, from basic handheld units to more advanced models with adjustable temperatures and cutting angles.
- Building Your Own Hot Wire Cutter (How to Make a Hot Wire for Cutting Foam): For the DIY enthusiasts, building your own hot wire cutter is a fun and rewarding project. You’ll typically need nichrome wire, a power supply (with adjustable voltage for temperature control is ideal), and a material to hold and guide the wire (wood is a common choice). Safety is paramount, so ensure all electrical connections are secure and use a heat-resistant handle.
Now that you have your hot wire, let’s explore what kind of foam you can use!
- XPS Foam: This rigid, blue or pink foam is commonly used for insulation and building projects. It’s great for architectural models and larger creations.
- Upholstery Foam: Perfect for creating cushions, props, or cosplay armor.
- Polyurethane Foam: This versatile foam comes in various densities and is great for packaging inserts, craft projects, and model making.
- Polyethylene Foam: Often used for packaging materials and soundproofing, it can be cut with a hot wire for specific applications.
Beyond the Basics: Creative Applications of Hot Wire Foam Cutting
Hot wire cutting opens a door to endless creative possibilities. Here are just a few ideas to spark your imagination:
- Foam Gun Case: Design and cut a custom foam insert to perfectly cradle your firearm and accessories for safe storage and transport.
- Foam Wings for Cosplay or Model Airplanes: Craft lightweight and detailed wings for your next costume or model project.
- Foam Rubber Stamps: Create custom shapes from foam rubber for unique and personalized stamped designs.
- Foam Board Sculptures: Construct impressive 3D sculptures or signs using layered foam board cut into desired shapes.
- EVA Foam (Can You Cut EVA Foam with a Hot Wire?): Absolutely! EVA foam is popular for cosplay costumes and crafting projects due to its soft and flexible properties.
While a 3-in-1 hot wire foam cutting tool might offer additional functionalities like soldering or burning, a basic hot wire cutter is sufficient for most projects. Remember, cutting spray foam with a hot wire is not recommended as it can be messy and potentially release harmful fumes. For cutting thick spray foam, a hot knife or alternative tools are better suited.
Ready to take the plunge into the world of hot wire foam cutting (CNC hot wire foam cutting machine is another option for high-precision needs!)? With a little practice and creativity, you’ll be shaping your own masterpieces in no time! So grab your hot wire, and let the crafting adventure begin!
How to Cut Foam With a Hot Wire
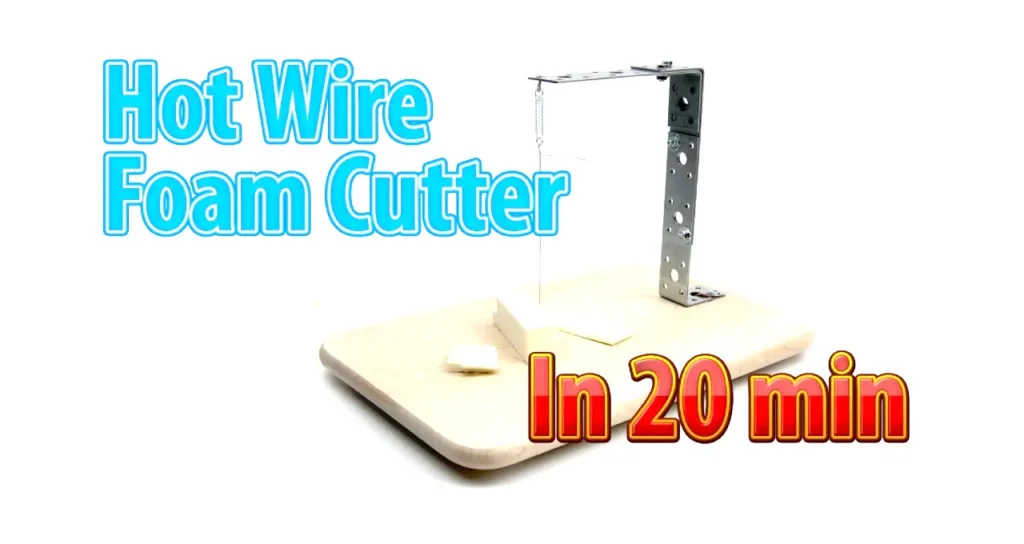
Cutting foam with a hot wire transforms a challenging task into a smooth, precise operation. This method leverages heat to melt through the material, yielding clean edges far superior to those achieved with traditional blades.
Mastering this technique involves several crucial steps, from proper setup to the actual cutting motion, ensuring safety and optimal results. Follow this guide for best practices in achieving professional-quality foam cuts.
Step 1. Prepare Your Workstation
Before you begin cutting, ensure your workspace is well-ventilated, as melting foam can release fumes. Lay down a protective surface, like a scrap piece of wood or cardboard, to shield your table from accidental contact with the hot wire. This prevents damage and provides a stable base for your foam.
Additionally, gather all necessary tools, including your hot wire cutter, ruler, and any templates you plan to use. Having everything within reach will streamline your cutting process and minimize interruptions, contributing to smoother, more consistent cuts.
Step 2. Set Up the Hot Wire Cutter
Properly assembling your hot wire cutter is critical for safety and performance. Ensure the hot wire is securely attached to the cutting tool’s arms or frame, following the manufacturer’s instructions carefully. A taut, well-tensioned wire is essential for straight and precise cuts.
Next, plug in your hot wire cutter and allow it sufficient time to heat up. The ideal temperature will vary depending on the foam density and type, so some initial testing on a scrap piece is often beneficial to find the perfect heat setting.
Step 3. Mark Your Cutting Lines
Accurate marking is paramount for precise foam cutting. Use a ruler and a fine-tipped marker or pencil to clearly draw your desired cutting lines directly onto the foam surface. For complex shapes, consider creating templates from paper or thin cardboard.
Ensure your marks are visible but not so deep they deform the foam. Precise lines act as your guide, helping you maintain a steady hand and consistent path as you move the hot wire through the material, leading to cleaner edges.
Step 4. Perform the Cut
With your foam marked and the wire heated, begin the cut. Slowly and steadily guide the hot wire along your marked line, applying gentle, consistent pressure. Allow the heat to melt through the foam; avoid forcing the wire, as this can lead to uneven cuts or breakage.
Maintain a consistent speed throughout the cut. Moving too fast will result in a jagged edge, while moving too slowly can create an overly wide kerf or burn marks. Practice on scrap pieces to find the optimal speed for your specific foam type and wire temperature.
Step 5. Finish and Clean Up
Once the cut is complete, carefully separate the foam pieces. Unplug your hot wire cutter and allow it to cool down completely before storing it. Proper cooling prevents accidental burns and extends the life of the tool.
Finally, clean your workstation. Dispose of any foam scraps responsibly. Ensure all tools are put away safely. A tidy workspace is crucial for safety and prepares you for your next project, maintaining efficiency and organization.
How to Make a Hot Wire for Cutting Foam
While you can purchase pre-made hot wire cutters for convenience, building your own offers a rewarding DIY experience! Here’s a breakdown of how to make a hot wire for cutting foam:
Materials:
- Nichrome Wire: This high-resistance wire heats up significantly when electricity passes through it. Choose a thickness suitable for your projects (typically between 26 gauge and 32 gauge).
- Power Supply: You’ll need a power supply that can provide enough voltage to heat the nichrome wire effectively. A transformer or a wall adapter with adjustable voltage (for temperature control) are good options.
- Wire Holder: This will hold the nichrome wire taut and guide it during cutting. Wood or a sturdy metal bracket are common choices.
- Electrical Wires: To connect the nichrome wire to the power supply.
- Safety Equipment: Eye protection, gloves, and heat-resistant materials for handling the wire.
Instructions:
- Prepare the Wire Holder: Design and build your wire holder. It should securely hold the nichrome wire with a mechanism to keep it taut (e.g., screws with wing nuts). You can find plans for various holder designs online.
- Cut and Attach Nichrome Wire: Cut a length of nichrome wire based on the desired cutting length (longer for wider cuts). Securely attach the ends of the wire to the holder using crimp connectors or high-temperature resistant wire loops.
- Connect the Power Supply: Following safety precautions and proper electrical wiring practices, connect the nichrome wire to the power supply using the additional electrical wires. Ensure a secure and insulated connection. Note: It’s advisable to consult a qualified electrician if unsure about electrical wiring.
- Test and Adjust: With safety glasses on, test your hot wire setup on a scrap piece of foam. If the wire doesn’t heat up enough, adjust the voltage on your power supply (if possible) or consider using a thicker nichrome wire.
Safety Tips:
- Always wear safety glasses while using your hot wire cutter.
- Ensure all electrical connections are secure and insulated to avoid shorts or shocks.
- Use a heat-resistant handle or material to hold the wire holder during cutting.
- Never leave your hot wire cutter unattended when plugged in.
- Only use your hot wire cutter in a well-ventilated area, as fumes may be produced while cutting foam.
Remember: Building a hot wire cutter involves working with electricity. If you’re uncomfortable with electrical wiring, it’s best to purchase a pre-made hot wire cutter for safe and easy use.
Cutting Polyurethane Foam With Hot Wire
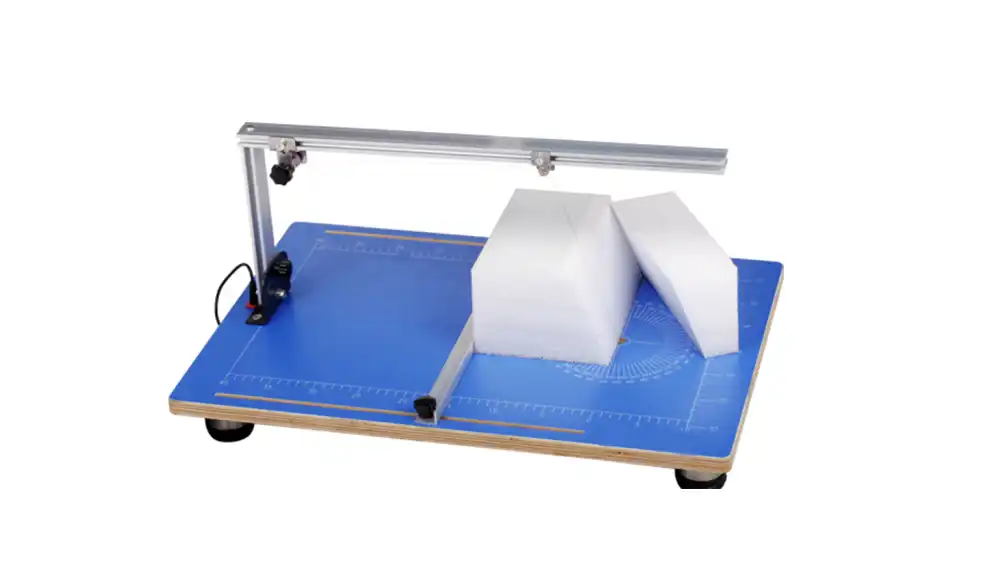
Absolutely not! Cutting polyurethane foam with a hot wire cutter is strongly discouraged for several reasons:
- Toxic Fumes: Polyurethane foam, when heated, releases harmful fumes that can irritate your lungs and eyes. These fumes can be particularly dangerous in poorly ventilated areas.
- Messy Cutting: Hot wire cutting on polyurethane foam tends to be messy. The heat can melt the foam unevenly, leaving behind a rough and uneven cut surface.
- Ineffective Cutting: Polyurethane foam can be denser and more difficult to cut cleanly with a hot wire compared to other foams like polystyrene (Styrofoam) or XPS foam.
Safer Alternatives for Cutting Polyurethane Foam:
Here are some safer and more effective methods for cutting polyurethane foam:
- Sharp Blades: Using a sharp utility knife, craft knife, or bread knife can provide clean and precise cuts on polyurethane foam. Opt for a serrated blade for thicker foams.
- Electric Cutting Tools: Electric carving knives or hot knives specifically designed for foam cutting can offer better control and cleaner cuts compared to a standard hot wire cutter.
- Die Cutters: For repetitive cuts on polyurethane foam sheets, consider using a die-cutting machine. This allows for consistent and precise shapes.
Important Note: Always ensure proper ventilation when cutting polyurethane foam, regardless of the method used. Consider wearing a dust mask for additional protection from airborne particles.
Here’s a quick comparison table to summarize:
Method | Polyurethane Foam | Other Foams (XPS, Styrofoam) |
---|---|---|
Hot Wire Cutting | Not Recommended (Toxic fumes, messy cuts) | Works well, clean cuts |
Sharp Blades | Effective, clean cuts | Effective, clean cuts |
Electric Cutting Tools | Effective, cleaner cuts than hot wire | Very effective, clean cuts |
Die Cutters | Effective for repetitive shapes | Not ideal |
Can You Cut Eva Foam With a Hot Wire?
Yes, you can cut EVA foam with a hot wire, but it’s generally not recommended for the best results or safety.
While the hot wire will melt through EVA foam, it often creates a strong, unpleasant odor and can produce a sticky, melted residue that clings to the wire and the foam, leading to less clean cuts and potential damage to your tool.
Traditional sharp blades are usually preferred for cleaner EVA foam cuts. While hot wire cutters are excellent for polystyrene foams (EPS and XPS), they are not ideal for EVA foam. EVA (Ethylene Vinyl Acetate) has a different chemical composition and melts differently. Using a hot wire on EVA foam can produce significant, potentially harmful fumes and result in a messy, uneven cut rather than the clean, precise edges achieved with polystyrene. Other tools like sharp utility knives or rotary cutters are generally recommended for EVA foam.
Can You Cut Polyurethane Foam With a Hot Wire?
Cutting polyurethane foam with a hot wire is generally not recommended and strongly discouraged. Unlike polystyrene foams (EPS and XPS) which melt cleanly, polyurethane foam tends to scorch, produce a very messy cut with melted plastic residue, and most importantly, release harmful and toxic fumes when heated. For safety, it’s best to use sharp blades, electric carving knives, or specialized hot knives designed for polyurethane.
Conclusion
By consistently applying the best practices for hot wire foam cutting – from proper ventilation and wire tension to controlled speed and temperature – you can achieve professional-grade results. These techniques ensure clean, smooth edges, enhancing the quality of your projects and minimizing waste.
Remember that practice makes perfect. Experiment with different foam types and densities to truly master the nuances of your hot wire cutter. Your precision will improve with every cut, opening up new creative possibilities.
For your large-scale foam needs, consider sources like Epsole for wholesale EPS foam. Utilizing quality materials combined with these cutting best practices will elevate your foam projects to the next level.