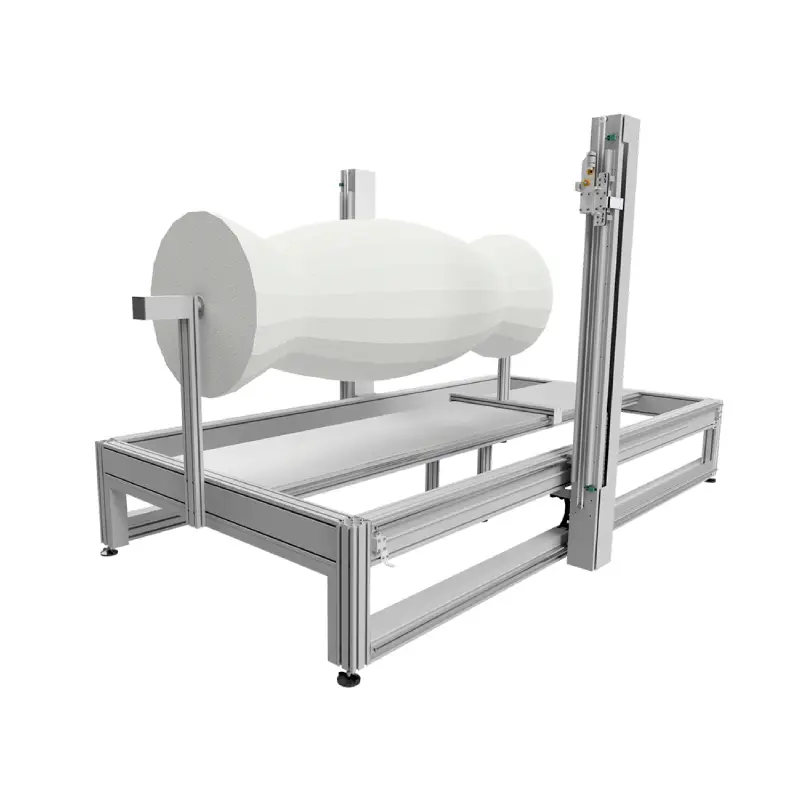
Importing CNC Foam Cutting Machine
We provide advanced CNC foam cutting machines, designed to deliver unparalleled precision and efficiency. Our machines are perfect for a wide range of applications, from prototyping to large-scale production. Import our cutting-edge technology and elevate your foam cutting operations.
Why Choose Our EPS Foam Cutting Machine
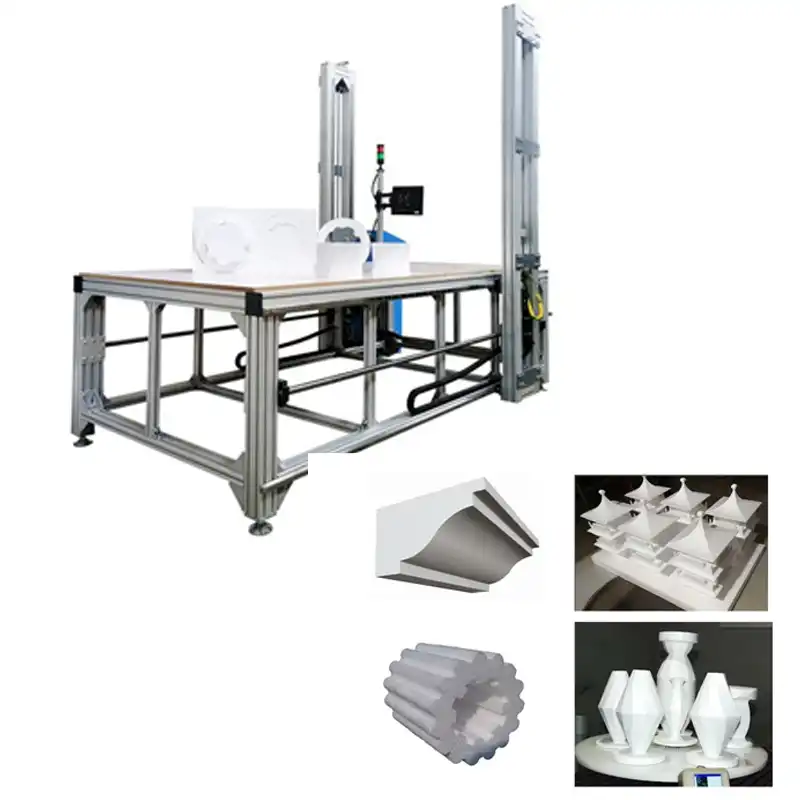
Our EPS foam cutting machine offers unparalleled precision and efficiency. With advanced CNC technology, you can create intricate designs and complex shapes with ease.
- Unmatched Accuracy: Precision cutting for flawless results.
- Superior Efficiency: Streamlined workflow and faster production times.
- Versatile Applications: Ideal for various industries, from packaging to construction.
- Durable Construction: Built to last, ensuring long-term reliability.
Why Choose Our EPS Recycling Machine
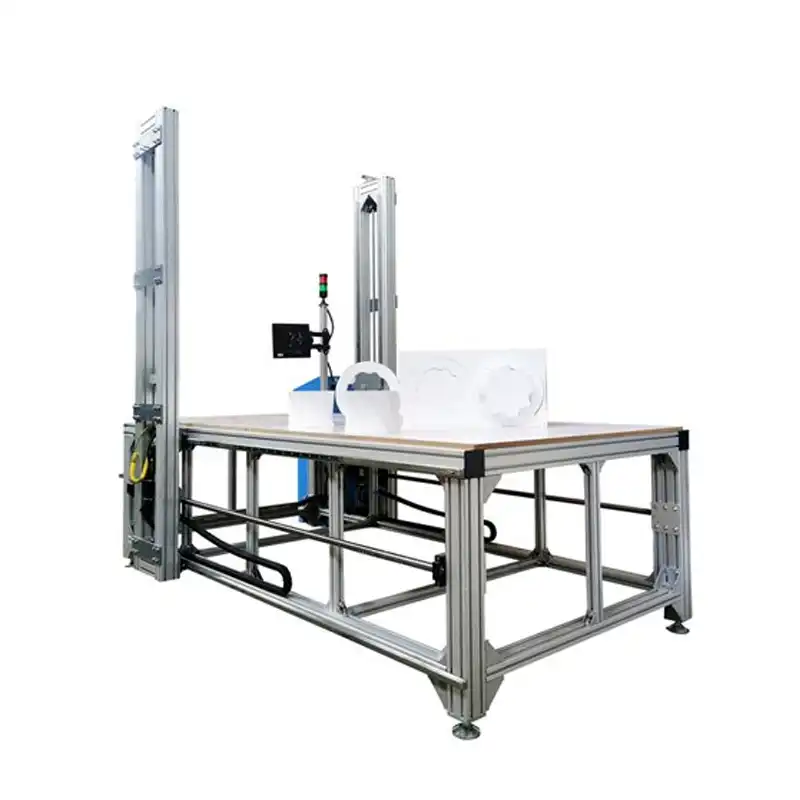
CNC EPS Foam Cutting Machine
We provide qualified CNC EPS foam cutting machines. Our machines offer precise cutting, intricate designs, and efficient production. Ideal for various applications like packaging, insulation, and more, our machines ensure high-quality results and optimize your workflow. Contact us now to get cnc foam cutting machine price.
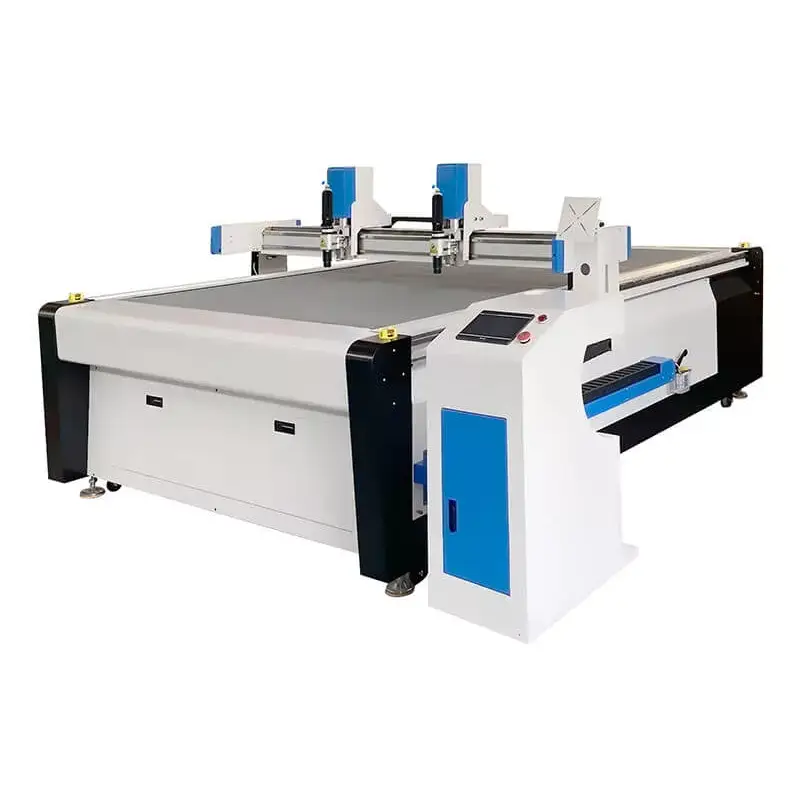
CNC Eva Foam Cutting Machine
We provide EVA foam cutting machines, designed to deliver precise and efficient cuts. Ideal for crafting custom shapes and intricate designs, our machines are perfect for industries like sports, cosplay, and prototyping. Experience the future of EVA foam cutting with our cutting-edge technology.
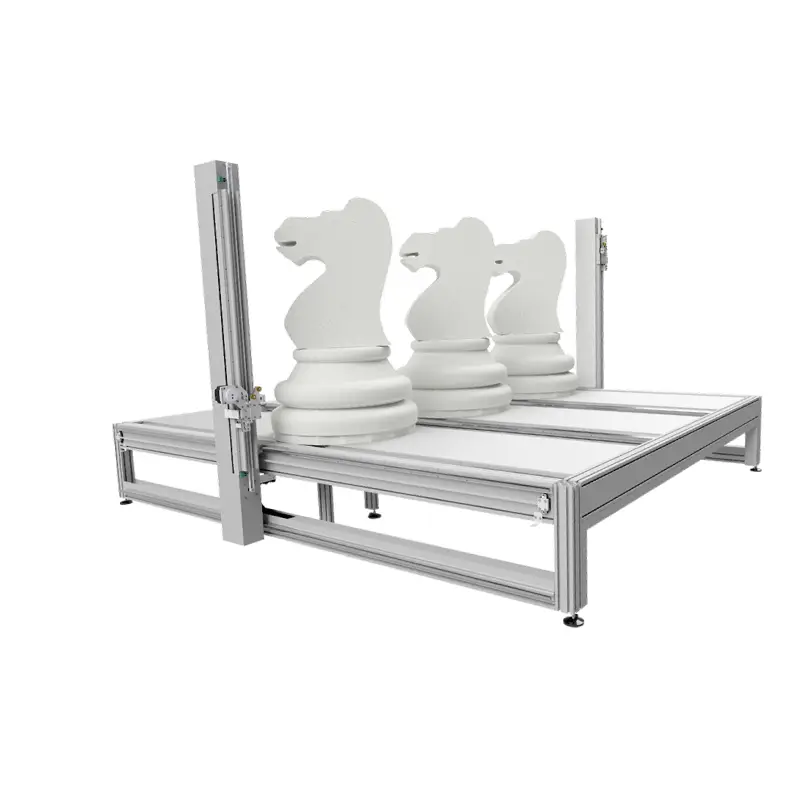
3D CNC Foam Cutting Machine
We offer cutting-edge 3D CNC foam cutting machines. These advanced tools allow you to create complex, three-dimensional foam shapes with precision and speed. From prototypes to finished products, our machines deliver exceptional results, elevating your manufacturing capabilities.
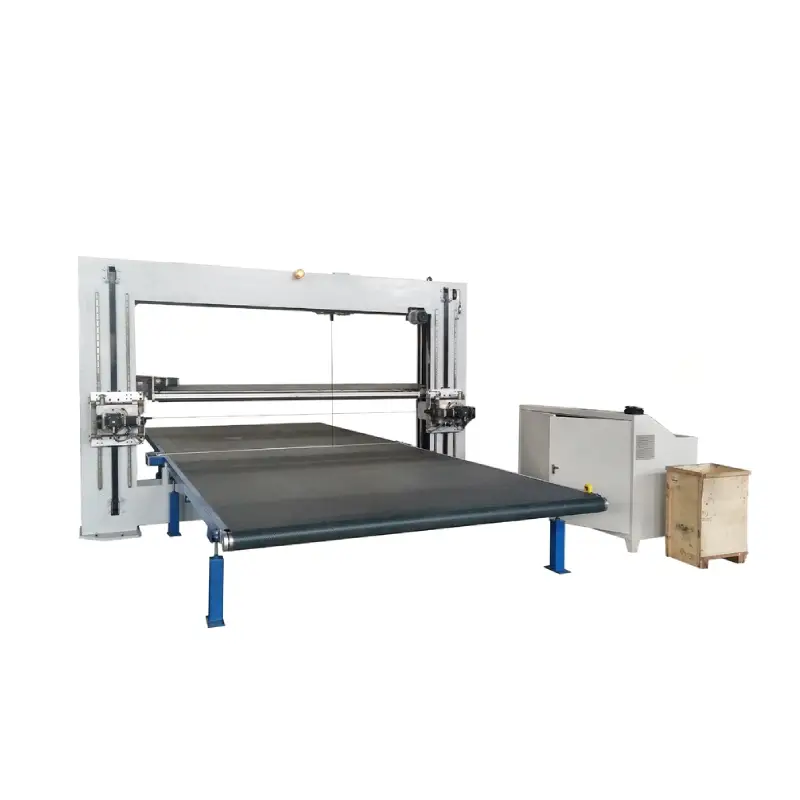
CNC Contour Foam Cutting Machine
We provide high-performance CNC foam contour cutting machine, designed to deliver exceptional precision and efficiency. Our CNC foam cutting machines excel in creating intricate 2D and 3D foam shapes, ideal for industries such as packaging, automotive, and aerospace. Experience the future of foam cutting with our advanced technology.
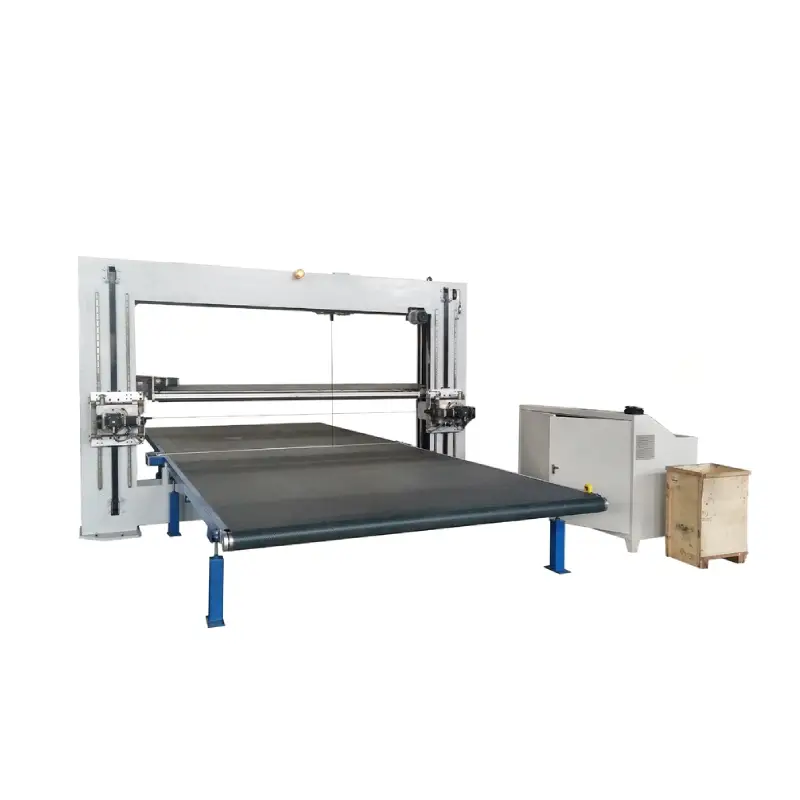
CNC Hot Wire Foam Cutting Machine
We offer hotwire CNC foam cutting machine. These machines utilize a heated wire to precisely cut expanded polystyrene (EPS) and other foam materials. With advanced CNC control, you can create intricate designs and complex shapes with ease. Our machines are ideal for a wide range of applications, including prototyping, packaging, and architectural modeling.
FAQs about CNC Foam Cutting Machine
What is CNC Technology?
CNC stands for Computer Numerical Control. It’s a manufacturing process that uses computers to control machine tools, like lathes, mills, and routers. These machines follow precise instructions to cut, shape, and drill materials like metal, wood, plastic, and foam. CNC technology has revolutionized manufacturing by increasing accuracy, efficiency, and production speed.
Can a CNC machine cut foam?
Yes, a CNC machine can cut foam.
In fact, it’s a common application for CNC machines, especially for creating custom shapes and intricate designs. CNC routers are particularly well-suited for cutting foam, as they can use a variety of cutting tools to achieve precise results.
Here are some common methods for cutting foam with a CNC machine:
- CNC Router: This is a popular choice for cutting foam, as it can use a variety of cutting tools, including end mills and router bits, to create intricate shapes and designs.
- CNC Hot Wire Cutter: This specialized machine uses a heated wire to cut foam, making it ideal for creating smooth, clean cuts in expanded polystyrene (EPS) foam.
- CNC Laser Cutter: While less common for foam cutting, laser cutters can be used to create precise cuts in certain types of foam.
Key advantages of using a CNC machine for foam cutting:
- Precision: CNC machines can create highly accurate cuts, ensuring consistent results.
- Efficiency: CNC machines can automate the cutting process, saving time and labor.
- Versatility: CNC machines can cut a wide variety of foam materials and shapes.
- Repeatability: CNC machines can produce identical cuts, making them ideal for mass production.
CNC machines offer a versatile and efficient solution for cutting foam, making them a valuable tool for a wide range of industries, including manufacturing, prototyping, and arts and crafts.
What are the settings for CNC foam cutting?
The optimal CNC foam cutting settings can vary depending on the specific machine, foam type, and desired cut quality. However, here are some general guidelines and tips:
Spindle Speed (RPM):
- Lower RPM: Typically around 10,000 RPM or less. Lower RPMs help prevent excessive heat buildup and melting of the foam.
- Higher RPM: Can be used for harder foams or for achieving a smoother finish, but be cautious of potential melting.
Feed Rate:
- Faster Feed Rate: Generally, a faster feed rate is acceptable for foam cutting, around 100 inches per minute or more.
- Slower Feed Rate: For intricate details or delicate cuts, a slower feed rate may be necessary.
Bit Selection:
- Sharp, Single-Flute Bits: These are ideal for clean cuts and reducing heat buildup.
- Multi-Flute Bits: Can be used for faster cutting but may require more power and can generate more heat.
Depth of Cut:
- Shallow Cuts: For delicate foams or intricate designs, take shallow cuts to avoid excessive material removal.
- Deeper Cuts: For thicker foam, multiple passes may be necessary to achieve the desired depth.
Other Considerations:
- Foam Type: Different foam types have varying densities and cutting characteristics. Adjust settings accordingly.
- Machine Power: A more powerful machine can handle higher feed rates and deeper cuts.
- Cooling: Adequate cooling can help prevent overheating and improve cut quality.
- Test Cuts: Always perform test cuts on scrap foam to fine-tune settings before cutting your final piece.
Additional Tips:
- Secure the Foam: Ensure the foam is securely clamped to the machine bed to prevent movement during cutting.
- Use a Vacuum Table: A vacuum table can help hold the foam in place and improve cut quality.
- Clean the Bit: Regularly clean the cutting bit to remove foam debris and maintain sharpness.
- Monitor the Cutting Process: Keep an eye on the cutting process to identify any issues or adjustments needed.
By carefully considering these factors and experimenting with different settings, you can achieve optimal results for your CNC foam cutting projects.
What speed is CNC foam cutting?
The speed of CNC foam cutting depends on several factors, including:
- Foam type: Different foam types have varying densities and cutting characteristics. Softer foams can be cut at higher speeds, while denser foams may require slower speeds.
- Machine power: A more powerful machine can handle higher speeds and deeper cuts.
- Cutting tool: The type of cutting tool used (e.g., end mill, router bit, hot wire) and its sharpness will affect the cutting speed.
- Desired cut quality: For intricate details or a smooth finish, slower speeds may be necessary.
General guidelines:
- Spindle speed (RPM): Typically around 10,000 RPM or less. Lower RPMs help prevent excessive heat buildup and melting of the foam.
- Feed rate: Generally, a faster feed rate is acceptable for foam cutting, around 100 inches per minute or more. However, for intricate details or delicate cuts, a slower feed rate may be necessary.
It’s important to perform test cuts on scrap foam to fine-tune the settings and achieve the desired results.
Remember, the optimal settings will vary depending on your specific project requirements.
What blade should I use to cut foam?
The best blade for cutting foam depends on the type of foam and the desired cut quality. Here are some common options:
For general foam cutting:
- Utility knife: A sharp utility knife with fresh blades is a versatile tool for cutting foam board and other types of foam.
- Craft knife: A craft knife with a sharp blade is ideal for making precise cuts in foam.
For denser foam:
- Saw blade: A fine-tooth saw blade can be used to cut through denser foam, such as rigid foam insulation.
For expanded polystyrene (EPS) foam:
- Hot wire cutter: A hot wire cutter is the best tool for cutting EPS foam. It uses a heated wire to melt the foam as it cuts, resulting in a clean and precise cut.
Additional tips:
- Sharp blades: Always use sharp blades to avoid tearing the foam.
- Test cuts: Perform test cuts on scrap foam to determine the best blade and settings for your specific project.
- Clean cuts: Use a slow, steady motion when cutting foam to avoid chipping or tearing.
- Dust: Be aware that cutting foam can create dust, so it’s a good idea to wear a mask and work in a well-ventilated area.
By following these tips and choosing the right blade for your project, you can achieve clean, precise cuts in foam.