Geofoam has become an essential material in construction, offering lightweight and versatile solutions for a variety of projects. However, managing the cost of geofoam can be challenging, especially for large-scale endeavors. In this article, the focus is on understanding the top 10 factors that affect geofoam cost, providing valuable insights for project managers, engineers, and contractors.
By examining these key elements, readers will gain a clearer perspective on budgeting for geofoam, enabling them to make informed decisions and optimize their project expenditures. Whether it’s material density, supplier choices, or installation complexities, each factor plays a crucial role in determining the overall cost, and this comprehensive guide aims to shed light on these critical aspects.
What Is Geofoam?
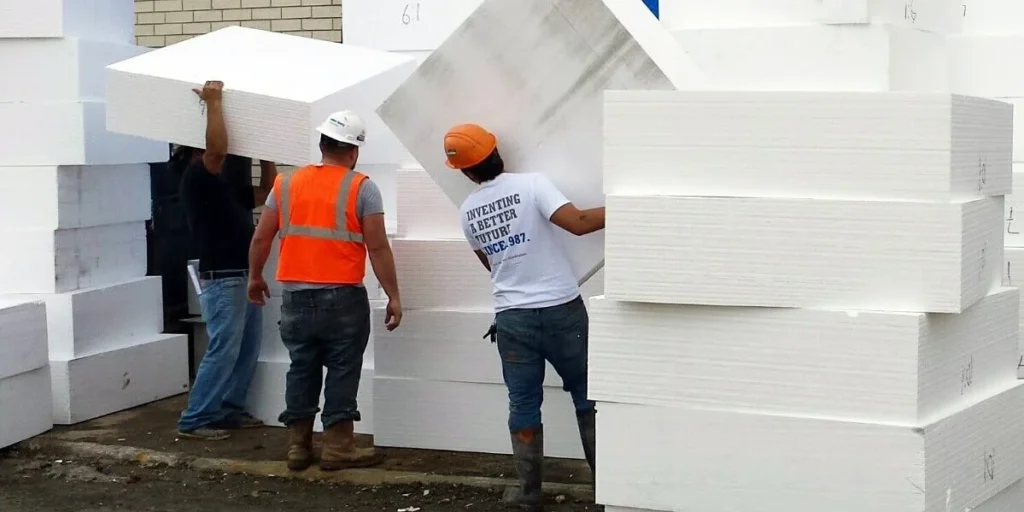
Geofoam is a lightweight, engineered foam material commonly used in construction for soil stabilization, road embankments, and foundation support. Made from expanded polystyrene (EPS), geofoam is prized for its high compressive strength, low weight, and ease of installation. It effectively reduces stress on underlying soils and structures, making it ideal for projects in challenging environments.
Understanding geofoam cost is crucial for project planning, as factors like material density, project size, and suppliers can significantly impact the budget. By considering these elements, construction professionals can optimize geofoam cost and enhance overall project efficiency.
Top 10 Factors Affecting Geofoam Cost
1. Material Density
When considering geofoam for your construction projects, understanding its density is crucial. Geofoam comes in a range of densities, typically from 10 to 40 kilograms per cubic meter (kg/m³). Lower-density geofoam, like 10 kg/m³, is lightweight and cost-effective, making it ideal for applications where weight reduction is key, such as filling voids behind retaining walls.
However, it offers less compressive strength. In contrast, higher-density geofoam, around 40 kg/m³, is stronger and more durable, suitable for supporting heavy loads in road embankments or under foundations. Keep in mind that higher density usually means higher costs due to increased material and manufacturing expenses.
Choosing the right density of geofoam is essential for balancing performance needs and budget considerations in your construction projects.
2. Project Size And Scope
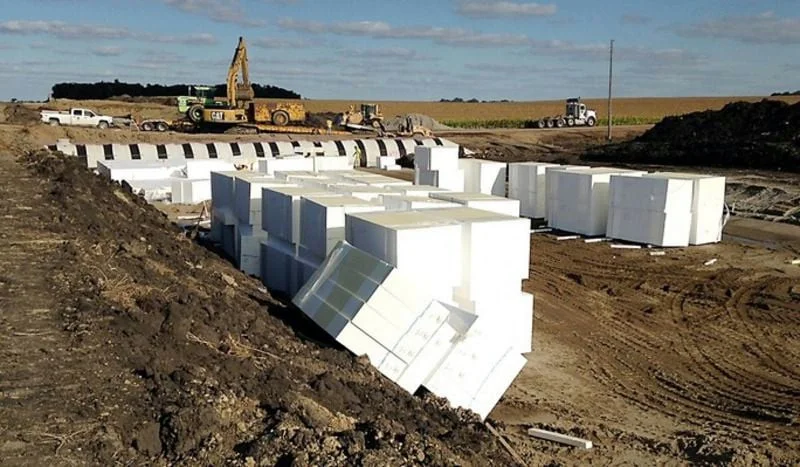
Considering the size and scope of your construction project plays a significant role in determining geofoam requirements and costs. Larger projects typically demand more geofoam to cover expansive areas or support heavier structures, affecting overall material expenses. Economies of scale often apply, meaning larger quantities may lower the per-unit cost of geofoam, benefiting your budget.
Conversely, smaller projects may incur higher costs per unit due to less bulk purchasing power. Understanding these dynamics helps in optimizing geofoam cost management and aligning expenses with your project’s specific needs and goals.
3. Geofoam Type And Grade
Choosing geofoam for your construction projects, and understanding the different types and grades is crucial for managing costs effectively. Geofoam comes in various types and grades, each tailored to specific applications and performance requirements. Lower-grade geofoams are typically less expensive but may offer reduced compressive strength and durability, suitable for lighter applications like void filling.
In contrast, higher-grade geofoams are engineered for greater strength and longevity, making them ideal for heavy-duty projects such as road embankments or foundation support. The cost difference between these types reflects their varying material quality and performance capabilities, allowing you to select the most cost-effective option that meets your project’s needs while optimizing geofoam cost management.
4. Supplier And Manufacturer
Selecting the right supplier and manufacturer is vital for controlling geofoam costs in your construction projects. Suppliers and manufacturers set the pricing based on factors like production efficiency, material quality, and sourcing strategies. Their role in pricing means that an efficient and reputable supplier can offer more competitive rates, superior product quality, and dependable delivery schedules.
Choosing a reliable supplier minimizes the risk of project delays and unexpected expenses, which can significantly impact your budget. By partnering with a trustworthy supplier, you enhance cost efficiency, ensuring your project remains within budget and progresses smoothly. Prioritizing a reliable supplier helps you manage geofoam cost-effectively, contributing to the overall success of your construction endeavors.
5. Transportation And Logistics
Understanding transportation and logistics is crucial for managing geofoam cost-effectively in your projects. Transporting geofoam to your project site involves several costs, influenced by factors like distance, delivery method, and fuel prices. Longer distances typically increase transportation costs, while choosing the right delivery method, such as bulk shipping or optimized routing, can help reduce expenses.
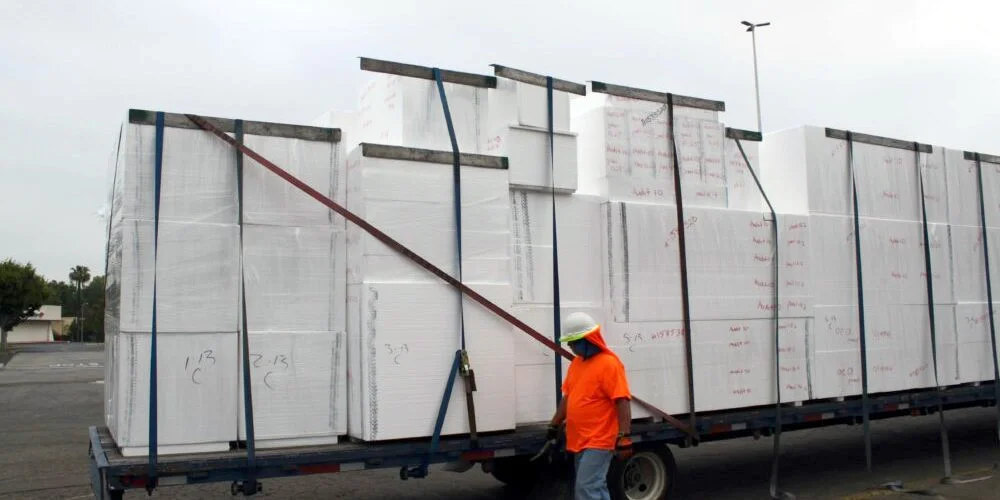
Additionally, fuel costs and logistical challenges, such as accessibility of the site, can impact overall transportation costs. By carefully planning and selecting efficient transportation options, you can better manage geofoam costs, ensuring your project stays within budget and on schedule. Effective logistics planning is key to minimizing these expenses and maximizing the efficiency of your geofoam usage.
6. Installation Costs
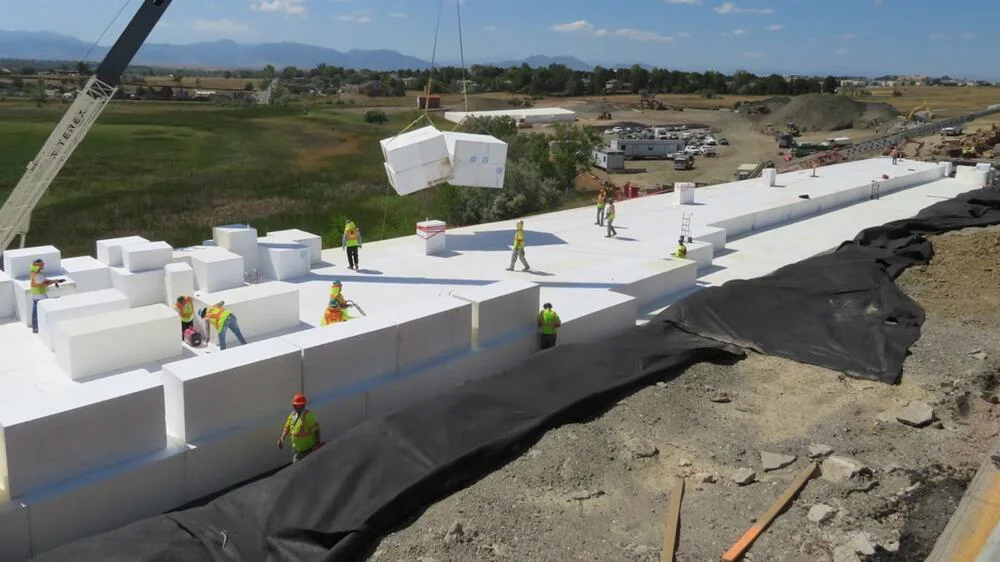
Managing installation costs is crucial for controlling overall geofoam costs in your projects. Labor costs for installing geofoam can vary significantly based on the complexity of the installation. Simple installations, like basic void filling, tend to have lower labor costs.
However, more complex applications, such as intricate foundation supports or multi-layered road embankments, require skilled labor and precise execution, driving up costs. The complexity of the installation influences the time and expertise needed, directly impacting the overall geofoam cost.
By planning efficiently and possibly investing in trained labor or specialized equipment, you can streamline the installation process, reducing labor expenses and ensuring your project stays within budget. Proper management of installation costs is essential for maximizing the cost-efficiency of your geofoam usage.
7. Local Regulations And Standards
Compliance with local building codes and regulations ensures the safety and legality of your project but can also impact overall costs. Meeting these standards may require specific types of geofoam, additional testing, or specialized installation techniques, all of which can increase expenses.
However, adhering to these regulations helps prevent fines, project delays, and potential rework, ultimately saving money in the long run. By staying informed about local requirements and incorporating them into your project planning, you can effectively manage geofoam cost, ensuring a smooth and compliant construction process. Balancing compliance with cost efficiency is key to successful project execution.
8. Environmental And Site Conditions
Site-specific conditions, such as soil type, moisture levels, and terrain, can significantly influence the amount and type of geofoam needed. For instance, high moisture areas may require special geofoam treatments or additional protective measures to ensure durability and performance, leading to increased costs. Challenging terrains might also necessitate more complex installation processes, adding to labor expenses.
By thoroughly assessing your site’s conditions and planning accordingly, you can anticipate these additional expenses and optimize geofoam costs. This careful consideration helps ensure that your project remains within budget while effectively addressing the unique challenges of your site.
9. Market Demand And Supply
Market conditions significantly influence geofoam pricing, with high demand often driving up costs. When demand surges, prices can rise due to the increased competition for available materials. Conversely, in periods of low demand, prices may drop, offering potential cost savings.
Supply chain disruptions, such as raw material shortages or transportation delays, can also impact geofoam costs by limiting availability and increasing prices. Staying informed about market trends and maintaining good relationships with suppliers can help you anticipate price changes and plan your purchases more effectively, ensuring your project remains within budget despite market fluctuations.
10. Customization And Special Requirements
When incorporating customized geofoam solutions into your project, it’s essential to understand how these choices affect geofoam cost. Customization, whether for specific shapes, sizes, or densities, generally increases costs due to the additional manufacturing processes involved. Special requirements, such as enhanced fire resistance or greater durability, also add to the expense.
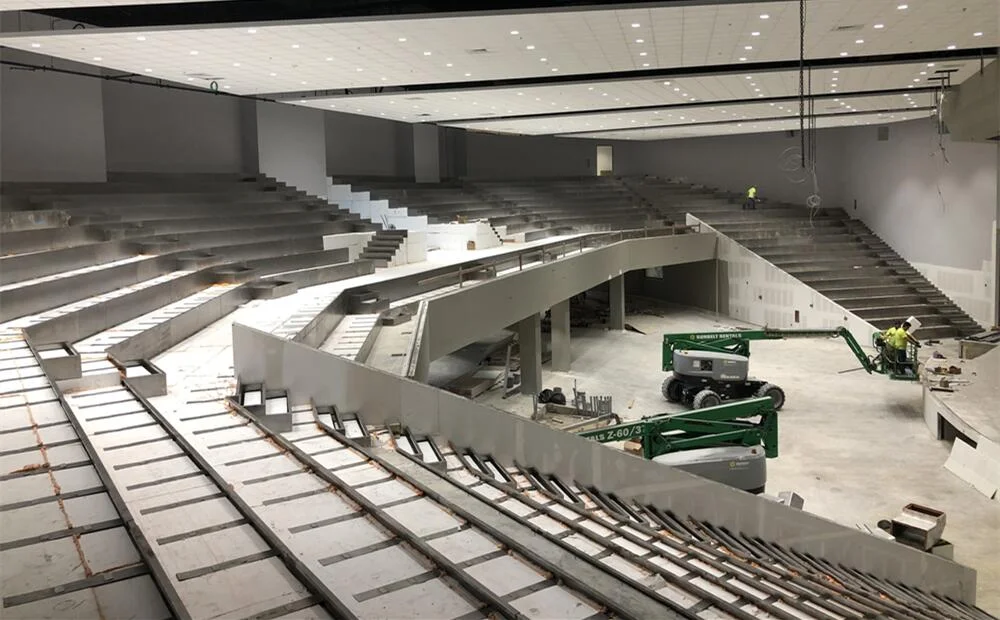
These features necessitate the use of specialized materials and production techniques, driving up the overall cost. However, these customized solutions often provide significant benefits, such as improved safety and longevity, which can justify the higher initial investment.
By carefully evaluating your project’s needs and balancing them with budget considerations, you can optimize geofoam cost while ensuring the customized features meet your specific requirements.
How To Reduce Geofoam Cost In Your Projects?
To effectively reduce geofoam costs in your construction projects, strategic planning and smart decisions are crucial. Begin by conducting a thorough assessment of your project’s requirements to accurately determine the amount of geofoam needed, thereby preventing unnecessary purchases. Take advantage of bulk purchasing opportunities to secure discounts from suppliers, ensuring you get the best possible price per unit.
Compare quotes from multiple suppliers to find competitive rates without compromising on quality. Selecting the appropriate type and grade of geofoam tailored to your project’s specifications is essential. Opt for standard options that meet performance requirements while minimizing costs. Implement efficient installation practices to reduce labor expenses and minimize material waste during application.
Consider sourcing geofoam locally to cut down on transportation costs and support regional suppliers. Additionally, explore the feasibility of utilizing recycled geofoam, which can offer cost savings while promoting sustainability. Leverage technology for precise geofoam calculation and placement, optimizing material usage and minimizing errors.
Stay informed about market trends and fluctuations in geofoam prices to make informed purchasing decisions and capitalize on cost-saving opportunities. By integrating these strategies into your project planning and execution, you can effectively manage and reduce geofoam costs while maintaining high standards of quality and efficiency throughout your construction endeavors.
Conclusion
In conclusion, understanding the top 10 factors affecting geofoam cost is crucial for optimizing construction project budgets. Factors such as material density, project size, geofoam type, supplier selection, transportation logistics, installation practices, local regulations, environmental conditions, market demand, and customization requirements all significantly impact costs.
By carefully considering these elements, professionals can make informed decisions, ensuring cost-effective and successful project outcomes. This insight aids in precise budgeting and efficient resource management.