Lost foam casting is a versatile and innovative casting process that has revolutionized the manufacturing industry. This method allows for the production of complex and intricate metal parts with high precision and minimal waste. Understanding lost foam casting is essential for industries that demand high-quality and cost-effective metal components.
What Is Lost Foam Casting
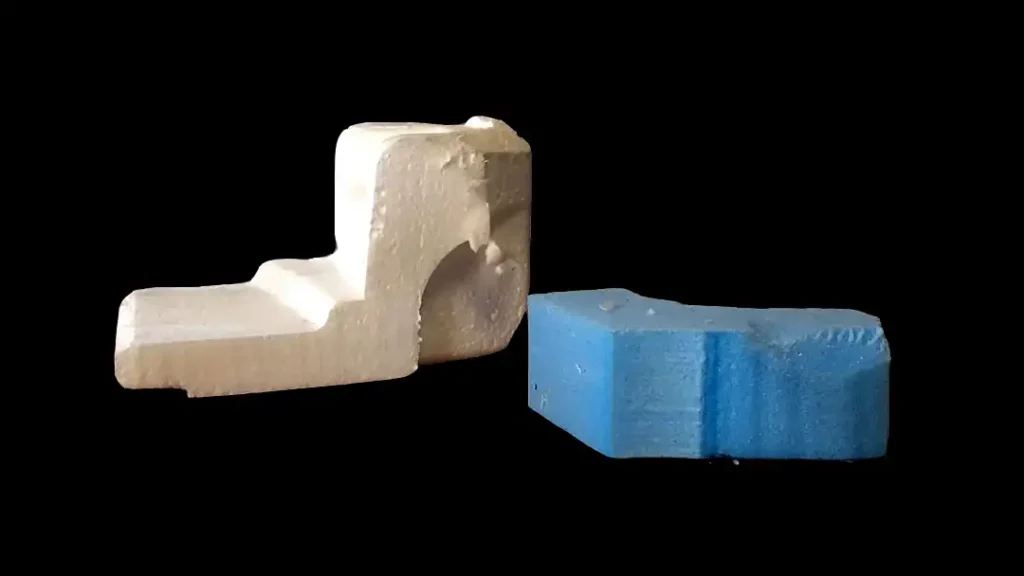
Lost foam casting is a type of evaporative-pattern casting process that utilizes foam patterns to create metal parts. The foam pattern, typically made from polystyrene, is coated with a refractory material and then buried in sand. When molten metal is poured into the mold, the foam vaporizes, leaving behind a cavity that is filled by the metal, thus forming the final cast part.
Lost-foam casting (LFC) is a type of evaporative-pattern casting process that is similar to investment casting except foam is used for the pattern instead of wax. This process takes advantage of the low boiling point of polymer foams to simplify the investment casting process by removing the need to melt the wax out of the mold.
source: https://en.wikipedia.org/wiki/Lost-foam_casting
What Is the Origin of Lost-Foam Casting?
The origin of lost-foam casting can be traced back to a patent filed by H.F. Shroyer in April 1956. Shroyer proposed a novel idea of embedding foam patterns within green sand to facilitate metal casting.
This inventive approach involved cutting a pattern from expanded polystyrene (EPS) and supporting it with bonded sand throughout the casting process. Shroyer’s innovative technique, which was formally patented in 1958, laid the foundation for what is now known as lost-foam casting, also referred to as the whole-mold technique. This method revolutionized the casting industry by enabling the production of complex and precise metal parts with high efficiency and reduced waste.
Importance of Lost Foam Casting
Lost-foam casting is highly significant in manufacturing due to its ability to produce complex and intricate metal parts with high precision and minimal material waste. This method offers several advantages over traditional casting techniques, making it invaluable for industries that require detailed and high-quality components.
One of the primary benefits of lost-foam casting is its cost-effectiveness. By reducing the need for machining and finishing operations, it lowers production costs and improves overall efficiency. Additionally, the process minimizes defects and ensures tight tolerances, which are crucial for applications in automotive, aerospace, and heavy machinery industries. The versatility and accuracy of lost-foam casting enable manufacturers to create parts with complex geometries that would be difficult or impossible to achieve with other casting methods, thereby enhancing design flexibility and innovation in product development.
Key Principles of Lost Foam Casting
The Role of Foam Patterns
Foam patterns are the core of the lost foam casting process. These patterns are meticulously designed and crafted to match the exact specifications of the desired metal part. The accuracy of the foam pattern directly impacts the quality of the final cast product.
Refractory Coating
The refractory coating applied to the foam pattern serves multiple purposes. It protects the foam from the molten metal’s heat, ensures a smooth surface finish on the cast part, and facilitates the escape of gases during the casting process.
Sand Molding
The sand used in lost foam casting must be fine and uniform to ensure that it can compact tightly around the foam pattern. Proper sand molding is crucial for supporting the foam pattern and maintaining its shape during metal pouring.
How Lost Foam Casting Works
Pattern Creation
The process begins with the creation of a foam pattern, typically using expanded polystyrene (EPS). This pattern is an exact replica of the part to be cast and includes all necessary design features and details.
Coating Application
Once the foam pattern is prepared, it is coated with a refractory material. The coating must be applied evenly to ensure proper protection and gas permeability. This step is critical for achieving a high-quality surface finish on the final cast part.
Mold Assembly
After the coating dries, the foam pattern is placed in a flask, and fine sand is compacted around it. The sand must be tightly packed to support the foam pattern during the metal pouring process. This step ensures that the pattern remains stable and maintains its shape.
Metal Pouring
Molten metal is then poured into the mold. As the metal flows into the mold, it vaporizes the foam pattern, filling the cavity left behind. The metal must be poured at the correct temperature and rate to ensure complete pattern vaporization and proper filling of the mold cavity.
Cooling and Solidification
Once the mold is filled, the metal is allowed to cool and solidify. Proper cooling is essential to prevent defects and ensure the integrity of the cast part. The cooling rate can be controlled to achieve the desired mechanical properties in the final product.
Mold Breakout
After the metal has solidified, the sand mold is broken away to reveal the cast part. Any remaining sand and refractory coating are removed through various cleaning processes. The cast part is then inspected for quality and any necessary finishing touches are applied.
What is the Lost Foam Casting Process
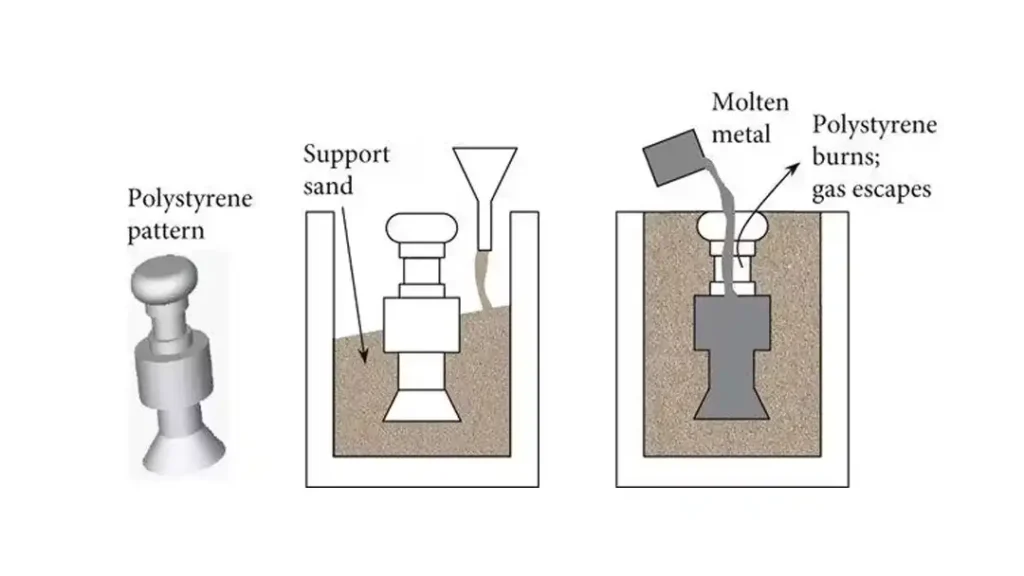
Lost-foam casting is a sophisticated manufacturing process that allows for the creation of intricate metal parts through a series of carefully executed steps. Here’s a detailed explanation of the procedure:
Foam Pattern and Gating System Production:
The process begins with the creation of foam patterns that replicate the precise geometry of the final metal object. These foam patterns also include gating systems, which are passages designed to direct the flow of molten metal into the mold. These gating systems can either be integrated into the foam pattern itself or attached separately (glued on). This setup ensures precise designs and efficient metal flow during casting.
Assembly of Mold Bundle Module:
Once the foam patterns and gating systems are prepared, they are tightly bonded together to form a mold bundle module. This assembly is crucial as it ensures that all components are correctly aligned, reducing errors and facilitating consistent manufacturing of complex metal parts.
Application of Refractory Dip Paint:
After the assembly, the mold bundle module is coated with refractory dip paint. This paint forms a protective ceramic coating once dried, enhancing the mold’s surface durability, heat resistance, and capability to withstand the temperature and pressure of molten metal during casting.
Placement in Molding Flask and Sand Filling:
The coated mold bundle module is placed inside a molding flask, and dry sand is packed around it. This step is essential to support the shape of the module, keep it securely in place during casting, and ensure uniform compaction of the sand.
Vibration and Sand Compaction:
Vibrations are applied to the molding flask to facilitate the flow of sand into every intricate detail of the mold bundle module. This process compacts the sand tightly around the module, eliminating air pockets and ensuring the creation of a high-quality mold with precise dimensions and fine details.
Pouring of Molten Metal:
Once the mold is prepared, molten metal is carefully poured into the mold cavity. The high temperature of the metal vaporizes the foam patterns within the mold bundle module, leaving behind a cavity that matches the exact shape of the original foam patterns. As the metal solidifies, it forms the desired casting, replicating the intricate details and complex shapes of the foam patterns.
Cleaning and Finishing:
After the metal has cooled and solidified, the mold is broken away to reveal the cast metal part. The casting is then cleaned to remove any remaining sand, ceramic shells, or other impurities. This cleaning process ensures that the final castings meet quality standards, have smooth surfaces, and are ready for subsequent finishing operations or assembly.
The lost-foam casting process is highly efficient, reducing labor requirements and waste production. It also allows for the recycling of used dry sand, aligning with sustainability goals by minimizing emissions and energy consumption in manufacturing operations. This method is particularly valued for its ability to produce complex shapes and intricate details with high precision, making it indispensable in industries requiring advanced metal components.
Applications of Lost Foam Casting
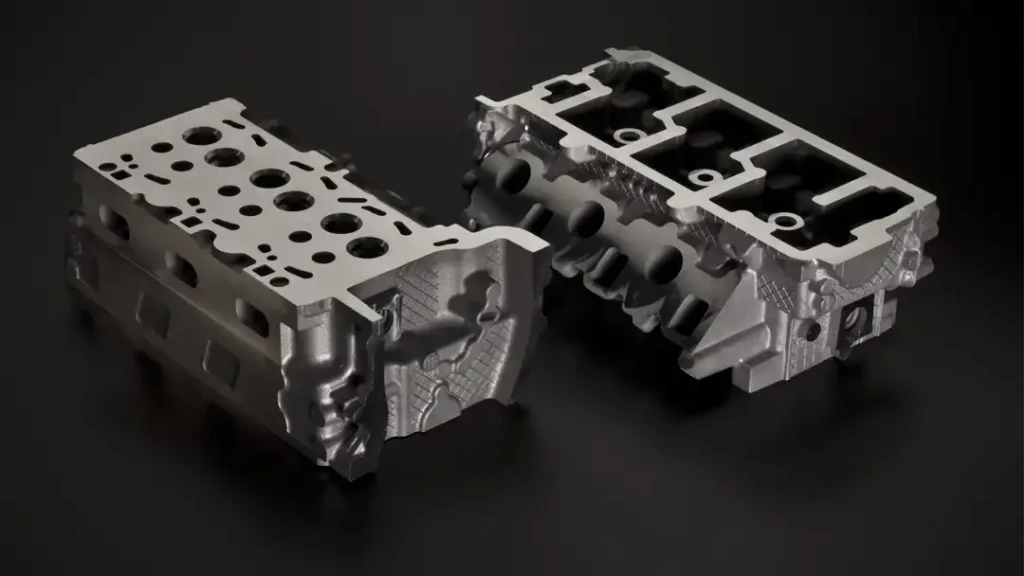
Automotive Industry
In the automotive industry, lost foam casting is used to produce engine blocks, cylinder heads, and other critical components. The process’s precision and ability to produce complex geometries make it ideal for automotive applications.
Aerospace Industry
Lost foam casting is also prominent in the aerospace sector, where it is used to create lightweight and high-strength components for aircraft engines and structural parts. The method’s accuracy and ability to produce parts with intricate details are highly valued.
Heavy Machinery
Heavy machinery manufacturers use lost foam casting to produce large and complex parts such as pump housings, valve bodies, and gearboxes. The process’s efficiency and cost-effectiveness are significant advantages in this industry.
Art and Sculpture
Artists and sculptors utilize lost foam casting to create detailed and intricate metal artworks. The ability to replicate fine details and the flexibility in design make it a preferred method for metal sculptures.
Advantages of Lost Foam Casting
High Precision and Accuracy
One of the primary advantages of lost foam casting is its ability to produce highly precise and accurate metal parts. The foam patterns allow for intricate details and tight tolerances, resulting in parts that meet exact specifications.
Cost-Effectiveness
Lost foam casting is cost-effective due to the reduced need for machining and finishing operations. The process minimizes material waste and can produce parts with minimal defects, reducing overall production costs.
Design Flexibility
The lost foam casting process offers significant design flexibility. Complex geometries and intricate details that would be difficult or impossible to achieve with traditional casting methods can be easily produced using lost foam casting.
Reduced Waste
The use of foam patterns and precise molding techniques reduces material waste in lost foam casting. This efficiency not only lowers costs but also makes the process more environmentally friendly compared to other casting methods.
What Are the Metals Used in Lost-Foam Casting
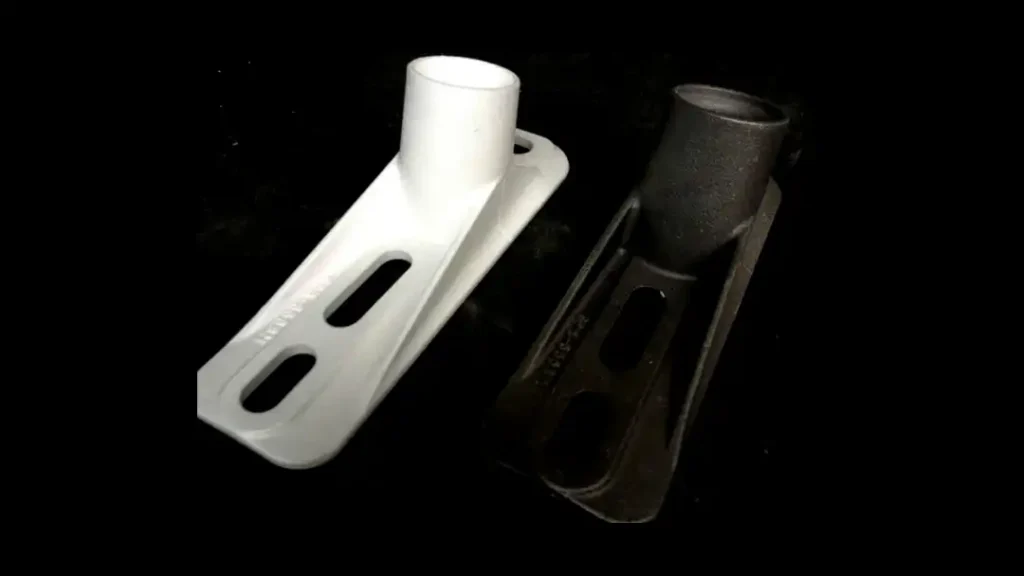
Lost-foam casting utilizes a variety of metals, each chosen for its specific properties and suitability for different applications:
Stainless Steel:
Stainless steel, composed primarily of iron and chromium, is renowned for its exceptional corrosion resistance and strength. It is preferred in applications requiring both durability and aesthetic appeal. During the lost-foam casting process, molten stainless steel is poured into the foam mold, replacing the evaporated foam to form intricate shapes. While stainless steel may be more costly and challenging to work with, its high strength and corrosion resistance make it indispensable in various industries.
Aluminum Alloys:
Aluminum alloys combine aluminum with other elements to achieve a balance of lightweight properties and effective thermal conductivity. In lost-foam casting, these alloys are used where parts require specific strength-to-weight ratios. Their lightweight nature and good thermal properties are advantageous, though they may have limitations in applications requiring extremely high strength. Aluminum alloys are widely utilized across industries for their versatility and performance characteristics.
Nickel Alloys:
Nickel alloys are prominent in lost-foam casting for their exceptional resistance to high temperatures and corrosion. These alloys are favored in extreme environments and specialized applications where robust performance is critical. Nickel alloys offer unique properties but require careful consideration of cost and alloy selection to match specific application needs effectively.
Steels:
Steels encompass a broad range of alloys tailored for specific applications in lost-foam casting. These alloys vary in strength, hardness, and wear resistance, catering to diverse industrial needs. While offering a spectrum of advantageous properties, precise alloy selection is crucial to meet specific application requirements effectively. Steels are extensively used in automotive, aerospace, and machinery sectors for their reliability and mechanical properties.
Cast Irons:
Cast irons, including variations like gray iron and ductile iron, are crucial in lost-foam casting due to their high compressive strength and wear resistance. They excel in heavy-duty applications where durability and toughness are paramount. However, achieving optimal results with cast irons requires meticulous control and consideration during the casting process to manage their unique properties effectively.
Each metal used in lost-foam casting plays a distinct role, offering a combination of mechanical properties, durability, and performance characteristics suited to diverse industrial requirements.
Difference Between Lost-Foam Casting vs Sand Casting
Both lost-foam casting and sand casting have their strengths and are selected based on the specific requirements of the part being produced, including complexity, size, finish, and cost considerations.
Aspect | Lost-Foam Casting | Sand Casting |
---|---|---|
Process | Uses foam patterns coated with refractory material. Molten metal vaporizes the foam to create the component. | Employs compacted sand molds to capture patterns and define part shape, with sand removed after solidification. |
Complexity | Ideal for producing intricate, detailed, and complex parts easily. | Best suited for simpler, larger parts due to molding constraints. |
Surface Finish and Tolerance | Delivers smooth surface finishes and precise dimensions. | Typically results in rougher surfaces and less precise tolerances. |
Cost and Tooling | The cost of foam patterns is offset by avoiding complex mold-making; generally higher upfront costs. | More cost-effective for low to medium production volumes with cheaper pattern materials. |
Part Size and Weight | Suitable for both small and large parts. | Optimal for larger components, especially in heavy machinery. |
Conclusion
Lost foam casting is a transformative process in the manufacturing industry, offering numerous advantages in terms of precision, cost-effectiveness, and design flexibility.
As technology advances and new innovations emerge, the future of lost foam casting looks bright, with increasing applications across various sectors. Understanding this process is essential for industries that demand high-quality and efficient production of metal components.